Рекорд скорости при производстве алюминиевых комбинированных труб: Большой круг заинтересованных покупателей убедился в возможности уникальной скорости - свыше 50 м/мин - при производстве алюминиевых комбинированных труб. Компания "Battenfeld Extrusionstechnik GmbH" совместно с партнером "Templet Deutschland GmbH" провели эту презентацию во время дня открытых дверей, состоявшегося в г. Зелигенштадт (Германия) 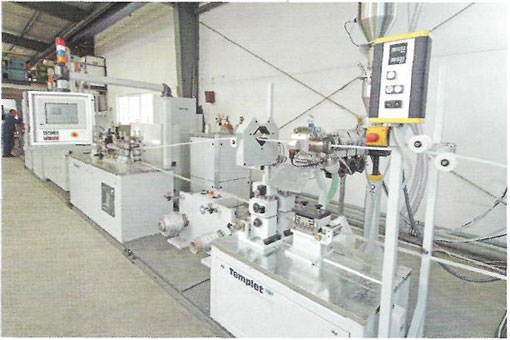
Комплексная линия для производства комбинированных труб из ПЭ и алюминия, представленная компаниями "Templet Deutschland GmbH" и "Battenfeld Extrusionstechnik bH" Алюминиевые комбинированные трубы пользуются растущим спросом и благодаря своим значительным преимуществам все больше и больше вытесняют обычные металлические трубы. Наряду с высокой коррозионной устойчивостью, абсолютной газонепроницаемостью и электрической непроводимостью, комбинированные трубы убеждают быстротой монтажа, свободной и простой формуемостью. Сегодня они используются преимущественно в водопроводах горячей и холодной воды, а также для отопительных систем. Фирма "Templet", специализирующаяся на изготовлении оборудования по металлическим облицовкам в сантехнике и "Battenfeld Extrusionstechnik" продемонстрировали комплексную линию длиной 83 м для изготовления 5-слойных алюминиевых комбинированных труб с полиэтиленовым покрытием. В таких трубах внутренний алюминиевый слой покрыт двумя слоями для улучшения адгезии и наружными слоями из ПЭ-ХЬ (сшитого полиэтилена). Для их изготовления необходимо обеспечить несколько оптимально согласованных технологических операций: сначала на классической линии для экструзии труб изготавливается внутренняя труба, на которую во время следующей операции наносится адгезионный слой, после чего производится облицовка алюминиевым слоем. После сварки алюминиевого слоя теперь уже 3-х-слойная труба подаётся на поперечную экструдерную головку, где наносится второй слой для повышения адгезии и наружный слой из ПЭ-Хb. Во время демонстрации линии, рассчитанной на производство труб диаметром от 14 по 40 мм при гарантированной скорости 35 м/мин, изготавливалась труба диаметром 16 мм, с толщиной стенки 2,1 мм. При этом была достигнута рекордная скорость, составившая 52 м/мин Новая система автоматизации улучшает комфорт обслуживания:
«BMCtouch» - самое молодое звено в серии систем управления «Battenfeld Machine Control «ВМС», обладающее уникальными функциями. После успешного тестирования начаты первые серийные поставки. 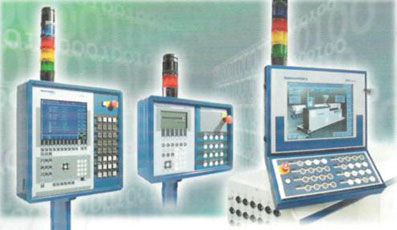
Новое «лицо» системы управления ВМС. Система «BMCtouch» не только внешне отличается от остальных моделей систем управления «BMCplus» и «BMCsmart» - технические усовершенствования предоставляют дополнительные возможности. В новой системе управления машинами сохранены зарекомендовавшие себя на рынке стандарты. Так, датчики и исполнительные органы объединены в сеть с помощью стандартизированной шины системы CAN, а процесс визуализирован с Windows. Название «BMCtouch» говорит само за себя: управление осуществляется интуитивно с помощью сенсорного экрана. Цветной 15" -экран с высокой разрешающей способностью и очень прочной поверхностью помещён в корпусе экономных размеров. При этом сохранены большие клавиши, что позволяет оператору машины пользоваться им, не снимая перчаток. 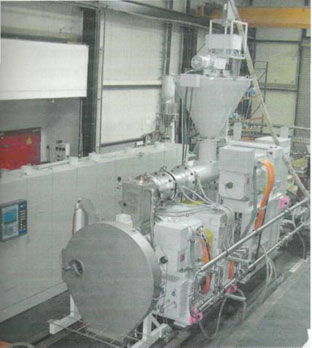
