Различные методы сшивания полиэтилена первоначально разрабатывались с целью повышения рабочей температуры изделий из полимеров. Однако, процессы сшивания позволяют улучшить и другие характеристики полимеров, такие как: - уменьшение деформации под нагрузкой дает улучшенные характеристики на разрыв/излом при механическом напряжении в пленках и кабелях; - увеличение химической стойкости (в т. ч. к воздействию растворителей); - увеличенное абразивное сопротивление в кабельных оболочках и трубах; - эффект памяти для усадочных трубных обвязок, пленок и упаковочных пленок; - улучшенные характеристики динамической нагрузки для прессованных изделий и вспененного материала; - повышенная стойкость к старению; - повышенный модуль упругости; - повышенная ударопрочность при низких температурах; - пониженное каплеобразование (при горении). Известно три основных промышленных способов сшивки полиэтилена, в зависимости от которых сшитый полиэтилен индексируется соответствующей литерой. Это пероксидный, силановый и радиационный процессы сшивания. В европейских стандартах приняты обозначения соответственно: PEX-A, PEX-B, PEX-C. 1. Технология пероксидной сшивки.
Представляет собой свободно-радикальный процесс, приводящий к образованию углерод-углеродных связей между полимерными цепочками (см. Рисунок 1). Для получения сшитого полимера по способу А полиэтилен перед экструдированием расплавляется вместе с антиокислителями и пероксидами. С повышением температуры пероксиды распадаются, образуя радикалы (молекулы со свободной связью). Радикалы пероксидов отрывают у звеньев полиэтилена по одному атому водорода, что приводит к появлению свободной связи у атома углерода. В соседних макромолекулах атомы углерода объединяются. Количество межмолекулярных связей составляет 2-3 на 1000 атомов углерода. Образуется трехмерная сетка, которая исключает возможность образования кристаллитов при охлаждении полимера. Процесс требует жесткого контроля за температурным режимом в процессе экструзии, и когда происходит предварительная сшивка, и в ходе дальнейшего нагревания трубы для завершения образования связей. Рис.1. Структура полиэтилена, сшитого по пероксидной или радиационной технологии 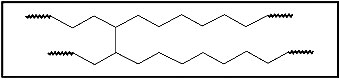
Разложение пероксидов происходит после экструзии с помощью протяженных линий непрерывной вулканизации, соляной бани или азотной системы. Пероксидно-сшитые изделия требуют продолжительного замедленного цикла термообработки (часто при повышенном давлении) для завершения процесса вулканизации. Пероксидная технология применяется для производства низко- и средневольтных кабелей, а также для производства труб. 2. Технология радиационной сшивки.
При облучении полимеров электронами, бета- или гамма-лучами образуются свободные радикалы, что приводит к появлению структур, схожих с полученными в результате пероксидной сшивки (см. Рисунок 1). Изделия облучаются после процесса экструзии, для этого часто приходится использовать отдельные производства. Процесс достаточно дорогой и продолжительный. Другим недостатком данного метода можно считать неизбежную неравномерность сшивки по толщине полиэтиленового слоя. Радиационная сшивка полиэтилена применяется при производстве пленок, термоусадочных труб и кабельной изоляции. 1. Технология Силановой сшивки.
