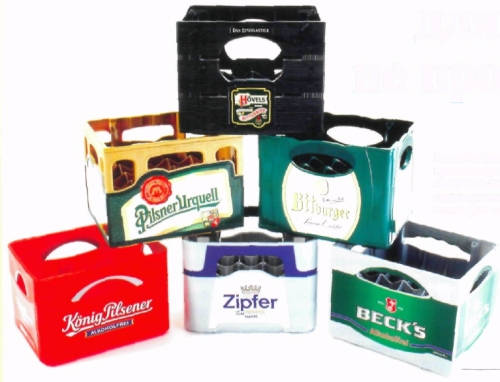
В последние годы дизайн ящиков для бутылок с напитками претерпел существенные изменения, Из простых по конструкции и зачастую неудобных в обращении транспортных контейнеров они постепенно превратились в многофунк-циональные и удобные для переноски полимерные изделия с эстетичным внешним видом, которые все чаще используются расфасовывающими напитки предприятиями в качестве средства маркетинга и даже презентации новых напитков. На смену традиционным однокомпонентным ящикам пришли многокомпонентные, и выбор наиболее приемлемой технологии их изготовления становится непростой задачей и зависит от многих факторов. В статье, на основе обширного опыта, накопленного в этой области фирмой Haidlmair Werkzeugbau GmbH (г. Нуссбах, Австрия), обобщаются возможные варианты дизайна и методов изготовления современных ящиков для бутылок. Начиная с 1970-х гг. изготавливаемый литьем под давлением однокомпонентный ящик из полимерных материалов (ПМ) постепенно вытеснил обычные де¬ревянные ящики для пивных или других бутылок. По функциональному назначению и внешнему виду такой ящик мало отличался от ящика из древесины, если не считать меньшей массы. Использовавшиеся в то время в Германии и Австрии бутылки для пива были более высокими и тяжелыми, чем современные бутылки. Поэтому и ящики тогда были выше, чем сегодня, и их основное назначение заключалось в предохранении находящихся в них бутылок от повреждений. Твердые, с острыми краями ручки ящиков делали транспортировку бутылок с напитками тяжелой работой и требовали от грузчиков определенного навыка. Это неудобство в обращении с ящиками стало впоследствии причиной изменения формы их ручек, которые стати более округлыми и объемны¬ми. В результате этого увеличилась площадь их контакта с ладонью переносящего ящик человека, и соответственно уменьшилось контактное давление на ладонь. 1. Возможности изготовления однокомпонентных ящиков для бутылок Изготовление литьем под давлением более удобного для переноски ящика, имеющего монолитные ручки с увеличенной площадью поперечного сечения, было связано, однако, с увеличением времени охлаждения и соответственно цикла литья. Чтобы избежать связан¬ного с этим снижения производительности процесса, рассматривались два возможных варианта уменьшения объема материала в зоне ручки и решения тем самым указанной проблемы: изготовление полой ручки с тон¬кой стенкой (рис. I, а) или ручки с многочисленными тонкостенными ребрами для уменьшения локального скопления материала (рис. I, б). В результате тесного сотрудничества технологов и конструкторов литьевых форм оба варианта, требующие более усложненной конструкции литьевых форм, были успешно реализо¬ваны и часто встречаются в настоящее время. В первом случае (см. рис. 1, а) ручки, имеющие совершенно гладкую поверхность в отличие от второго варианта, изготавливаются по газоинжекционной технологии литья (выдувной вариант), при которой впрыск расплава ПМ осуществляется в оформляющую ПОЛОСТЬ формы, часть объема которой (около 50 %) занимает специальный подвижный сегмент. Затем, после Кратковременной паузы, необходимой для некоторого охлаждения и загустевания расплава, сегмент отводится, полностью освобождая оформляющую полость формы, и в расплав ПМ под давлением подается азот, в результате чего происходит образование полости внутри отливки и осуществляется ее выдув.
|