Основная особенность этого способа переработки полимерных материалов заключается в том, что формование изделий осуществляется не из расплава, а из заготовок полимерного материала (листа, пленки), нагретых до размягченного состояния, которые затем приложенным усилием оформляются в изделия и затем охлаждаются при сохраняющемся усилии формования (рис. 1). 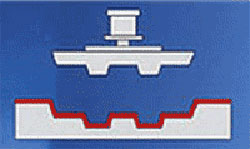
Методом формования изготавливают изделия различной конфигурации, имеющие одинаковую толщину всех стенок (стаканчики, крышки, ячейки для упаковки конфет или медицинских инструментов и т.д.) (рис. 2). Широко применяется вакуумформование для изготовления тонкостенных изделий (упаковочная тара и одноразовая посуда), когда литье под давлением неприменимо из-за малой толщины стенок. Очень выгодно использовать данный метод при мелкосерийном производстве, так как технологическая оснастка намного проще и дешевле, чем литьевые формы. 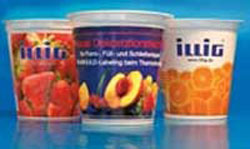
Существенными преимуществами этого метода являются рентабельный инструмент для формования, разумная стоимость вакуумформовочных машин, возможность переработки многослойных и вспененных материалов, а также материалов с предварительно нанесенной на них печатью. Из формуемых материалов с высокой вязкостью расплава могут быть получены чрезвычайно тонкостенные изделия, в то время как при литье под давлением для таких изделий требуется гранулят с низкой вязкостью расплава. Относительно невысокие цены на оснастку дают еще одно преимущество данному методу для производства небольших партий изделий; достоинства вакуумформования для больших партий состоит в достижении очень низких толщин стенок и высокой производительности вакуумформовочных машин. Самые маленькие по размеру детали, производство которых вакуумформованием еще экономически выгодно, это упаковка для таблеток или батареек для часов. Недостатками метода являются: • значительная разнотолщинность изделий, обусловленная различной степенью вытяжки; • невозможность получения изделий сложной конфигурации; • необходимость дополнительной механической обработки изделий; • невозможность переработки листов толщиной более 6 мм; • большое количество отходов (до 50%) при изготовлении изделий с большой глубиной вытяжки. Диапазон толщин формуемых материалов от 0,05 до 15 мм, а для вспененных материалов даже до 60 мм. Любые термопласты или материалы с аналогичными свойствами являются в принципе термоформуемыми. Наибольшее распространение получили листы крупнотоннажных полимеров: ударопрочного полистирола, АБС-пластика, жесткого ПВХ, аморфного ПЭТ. Поликарбонат, ПММА, ПЭНД и ПЭВП, ПП имеют менее широкое применение. При вакуумформовании различают следующую последовательность процессов: • нагревание формуемого материала до температуры, при которой он способен изменять форму, то есть до температуры высокоэластического состояния (для аморфных полимеров) или до температуры приближенной к плавлению кристаллической фазы (для кристаллизующихся полимеров); • формование на специальной оснастке; • охлаждение в форме до температуры, при которой конфигурация отформованного изделия приобретет стабильные размеры; • извлечение из формы изделия со стабильными размерами. В большинстве случаев необходима последующая обработка формованного изделия, а именно: отделка (обрезка); сварка; соединение (склеивание); горячее запаивание; печать; металлизация.
|