Применение силанов позволяет получить более гибкий и экономичный процесс сшивания. Технология влажной вулканизации Silquest® применяется в промышленности свыше 30 лет. Силано-сшитые полиолефины связаны Si-O-Si мостиками, (см. Рисунок 2) в отличие от C--C связей, образующихся в результате пероксидного или радиационного метода. Рис.2. Структура полиэтилена, сшитого по силановой технологии 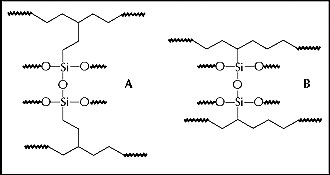 A: сшитый винилсилан (например, Sioplas®, Monosil®), B: винилсилан сополимеризации (например,, Silink®, Visico®) Sioplas, зарегистрированная торговая марка Dow Corning Corp. Monosil, зарегистрированная торговая марка Maillefer SA Silink, зарегистрированная торговая марка Dow Corp. Visico, зарегистрированная торговая марка Borealis A.S. Силановая технология состоит из двух этапов: Этап 1) внедрение силана в полимер, либо привитием винилсилана на полимерную цепочку (см. Рисунок 3), либо сополимеризацией винилсилана с этиленом в реакторе полимеризации. Этап 2) сшивка в присутствии воды (см. Рисунок 4), обычно ускоряемая оловянным или другими подходящими катализаторами. Рис.3. Прививка винилсиланов на полиэтилен
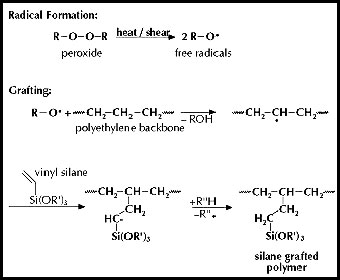
Рис.4. Сшивка Силано-привитого полиэтилена в присутствии влаги 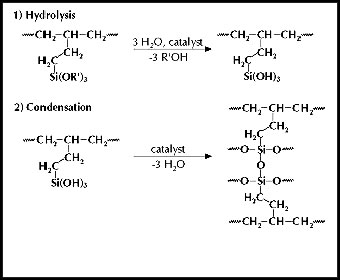
Силановое сшивание (СС) расширяет рамки производственного процесса, поскольку отпадает необходимость поддерживать температуру ниже температуры разложения перекиси. При использовании силана экструдат может быть быстро охлажден и подготовлен для чистовой обработки. Скорость полимеризации определяется скоростью диффузии влаги, поэтому для ускорения реакции часто применяется горячая водяная баня, паровая сауна или автоклав низкого давления. Силановая технология сшивания обладает следующми преимуществами, по сравнению с пероксидным и радиационным методами: • снижение капитальных вложений • снижение эксплуатационных затрат (стоимости энергии и труда) • повышение производительности • широкий спектр рецептур и применений • возможность производства изделий различной толщины • возможность производства изделий сложных форм • повышение процента наполнения пластиков • возможность применения со всеми типами полиэтиленов и сополимеров. Данная технология применяется для производства кабелей низкого/среднего напряжения (до 35 КВ), полимерных труб для подогрева полов и питьевой воды. Не так давно силановое сшивание стали использовать при производстве листовых, пленочных и вспененных материалов. Готовые химические комплексы были разработаны для оптимизации различных процессов и типов конечных продуктов. В настоящее время существует несколько промышленных, хорошо отработанных методов нанесения силанов на сшиваемые полиолефины: - Двухстадийный процесс, оригинально разработанный как Sioplas® в 1972 году Midland Silicones (Dow Corning) - Одностадийный процесс Monosil® (1978, Maillefer SA и BICC Ltd.) - Технология сополимеризации (1986, Mitsubishi) - XL-PEarl® (1992, Union Carbide, в настоящее время GE Advanced Materials. Описания