Двухступенчатый экструдер ZSE 250 / 280; использование для гранулирования Благодаря возможности изменения конфигураций, поверхность экрана легко адаптируется к требованиям заказчика: индивидуальные элементы индикации можно размещать постранично, в то время как функциональные клавиши основных функций всегда видны и постоянно находятся в распоряжении. Новинка: многоместное управление Система «BMCtouch» может выполнять также и управление всей линией. Отдельные компоненты машины легко интегрируются в систему управления, надёжно контролируются и управляются в производственном процессе. Другая принципиальная новинка этого поколения систем управления - возможность многоместного управления. Находясь в сети «BMCtouch», оператор машины может с любого экструдера наблюдать за любым другим экструдером и управлять им. Планетарный валковый экструдер оптимизирован: производительность значительно повышена
Планетарные валковые экструдеры известны своими оптималь¬ными диспергирующими и гомогенизирующими свойствами и вытекающим из этого широким спектром применения. Инженеры фирмы Battenfeld Extrusionstechnik GmbH продолжили оптимизацию машинной концепции, обеспечив еще большую гибкость при одновременном повышении производительности и снижении расходов. Увеличению спектра использования планетарного валкового экструдера способствует новая альтернативная система темперирования технологического узла. Для охлаждения цилиндра вместо масла используется вода, а нагрев осуществляется керамическим электронагревателем. Благодаря этому, в течение короткого времени можно как подавать, так и отводить больше энергии, что расширяет возможности использования и значительно увеличивает производительность. Переработана вся секция планетарного валка; создатели улучшили как геометрию отдельных планетарных шпинделей, так и сегментов цилиндра. Все использованные сегменты цилиндра в количестве до четырех теперь являются взаимозаменяемыми, благодаря чему значительно увеличивается срок службы всего узла. Планетарные шпиндели также выполнены симметричными: достаточно один раз провернуть, чтобы произвести замену. 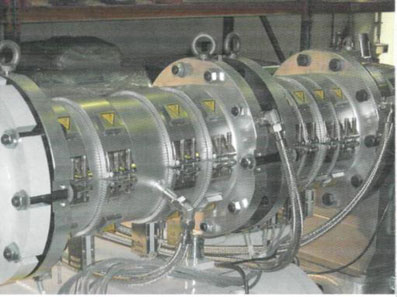
Планетарная валковая секция с электрическим нагревом и водяным охлаждением Совершенно новым является мультифункциональное кольцо, которое устанавливается между сегментами цилиндра планетарной валковой секции и может выполнять несколько функций. До сих пор не было возможности точно задавать давление и температуру в планетарной валко¬вой секции. Отныне в ней, благодаря мультифункциональному кольцу, можно устанавливать датчики давления и/или температуры. Через это кольцо в технологический узел также можно вводить специальные жидкие добавки и эффективно удалять летучие компоненты. До сих пор, например, жидкую краску дозировали в загрузочную зону планетарного валкового экструдера непосредственно вместе с полихлорвиниловой смесью, что часто приводило к склеиванию материала. Теперь жидкие добавки можно дозировать непосредственно в расплав, находящийся в планетарной валковой секции. Благодаря этому предотвращается склеивание и обеспечивается оптимальная эффективность смешивания. 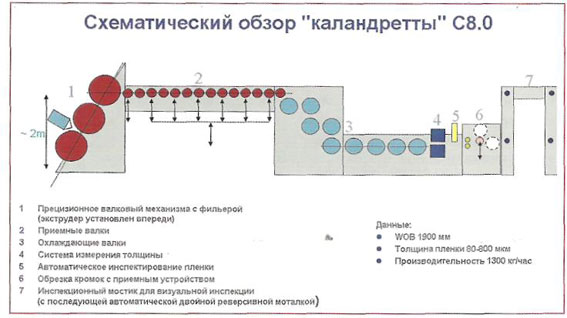
