Придание необходимой конфигурации изделию осуществляется или в высокоэластическом состоянии, или несколько выше температуры текучести за счет растяжения полимера, под действием нормальных напряжений. Так как в области высокоэластического состояния деформации обратимы, то в отформованном изделии наблюдаются релаксационные процессы, причем их скорость тем больше, чем выше температура, при которой эксплуатируется изделие. Релаксационные процессы, протекающие во времени, могут привести к изменению формы изделия, особенно при повышенной температуре. «Формоустойчивость» изделия в процессе эксплуатации определяется температурой формования и степенью вытяжки листа при формовании. Температура формующего инструмента (матрицы, пуансона, прижимных рам) должна быть ниже температуры размягчения полимера. Излишнее снижение температуры способствует росту дефектности (морщины, складки), брака (коробление) и усадки; увеличивается доля неотрелаксировавших напряжений; при увеличений Тф выше оптимального значения происходит другое нежелательное явление: увеличивается разнотолщинность стенок изделий. Поэтому температура формы не должна быть ниже 50-70 °С, а для ускорения процесса охлаждения и повышения производительности целесообразно использовать дополнительное воздушное охлаждение или охлаждение с помощью искусственного водяного тумана. При увеличении степени вытяжки заготовки при формовании изделия возрастает ее ударная вязкость. Однако наряду с этим возрастает и вероятность значительной термической усадки изделия. Таким образом, желательно формовать объемные изделия при таких режимах, при которых бы в меньшей степени проявлялись ориентационные процессы. На разнотолщинность изделий влияет также и скорость формования Vф. Медленная вытяжка сопровождается существенным охлаждением различных областей формуемого изделия, что ведет к увеличению разнотолщинности. Увеличение Vф способствует получению более равнотолщинных изделий. Одна из важнейших и наиболее длительная стадия технологического процесса - разогрев заготовки. Температурное поле разогретой заготовки должно быть максимально однородным как по ее поверхности, так и по толщине, но это затрудняется вследствии низкой тепло- и температуропроводности полимеров. Большинство машин и установок для вакуумформования оснащено тепло-радиационными инфракрасными нагревателями; температуру заготовки можно регулировать изменением интенсивности нагрева по зонам и расстояния нагревателя от поверхности листа. Кроме того, нагрев листовых заготовок (особенно большой толщины) может осуществляться в нагревателях камерного типа или контактным способом с помощью нагреваемых плит. В целом с повышением температуры формования механические характеристики готового изделия снижаются, а усадка растет. В зависимости от характера взаимодействия формуемого материала с формой различают свободное негативное и позитивное формование листовых заготовок. Свободное формование осуществляется без соприкосновения формуемого материала заготовки с оформляющим инструментом. Его применение ограничено изготовлением из прозрачных акрилатов крупногабаритных изделий овальной формы для обтекателей и световых фонарей с улучшенными оптическими характеристиками. При использовании метода требуется высокая равномерность нагрева заготовки с минимальной разнотолщинностью - в противном случае искажается форма изделия и его оптические характеристики. Кроме того, применение свободного формования ограничивает и глубину вытяжки. Негативное формование (формование в матрице) позволяет получать изделия, у которых наружная поверхность соответствует геометрии внутренней поверхности матрицы. Нагретая заготовка вначале деформируется свободно, и ее толщина уменьшается относительно равномерно, однако после соприкосновения с формой температура заготовки в этой области резко понижается и дальнейшее деформирование идет неравномерно - толщина стенок и днища оказывается различной. Значительная разнотолщинность - один из существенных недостатков негативного метода формования. 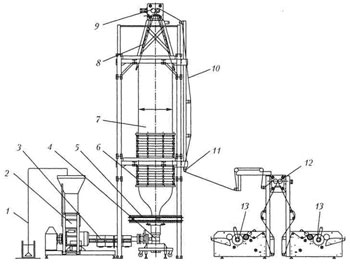 Позитивное формование осуществляется на пуансоне; форму внешней поверхности пуансона повторяет внутренняя поверхность изделия. Нагретая заготовка первоначально соприкасается с верхней поверхностью пуансона; деформация этой зоны прекращается, поэтому образующееся днище имеет наибольшую толщину. Вытяжка остальной части заготовки происходит более равномерно, но, как и при негативном формовании, получение изделия большой глубины и с острыми углами затруднительно.
Наиболее важные характеристики формы — глубина и степень вытяжки, которые обеспечивает конструкция формы. Практически этими параметрами являются высота изделия Н и отношение H/W, где W— ширина изделия. Основная особенность оснастки для этого метода – наличие отверстий диаметром 0,1 – 0,5 мм или щелей в местах перегибов конфигурации изделия. Это необходимо для отвода воздуха при вакуумировании. Охлаждение происходит при соприкосновении заготовки с холодными стенками формы. Для ускорения этой стадии применяют обдув изделия сжатым воздухом. В зависимости от метода формования и конструкции формы, охлаждение бывает односторонним или двухсторонним.
|