этих методов приведены ниже. 2-Х СТАДИЙНЫЙ ПРОЦЕСС Sioplas® При использовании этого метода силановая смесь (содержащая какой-либо пероксид, но без катализатора конденсации) расплавляется вместе с полиэтиленом. Как правило, для этого используется оборудование смешения, например, двухвинтовые экструдеры, Ko-Kneader (Buss) и специальные одновинтовые экструдеры. Для разложения пероксида температура должна быть достаточно высокой (при помощи пероксида образуется место для привития силана к полиэтиленовой цепочке), а время достаточно продолжительным для завершения процесса привитой сополимеризации. При этом добавляются или привносятся с тем или другим ингредиентом некоторые совместимые добавки (например, антиоксиданты, наполнители и армирующие агенты). Этот материал обычно гранулируется, высушивается и хранится в сухом прохладном месте сроком до шести месяцев в мешках с внутренней прокладкой из алюминиевой фольги. Также готовится маточная смесь катализатора, она состоит из полиэтилена и катализатора конденсации, который обычно представляет собой производное олова. В большинстве случаев, первая стадия разделена по времени и месту со второй. На второй стадии маточная смесь привитого полимера и катализатора соединяются непосредственно перед подачей в экструдер. После соединения срок хранения полученной смеси очень краток, особенно если она подвергается воздействию влаги. Примечание: указанные материалы не следует перевозить и хранить вместе без надлежащей упаковки и физического разделения. Полученное изделие обычно охлаждается в ванне, подвергаясь необходимому для полимеризации воздействию влаги. Скорость полимеризации определяется скоростью диффузии влаги, поэтому для ускорения реакции часто применяется горячая водяная баня, паровая сауна или автоклав низкого давления. Оборудование, необходимое для производства полиэтилена, сшитого силаном, предлагается такими компаниями, как Werner & Pfleider (Германия) и BUSS (Швейцария). Двухстадийный процесс 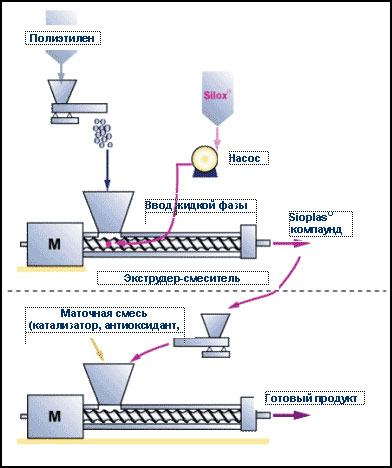
Метод Sioplas® применяется, прежде всего, для оценки возможности применения силанового сшивания для нового продукта. Он предоставляет производителям привитых полимеров максимальную гибкость в производстве подходящих материалов малыми партиями. Имеется возможность проведения испытаний различных материалов при незначительных или нулевых капиталовложениях. Большинство новых продуктов для производства пленок, кабелей и труб было получено именно этим методом. 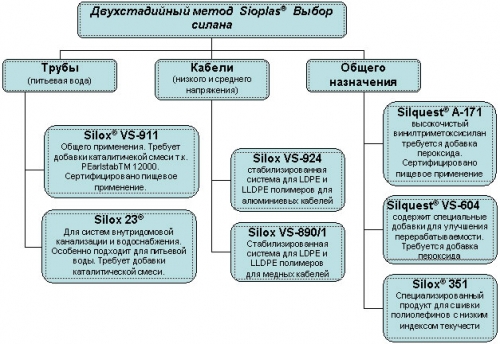
Таблица1. Продукты для двухстадийного процесса Sioplas® Марка | Тип полимера | Дозировка % | перок- сид | Анти- оксидант | Др. добавки*** | Свойства и применение | Трубы | Silox® VS-911 | HDPE1 MDPE1 | 1.2 - 2.2 | Х | - | - | Общего применения. Требует добавки каталитической смеси, напр.PEarlstabTM 12000, содержащей антиоксиданты и деактиваторы металла для применения с латунными фитингами. Сертифициро- вано пищевое применение. | Silox® 23 | HDPE1 MDPE1 | 1.1 - 2.2 | Х | - | - | Для систем внутридомовой канализации и