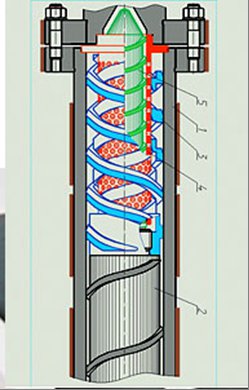
Смесевые композиции термопластов с каучуками по свойствам приближаются к термоэластопластам, новому классу полимерных соединений, получаемых методом синтеза эластомерных блок-сополимеров. Объем выпуска и номенклатура термоэластопластов постоянно расширяется, однако технологии синтеза, разработка и промышленное освоение которых связано с длительными сроками и крупными капиталовложениями, не в состоянии оперативно удовлетворять потребности рынка в новых полимерных материалах. Смесевые технологии, в отличие от технологии синтеза, позволяют организовать производство новых полимерных веществ из существующих полимеров с помощью низкозатратных процессов, не требуют сложного аппаратурного оформления и способны в короткое время отреагировать на запросы рынка. Вместе с тем, реализация возможностей и преимуществ смесевых технологий существенно ограничивается из-за отсутствия эффективного и одновременно простого по конструкции универсального смесительного оборудования непрерывного действия, осуществляющего смешение в жидкой фазе (расплаве), с возможностью оперативного управления процессом смешения. Такое оборудование должно учитывать специфические технологические свойства компонентов смеси, а по техническим характеристикам (производительности, энергозатратам) и стоимости отвечать производственным требованиям и финансовым возможностям большинства предприятий, занимающихся переработкой пластмасс. С этой целью чаще всего используют одно- и двухшнековые экструдеры, шнеки которых снабжены смесительными и сдвиговыми элементами, способными создавать смесительный эффект в большинстве случаев достаточный для осуществления одновременно с переработкой полимера процессов окрашивания или распределения в нем модифицирующих добавок. Вместе с тем, интенсивность смешения этих машин не в состоянии обеспечить высокие требования к качеству композиций по размеру частиц дисперсной фазы и их распределению при создании концентратов добавок или переработке сложных полимерных смесей, включающих термодинамически несовместимые компоненты, какими преимущественно являются термопласты и каучуки. Исключение могут составлять двухшнековые экструдеры с попутным вращением шнеков, включающих наборы из кулачковых смесительных элементов, по типу экструдеров ZSK фирмы «Werner und Pfleiderer». Однако, сложность конструкции и высокая стоимость этих экструдеров существенно ограничивают их применение. Комплект экструзионного оборудования, обладающий большими технологическими возможностями, обеспечивающими, в том числе, получение высококачественных концентратов и полимерных композиций термопластов с каучуками, разработан и изготовлен научно-производственной фирмой «ЭТО» (г. Киев, Украина). В комплект оборудования, кроме экструдера-смесителя, входят механизмы и устройства для дозирования и подачи компонентов смеси в винтовой канал шнека смесителя, а именно: экструдер для подготовки расплава термопластичного полимера, дозатор объемный каучука и дозатор весовой сыпучих компонентов, а также устройства для гранулирования расплава композиции – формующая головка, ванна охлаждения стренг и фрезерный гранулятор. экструдера, снабженного смесительным устройством, конструкция которого позволяет реализовать новую технологию получения смесевых полимерных композиций. Рабочие органы экструдера (корпус и шнек) по технологическому принципу разделены на три последовательно расположенных зоны – зону загрузки, зону смешения и зону выдавливания. Смесительное устройство, установленное в зоне смешения, представляет собой многозаходный ленточный шнек, состоящий из соосно расположенных наружных и внутренних витков противоположного направления, жестко соединенных между собой, и взаимодействующий с ним неподвижный сердечник, выполненный в виде полого цилиндра с отверстиями на боковой поверхности (см. схему). Ленточный шнек закреплен на основном шнеке и вращается вместе с ним, а его внутренние витки охватывают неподвижный цилиндр с минимальным зазором, обеспечивающим возможность его вращения. Полый цилиндр с помощью фланца установлен в корпусе экструдера таким образом, что выход расплава из рабочего канала ленточного шнека, образованного внутренней поверхностью корпуса экструдера и наружной поверхностью полого цилиндра, полностью перекрывается фланцем. Благодаря этому, рабочий канал ленточного шнека сообщается с винтовым каналом шнека в зоне выдавливания только через отверстия в стенке цилиндра и внутренний кольцевой канал, образованный внутренней поверхностью перфорированного цилиндра и сердечником шнека. Шнек экструдера-смесителя вращается от привода с регулируемой скоростью вращения. Работает смеситель следующим образом. Расплав базового полимера от экструдерплавителя через обогреваемый патрубок поступает в зону загрузки смесителя. Сюда же с помощью соответствующих дозирующих устройств подаются другие компоненты композиции, в том