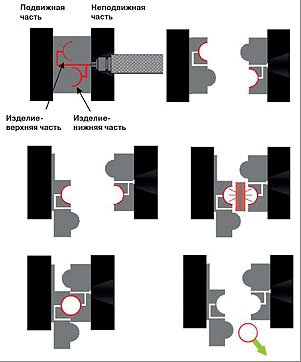
Техническое решение, на которое подана заявка на патент, является многообещающим с точки зрения экономии используемых ресурсов, прежде всего, для поставщиков автомобильных комплектующих. «Исключается необходимость в дополнительном сварочном устройстве. Не приходится больше извлекать и затем снова укладывать заготовку, так как готовое изделие получают непосредственно в литьевой форме», - подчеркивает Франц Фюредер (Franz Fuereder), руководитель автомобильного подразделения компании ENGEL. Формование обеих частей изделия осуществляется одновременно в одной и той же литьевой форме. По окончании стадии охлаждения литьевая форма открывается, причем одна часть изделия остается в левой полуформе, вторая – в правой. После этого, левая полуформа перемещается таким образом, что обе части изделия позиционируются друг относительно друга в подходящем для процесса сварки положении. В зону между гнездами литьевой формы вводится нагревательный элемент, с помощью которого осуществляется нагревание краев обеих частей изделия. При последующем закрывании литьевой формы обе части изделия свариваются, а после повторного открывания лить-евой формы из нее извлекается готовое изделие. Повышение качества и функциональной надежности Повышение качества и функциональной надежности позволяет наряду с существенной экономией ресурсов повысить качество и функциональную надежность изготавливаемых изделий. Поскольку обе части изделия перед сваркой остаются в литьевой форме, исключается опасность их деформирования и существенно умень- шаются затраты времени на вывод продукции на рынок. Образуется чистый и тонкий сварной шов высокой прочности, способный выдерживать более высокое усилие продавливания, чем традиционные сварные швы. Новая технология может быть использована при переработке всех видов термопластов. Особенно широкие потенциальные возможности для ее применения разработчики видят в области производства контактирующих с движущимися веществами деталей для моторного отсека автомобиля из армированных стеклянными волокнами полиамидов. До сих пор подобные детали в местах сварных швов имели заметные наплывы, которые обуслaвливали повышенный износ и связанное с этим уменьшение срока службы других функциональных элементов, например, толкателей клапанов. Применение технологии ENGEL joinmelt исключает образование подобных наплывов, что обеспечивает экономию материала и снижение массы изделий. Еще одно преимущество новой технологии проявляется уже на стадии разработки новых изделий. Эта технология не требует выдерживать строго определенное направление сварки, а следовательно изделиям можно придавать любую конфигурацию. Командная работа признанных специалистов Компания ENGEL разработала новую технологию в тесном сотрудничестве с двумя партнерскими фирмами. При этом машиностроительная компания не только взяла на себя ответственность за создание необходимого оборудования, но и разработала программное обеспечение для управления протеканием совмещенных технологических процессов. Компания Hummel-Formen подала заявку на патент на способ сварки нагретым газом в литьевой форме и в качестве вклада в совместную разработку предоставила собственные ноу-хау в области литьевых форм. Эта фирма, насчитывающая 250 сотрудников и располагающая двумя заводами, специализируется на изготовлении литьевых и пресс-форм массой до 100 т, предназначенных для переработки полимерных материалов. Сфера деятельности фирмы простирается от разработки новых видов продукции до апробации в условиях серийного производства (www.hummel-formen.de). Компания KVT Bielefeld при разработке технологии ENGEL joinmelt отвечала за сварочное оборудование. Она обладает патентом на способ образования высокопрочных сварных соединений без выделения частиц методом сварки нагретым газом с использованием инертного газа. Компания специализируется в области разработки и изготовления сварочных машин для сварки изделий из полимерных материалов, используемых в качестве компонентов продукции разных отраслей промышленности, включая автомобили, бытовую, телекоммуникационную и медицинскую технику (www.kvt-bielefeld.de). http://www.extrusion-info.com/ |