водоснабжения. Особенно подходит для линий питьевой воды из-за низкого запаха. Требует добавки каталитической смеси (PEarlstab 12000). | Кабели и провода | Silox VS-924* | LDPE3 LLDPE2 | 1.2 - 2.2 | Х | неокра- шивающий | - | Для производства средне/низковольтных кабелей с алюминиевым сердечником (экраном). Продукты проходят тест на старение 10 дней @ 150°C. | Silox VS-890/1* | LDPE4 LLDPE2 | 1.6 - 2.0 | Х | неокра- шивающий | ДМ** | Для производства средне/низковольтных медных кабелей. Продукты проходят тест на старение 7 дней @ 135°C. | Другие отрасли и продукты специального назначения | Silquest ® VS-604 | HDPE1 MDPE1 LLDPE2 | 1.1 - 2.1 | - | - | УП** | Модифицирован добавкой, улучшающей перерабатываемость. Требует использо- вания пероксида. Сертифицировано пищевое применение. | Silquest A-171® | Все типы PE | 0.8 - 1.8 | - | - | - | Высокочистый винилтриметоксисилан, полученный по патентованному прямому процессу TMS. Сертифицировано пищевое применение. | Silox 351® * | EVA ULDPE | 1.0 - 2.0 | Х | Х | - | Специализированный продукт для сшивки полиолефинов с низким индексом текучести расплава. |
*Стабилизированные марки Silox®, для использования с нестабилизированными полимерами. ** ДМ - деактиватор металла; УП - улучшенная перерабатываемость. 1 MDPE/HDPE (0.945-0.960 г/см3) ИТР (190°С/2,16 кг.) 0,1 - 8 г/10 мин. 2 LLDPE (0.915-0.925 г/см3) ИТР (190°С/2,16 кг.) 2 - 6 г/10 мин. 3 LDPE (0.915-0.925 г/см3) ИТР (190°С/2,16 кг.) 0,2 - 2,3 г/10 мин.4 LDPE (0.915-0.925 г/см3) ИТР (190°С/2,16 кг.) 0,6 - 2,3 г/10 мин. ОДНОСТАДИЙНЫЙ ПРОЦЕСС Monosil®
При использовании этого метода полиэтилен, жидкий компонент Silcat® (включающий пероксид и оловянный катализатор) и другие совместимые добавки или наполнители добавляются в течение одного непрерывного экструзионного этапа. В этом процессе происходит смешивание сырья, достигается прививка сополимера и непрерывно формуется изделие, такое, например, как провода и кабели или трубы. Схема такого процесса предлагается на рисунке 6. Как и при использовании двухэтапного процесса, изготовленное изделие подвергается воздействию влаги. Технически более сложная система экструзии включает в себя удлиненный шнек (L/D=30 или более) и систему впрыска жидкого силанового компонента. Первоначально все оборудование для процесса данного типа носило название Моносил (Monosil), оно производилось только компанией Maillefer, сейчас оно носит название Nokia-Maillefer. Одностадийный процесс 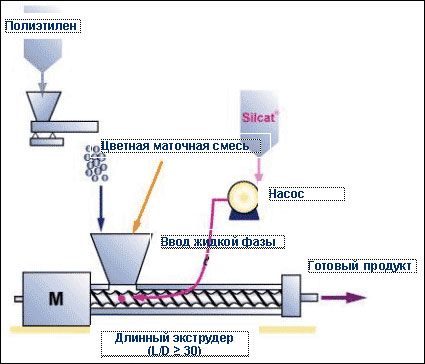
Выбор силана Марка | Тип поли- мера | Дози- ровка % | перо- ксид | Анти- окси- дант | Др. добав- ки*** | Свойства и применение | Общего назначения для стабилизированных полимеров | Silcat RHP | LDPE3 LLDPE2 MDPE1 | 0.8 - 1.8 | Х | - | - | Наиболее универсальная система , обладает пониженной склонностью к подвулканизации. Содержит слабопахнущий пероксид. | Silcat RHE | LLDPE2 MDPE1 HDPE1 | 0.8 - 1.8 | Х | - | - | Обладает повышенной эффективностью прививки, пониженным временем полимеризации, пониженной склонностью к подвулканизации, по сравнению