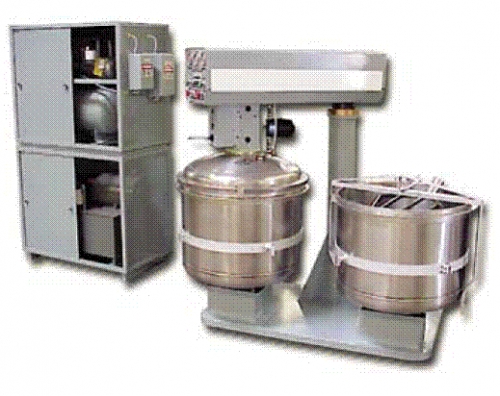
Требуемые смеси могут быть легко запрограммированы на компьютере машины. Спиралеобразные лопасти миксера имеют особый дизайн, который позволяет тщательно перемешивать все виды жидкостей (смолу, красящую пасту, катализатор, ускоритель, различные добавки) с наполнителем. По мере того, как смесь начинает перемешиваться в чаше миксера, вакуумное устройство откачивает весь воздух. Такая подача вакуума очень эффективна, поскольку количество вращающейся смеси относительно небольшое. Машина может вырабатывать давление в 3-4 бар, поэтому Вы можете подключить к ней шланг для инжекции. Несомненно, качество изделий, произведенных с помощью такого миксера, будет отличным. Благодаря тому, что смола внутри миксера нагревается, ее вязкость, соответственно, уменьшается, поэтому содержание наполнителя в смоле может быть очень высоким. За счет этого при изготовлении изделий из искусственного мрамора экономия на смоле позволяет окупить такую машину за 2-3 года. Денежные вложения в такую установку составляют от 150.000 до 300.000 USD, поэтому для ее приобретения необходимо иметь большое производство. Обычно покупатели начинают с малого и покупают миксер небольшого размера. Самая маленькая и самая распространенная модель рассчитана на 100 кг. Это самое скромное вложение денег, которое никогда не пропадет зря. Даже если в дальнейшем покупатель перейдет на производство с помощью машины для непрерывного литья, этот небольшой миксер все еще будет служить для работы с особыми оттенками гранул или же в испытательных целях. На рынке существуют различные модели миксеров, в которых емкость чаши для смешивания увеличивается до 150 и 175 кг, а самая большая модель имеет две чаши емкостью 200 кг. После закрытия крышки миксера чаша начинает вращаться, смола, наполнитель и другие ингредиенты очень тщательно перемешиваются без добавления катализатора. Перемешивающее лезвие непрерывно соскабливает материал со дна и стенок. Крышка миксера закрывается очень плотно, благодаря большому резиновому кольцу. Остальное делает вакуумный насос, откачивающий воздух и создающий небольшой вакуум не более 0,74 бара. Достаточно 10–20 минут перемешивания смеси при воздействии вакуума. Затем миксер и насос отключаются, добавляется немного воздуха и крышка открывается. Теперь настает время добавить отвердитель. После этого смесь перемешивается под вакуумом еще три минуты. Иногда приходилось наблюдать, как полученную смесь переливают в емкости, куда добавляют отвердитель, а затем по очереди перемешивают все компоненты с помощью миксера для краски или обычной электрической дрелью. Не рекомендую так делать, потому что результат, полученный с помощью вакуумного миксера, а именно, отсутствие воздушных пузырьков, полностью аннулируется. Перемешанный в вакуумном миксере материал становится уплотненным. Это гарантирует отсутствие воздушных включений при выливании материала самотеком в матрицы сложной формы. Для ликвидации крупных воздушных пузырьков достаточно на короткое время поместить матрицу на вибростол (не более, чем на 30 секунд). Более длительная вибрация вызовет расслоение компонентов смеси (смолы, гидроксида алюминия и гранул). Наполнитель (смесь полиэфирных гранул разного цвета и гидроксида алюминия) был разработан специально для образования суспензии с высококачественной смолой для изготовления «твердой поверхности», которая имеет более высокую вязкость, чем смола общего назначения. После того, как перемешанный материал помещен в матрицу, необходимо очистить чашу миксера. Эта операция может занять длительное время. Но есть простое специальное устройство, которое очистит чашу биоразрушаемым растворителем менее чем, за 10 минут. Оно подходит для очистки не только чаши, но и всех ручных инструментов. Биоразрушаемый растворитель медленно испаряется и безопасен для оператора. Возможно его многократное использование. Печь. Изделие извлекают из матрицы, когда оно нагревается до максимальной температуры, то есть наступает пик экзотерма. Температуру изделия можно измерить с помощью градусника с инфракрасным датчиком. После извлечения из матрицы, изделие необходимо поместить на поддерживающей поверхности в печь для постотверждения. Такой поверхностью может служить, например, лист фанеры. Это существенный шаг к улучшению качества, так как при наличии достаточного нагрева твердость изделия по Барколю возрастет, по крайней мере, на 10 пунктов. Установите температуру в печи на 90°C и оставить изделие в печи на 60 минут. Перед тем, как поместить изделие в печь, ее необходимо нагреть минимум до 60°C. Помните, что намного лучше проводить постотверждение быстро при высокой температуре, чем более длительное время при пониженной температуре. Не проводите постотверждение всю ночь или когда изделие полностью охладилось: образование межмолекулярных связей уже прекратится и единственное, что будет достигнуто – это высвобождение нереактивного стирола. Например, печь, показанная на рисунке, имеет 7 уровней, куда Вы можете помещать для прогревания Ваши изделия. Двери открываются вертикально таким образом, что можно открыть верхнюю или нижнюю половину печи и сэкономить место и энергию. Эти двери также могут быть установлены на задней стороне печи для создания цикла операций на Вашем предприятии. Нагревание, конечно же, электрическое, потому что источник открытого огня не может находиться там, где есть испарения стирола. Устройство циркуляции воздуха обеспечивает перемешивание горячего воздуха и отсутствие разницы температур внутри печи. 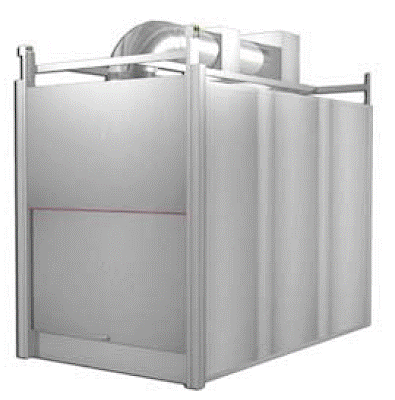
|