В виде опции мультифункциональное кольцо может быть оснащено устройством дегазации. Именно при одноступенчатом режиме планетарного валкового экструдера такая возможность предоставляет дополнительные преимущества в сравнении с предыдущими моделями. В планетарной валковой секции поверхность расплава быстро обновляется, благодаря непрерывному перемешиванию, что содействует эффективной дегазации. Вследствие проведенной оптимизации, новые планетарные валковые экструдеры при более высокой производительности и повышенной эффективности отличаются большими технологическими возможностями и повышенной гибкостью при меньших инвестиционных и эксплуатационных расходах. Экономичность и гибкость: изготовление полихлорвиниловой пленки при помощи "каландретты"
"Каландретта" является идеальной альтернативой каландру и специально предназначна для изготовления малых и средних партий полихлорвиниловых пленок. Результатом технической и конструктивной оптимизации явилась экономичная и гибкая машинная концепция в виде двух дополнительных типоразмеров с расширенным рабочим спектром Комплектные линии, для которых требуется оптимальное согласование отдельных машинных компонентов, являются безусловной компетенцией фирмы Battenfeld Extrusionstechnik. К комплектному агрегату с "каландреттой" относятся двухступенчатая экструдерная система, состоящая из планетарного валкового экструдера и разгрузочного узла с соплом, прецизионного валкового устройства, приемного и охлаждающего валкового устройства, системы измерения толщины, устройства обрезки кромок и резки по центру, двойной реверсивной моталки, а также системы темперирования, электрооборудование и система управления агрегатом. Сердцевиной такого агрегата является 3-валковое прецизионное устройство - "каландретта". 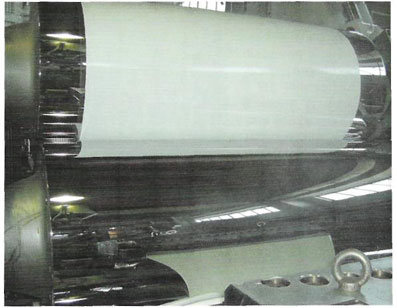
Сердечником "каландретты" является прецизионный валковый механизм. Для изготовления прозрачной или покрытой пленки из твердого или полутвердого полихлорвинила в диапазоне толщин 150-800 мкм, предназначена меньшая модель "каландретты" С 3.1 с шириной валков 1200 мм и производительностью до 600 кг/час. На модели С 8, однотипной модели большего размера, с шириной валков 1900 мм и максимальной производительностью 1300 кг/час, можно изготавливать каландрированную полихлорвиниловую пленку толщиной от 80 до 800 мкм, используемую, к примеру, для упаковок в фармацевтической промышленности. В сравнении с классическим каландром, "каландретта" отличается низкими инвестиционными расходами, меньшей стоимостью периферии, простотой обслуживания. Изменяя концепцию оборудования, Battenfeld Extrusionstechnik большое значение уделила повышению удобства обслуживания. Так, к примеру, при установке новой "каландретты" С8 отпала необходимость в яме - агрегат может быть смонтирован на одном уровне, что значительно повышает удобство доступа. Этому способствует также наклонное положение стойки под углом 60°. В соответствии с современной технологией, регулирование зазора в 3-валковом прецизионном устройстве производится гидравлически - изгиб валков и пересечение осей являются двумя функциями - благодаря этому обеспечивается правильный и постоян¬ный зазор валков и, соответственно, неизменно высокое качество продукции. Среди первых заказчиков, купивших комплектно переработанную "каландретту", крупный изготовитель полихлорвиниловых пленок для фармацевтической промышленности. Предприятие, уже в течение длительного времени использующее "каландретту", вновь приобрело модель фирмы Battenfeld Extrusionstechnik. Новая версия этой машины оправдала надежды клиентов. Battenfeld Extrusionstechnik GmbH KonigstraBe 53, D-32547 Bad Oeynhausen Тел.: +49 5731 242-0, Факс: +49 5731 27124 welcome@bex.battenfeld.com; www.bex.battenfeld.com
|