с силаном Silcat RHP. Содержит пероксид с ослабленным запахом. | Silcat RHS | LLDPE2 LDPE3 | 0.8 - 1.8 | Х | - | - | Обладает высокой стабильностью при хранении в жарких условиях, сохраняя реакционноспособность силана Silcat RHP. | Silcat®17 | Все типы PE | 0.8 - 1.8 | - | - | - | Продукт общего назначения. Пероксиды и антиокислители должны добавляться в зависимости от используемого сырья. | Трубы | Silcat VS-758/0 | HDPE1 MDPE1 | 1.5 - 2.1 | Х | - | - | Для изготовления труб (PEX-b). Для всех ингредиентов сертифицировано пищевое применение. | Silox® 23 | HDPE1 MDPE1 | 1.5 - 2.1 | Х | - | - | Для систем внутридомовой канализации и водоснабжения. Особенно подходит для линий питьевой воды из-за низкого запаха. Требует добавки каталитической смеси (PEarlstab 12000), содержащей антиоксиданты и деактиватор металла. | Кабели и провода | Silcat VS-963* | LDPE2 LLDPE3 | 1.5 - 2.0 | Х | неокра- шивающий | ДМ | Для средне/низковольтных медных и алюминиевых кабелей. Продукты проходят тест на старение 7 дней @ 135°C на меди или 7 дней @ 150°C на алюминиевом проводнике. | Silcat VS-735/1* | LDPE5 LLDPE2 | 1.6 - 2.2 | Х | неокра- шивающий | ДМ | Для низковольтных медных кабелей. Продукты проходят тест на старение 10 дней @ 135°C на меди или 10 дней @ 150°C на алюминиевом проводнике. | Silcat VS-966* | LDPE5 LLDPE2 | 1.6 - 2.2 | Х | неокра- шивающий | ДМ | Высокостабилизироанная силановая система для медных кабелей низкого напряжения. Продукты проходят тест на старение 7 дней @ 150°C (т.e.соответсвует спецификации G7). | Специализированные продукты | Silcat VS- 870M* | HFFR MDPE1 LLDPE2 | 1 - 2 | Х | неокра- шивающий | ДМ | Предназначен для производства не поддерживающих горение и полупроводниковых смесей, содержащих технический углерод. | PEarlstab 11000 | MDPE1 LLDPE2 LDPE3 | 3 - 5 | - | Х | ДМ УП | Стабилизатор - маточная смесь для средне/ низковольтных медных кабелей. Продукты проходят тест на старение 7 дней @ 135°C при дозировке 3% и 7 дней @ 150°C при дозировке 5%. Для применения с Silcat продуктами общего назначения. | PEarlstab 12000 | MDPE1 HDPE1 | 5 | - | Х | ДМ УП | Катализатор - маточная смесь для питьевой воды и внутридомовых систем снабжения. Для применения с Silox 23. |
*Стабилизированные марки Silсat® или PEarlstab®, для использования с нестабилизированными полимерами. ** ДМ - деактиватор металла; УП - улучшенная перерабатываемость. 1 MDPE/HDPE (0.945-0.960 г/см3) ИТР (190?С/2,16 кг.) 0,1 - 8 г/10 мин. 2 LLDPE (0.915-0.925 г/см3) ИТР (190?С/2,16 кг.) 2 - 6 г/10 мин. 3 LDPE (0.915-0.925 г/см3) ИТР (190?С/2,16 кг.) 0,2 - 2,3 г/10 мин. 4 LDPE (0.915-0.925 г/см3) ИТР (190?С/2,16 кг.) 0,6 - 2,3 г/10 мин. 5 ULDPE (0.863-0.900 г/см3), LDPE (0.915-0.925 г/см3), ИТР (190?С/2,16 кг.) 0,2 - 1 г/10 мин. СОПОЛИМЕРИЗАЦИЯ