числе каучук. Перемещаясь по винтовому каналу шнека, материал поступает в зону смешения, образованную ленточным шнеком и полым перфорированным цилиндром. Наружный и внутренний витки ленточного шнека, взаимодействуя с внутренней поверхностью корпуса экструдера и наружной поверхностью цилиндра, создают в кольцевой рабочей полости ленточного шнека потоки расплава противоположного направления, на которые накладывается прямой поток, формируемый загрузочной частью шнека. Встречные потоки расплава пересекаясь создают эффект активного перемешивания полимерной смеси в относительно большом объеме и обеспечивают предварительное распределение компонентов и однородность композиции на уровне агломратов и крупных частиц. Одновременно перерабатываемый материал, не имея прямого выхода в зону выдавливания, перетекает через отверстия на боковой поверхности цилиндра во внутреннюю его полость, благодаря чему весь расход расплава проходит переработку в малом зазоре между гребнем внутренних витков ленточного шнека и цилиндром (не более 0,1 мм). При относительно небольших скоростях течения расплава через отверстия в цилиндре, витки ленточного шнека, перемещаясь относительно его поверхности, многократно подвергают слой расплава, примыкающий в данный момент к наружной поверхности цилиндра, интенсивному сдвигу. Аналогичный процесс происходит на внутренней поверхности перфорированного цилиндра, взаимодействующей с витками зоны выдавливания шнека экструдера. Регулируемая частота вращения шнека позволяет при постоянном расходе управлять интенсивностью процессов смешения, обеспечивая, таким образом, требуемое качество смеси. После смесительного устройства расплав с помощью выгрузной части шнека транспортируется к выходу из смесителя и продавливается через гранулирующую головку. Формируемые в головке жгуты охлаждаются водой и режутся на гранулы в гранулирующем устройстве. Отличительной особенностью нового смесительного устройства в сравнении с известными конструкциями смесительных и сдвиговых элементов, используемых в одно- и двухшнековых экструдерах, является возможность переработки за короткий промежуток времени всего, без исключения, расхода перерабатываемого материала в малом зазоре между витками вращающегося шнека и неподвижной поверхностью перфорированного цилиндра, через отверстия которого этот расход осуществляется. Возникающие в тонких слоях расплава, примыкающих к наружной и внутренней поверхности цилиндра, высокие градиенты скоростей и напряжений сдвига создают смесительный эффект, благодаря которому достигаются минимальные размеры и равномерность распределения частиц дисперсной фазы, обеспечивающие высокие механические и реологические свойства смесей. При этом, интенсивный сдвиг перерабатываемого материала в малом зазоре на поверхности перфорированного цилиндра не создает на этом участке значительного сопротивления течению расплава, что расширяет диапазон технологических режимов смешения без существенного перегрева расплава полимера и снижения производительности экструдера-смесителя. Особенности конструкции смесительного устройства позволяют реализовать в экструдере-смесителе новую технологию смешения, обеспечивающую существенное повышение качества композиций термопластов с каучуками. Улучшение свойств этих материалов, получивших название «термопластичных вулканизатов», достигается при переработке смеси в условиях интенсивного сдвига благодаря уменьшению размеров частиц и повышению степени вулканизации каучуковой фазы, без ухудшения текучести и термопластичности композиции [1]. Эффективность одношнекового экструдера-смесителя подтверждена опытом многолетней эксплуатации в производстве специальных полимерных композиций, содержащих каучук, используемых для изготовления изделий, работающих в условиях низких температур. Обеспечивая высокое качество смешения, экструдерсмеситель предлагаемой конструкции легко встраивается в существующие производства и по габаритам, металлоемкости и цене имеет существенные преимущества в сравнении с существующими образцами смесителей для пластмасс. Возможны варианты исполнения экструдера-смесителя, основанные на вышеописанном принципе смешения, по конструкции шнека, расположению и геометрии основных деталей смесительного устройства, рассчитанные на изготовление термопластичных полимерных композиций с заданными свойствами из различных полимерных и не полимерных материалов с производительностью от 50 до 1000 кг/ч. C текущей ситуацией и прогнозом развития российского рынка ДПКТ можно познакомиться в отчете Академии Конъюнктуры Промышленных Рынков «Рынок древесно-полимерных композиционных материалов в России». Литература Сабет Абду-Сабет, Судин Датта «Термопластичные вулканизаты». Сб. статей «Полимерные смеси» под ред. Д.Р.Пола и К.Б.Бакнелла, том II, стр.539, изд-во «Научные основы и технологии», Санкт-Петербург, 2009г. ООО НПФ «ЭТО» к.т.н. Е.Бармашин http://www.extrusion-info.com |