Ряд компаний, возглавляемых Mitsubishi (Япония), Union Carbide (США) и Borealis (Швеция) предлагают продукты сополимеризации этилена и винилсилана, синтезируемые под высоким давлением. Получаемые продукты вулканизируются в присутствии катализатора и воды, как и компаунды Sioplas®. Таким образом, для использования данных марок требуется наличие каталитической (и, возможно, содержащей стабилизаторы) маточной смеси. Продукты сополимеризации более устойчивы при хранении и вулканизируются более равномерно, но этот процесс может быть продолжительнее. Существует ограниченный спектр продуктов сополимеризации, определяемый технологией производства полимеров - доступны только материалы, получаемые методом высокого давления. Низкие капиталовложения в экструзионное оборудование выгодно для конечного производителя, при этом расходы на сырье, как правило, находятся между стоимостью сырья для одностадийного и двухстадийного процессов. XL-PEarl® Маточные смеси: Сухая Силановая система XL-PEarl сухие силановые смеси представляют собой пористые полимерные носители, пропитанные силаном и обеспечивают возможность одностадийного процесса сшивания. Производители труб, пленок и листов могут смешивать XL-PEarl с полимерными гранулами, используя подходящие гравиметрические дозаторы. Желательно использовать отдельные системы дозирования для цветной маточной смеси и базового полимера. Готовые изделия затем могут быть получены в процессе экструзии, литья или прессования и пройти стадию влажной полимеризации. Особенности и преимущества метода: - Позволяет загружать силановый компонент в экструдер в твердой форме; - Технология основана на применении оптимальных полимерных носителей в форме порошка или гранул; - XL-Pearl® может добавляться в виде готовой маточной смеси или смешиваться на производстве; - Существующие стандартные экструдеры могут применяться для производства XLPE (подходят экструдеры 24 L/D); - Простая и быстрая пуско-наладка; - Уменьшение отходов; - Гибкость в использовании (твердые компоненты проще и безопаснее хранить); - Пониженное потребление силана; - Сшитые и термопластичные полимеры могут производиться на одной линии; - Возможна экструзия XLPE изделий большего диаметра и толщины благодаря лучшей дисперсии; - XL-Pearl® Позволяет использовать базовые полимеры местного производства; - XL-Pearl® Маточная смесь может быть приспособлена для различных конечных продуктов при изменении скорости полимеризации. Имеется полный спектр XL-Pearl® силанов, предназначенных для приготовления сухих маточных смесей XL-Pearl®. GE Silicones выбрал ряд компаний, которым предоставлены лицензии на производство сухих силановых смесей XL-Pearl® . Обладатели лицензий производят гранулированные полимеры с нанесенным силаном для конечных пользователей, использовавших силановые смеси Silcat® и Silox®. Лицензия предоставляется на право производства и маркетинга маточных смесей, получаемых только с использованием силанов XL-Pearl® XL-PEarl Сухой силановый процесс 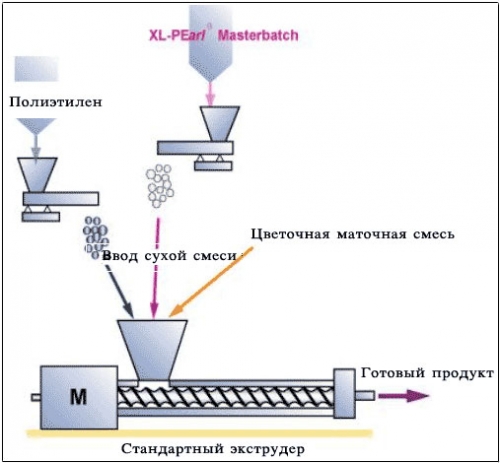
XL-Pearl® сухие маточные смеси предлагаются на EVA, LDPE, HDPE или PP пористых полимерных носителях в зависимости от области применения и марки базовой силановой смеси. Использованы материалы: "Силановое сшивание полиолефинов" L. Panzer и Dr. P. Kraxner GE Silicones-OSi Specialties |