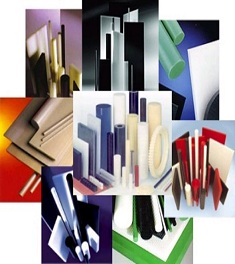
Термины рециклинг, повторно использованный, допускающий повторное использование (хотя они, в основном, применяются по отношению к утилизации для использования отходов материалов) принимают различный смысл в зависимости от контекста, в котором они употребляются. Например, имеются административные определения, основанные на критерии состава, которые позволяют называть материал повторно использованным, если он содержит как минимум 25% по весу отходов использованных изделий, тогда как остальная его доля состоит из непереработанного, первичного, материала. Подобным образом допускающий повторное использование материал был определен Федеральной комиссией по торговле США как материал, который должен допускать переработку, которая в настоящее время осуществляется и широко доступна; то есть фактический рециклинг материала должен быть устоявшейся промышленной технологией. Однако повторное использование полимерного мусора, который обычно называют «обрезки», то есть возникающего как побочный продукт литья или экструзионного процесса, не классифицируется как рециклинг, если обрезки возвращаются непосредственно в загружаемый материал. Также материалы этого сорта не классифицируются как допускающие повторное использование согласно тому, что считается хорошей практикой ведения хозяйства. К несчастью, ни одно из этих более точных определений не отвечает требованиям материаловедения по способности к восстановлению. Это касается рециклинга как основного предмета этой статьи и, следовательно, любое упоминание здесь способности к восстановлению подразумевает целостность материала, которая упрощает выделение материала из потока отходов, например, со свалки, в практическое применение. Восстановленный материал не должен обладать свойствами, присущими исходному полимеру. Свойства восстановленных смесей должны отвечать лишь требованиям для выбранного применения. Наконец, случайные и неконтролируемые смеси полимеров обычно имеют плохие механические, оптические и поверхностные свойства по сравнению с их чистыми составляющими, и их обычно описывают как несовместимые. Совместимость часто плохо определена в количественных выражениях, что, порой, приводит к разночтениям; однако здесь мы будем подразумевать под совместимостью способность двух и более полимеров быть переработанными с помощью доступной ныне технологии в единый материал, набор свойств которого считается приемлемым для нормального использования. Хотя слово несовместимость обычно оставляют для обозначения взаимонерастворимых смесей, совместимость в этом смысле может иметь место как во взаиморастворимых, так и во взаимонерастворимых смесях. Многие из термодинамических и технологических проблем, которые приходиться рассматривать при создании смеси или сплава, имеют равным образом отношение к рециклингу полимерных смесей; однако существуют дополнительные трудности, которые следует принимать во внимание при рециклинге. Если не делать различия между рециклингом по истечении срока службы (ИСС) и восстановлением или утилизацией во время производства, то наиболее важным вопросом, который определяет рециклинг термопластов и их смесей, является выносливость составляющих и морфология, необходимая для устойчивости к термической, окислительной и механо-химической деструкции во время повторяющихся операций переработки. Следует учесть дополнительное влияние долговременной деградации; в рабочей среде и загрязнение другими материалами, такими как покрытия, краски; и поглощенные жидкости; эти факторы имеют такое же отношение к способности к восстановлению однокомпонентных материалов. Смеси и сплавы Многие широкоиспользуемые термопласты являются фактически смесями или смесевыми полимерными системами значительной сложности; свыше 30% по весу от общего потребления полимеров находились, как известно, в виде сплавов или смесей. Например, смеси поликарбоната и акрилонитрил-бутадиен-стирола (ПК-АБС) составлены из трех различных полимеров. Растущие требования к улучшенным свойствам, таким как жесткость, пластичность и ударная прочность, стимулируют значительное развитие улучшенных материалов, которое может достигаться смешением или сплавлением полимеров. Это может быть выполнено созданием химического взаимодействия между составляющими и/или контролем морфологии и состава во время смешения. К сожалению, введение нескольких компонентов и компатибилизующих систем может вызвать повышенную склонность к деструкции (например, химическое взаимодействие между компонентами) и нестабильность морфологии при экспозиции многократным (и, следовательно, вредоносным) тепловым обработкам, которые могут иметь место при рециклинге. Эти нежелательные процессы являются, разумеется, дополнением к обычной термодеструкции и снижению молекулярного веса, которые следует ожидать при переработке расплавов. Стабильность модификаторов, повышающих ударную прочность Составы с модификаторами, повышающими стойкость к удару (далее «ударные модификаторы»), возможно, представляют наиболее распространенные многокомпонентные системы. Сопротивление трещинообразованию и повышенная ударная вязкость входят в число наиболее ценных атрибутов полимерных материалов. Соответственно, морфологическая и термическая стабильность каучуковых добавок является первостепенным требованием для рециклинга. Полибутадиен (ПБ) обеспечивает великолепные низкотемпературные ударные свойства, однако двойные углерод-углеродные связи особенно восприимчивы к термической и окислительной деструкции. При этом каучук деструктирует и сшивается, что снижает его эффективность как ударного модификатора и может вести к увеличению вязкости и трудностям в переработке. Стойкость термопластов АБС к многократной переработке (до пяти циклов) весьма высока благодаря относительно низким технологическим температурам (220 °С); однако известно о небольшой потере ударной прочности, которую связывают с деструкцией полибутадиена. Сплавы ПК-АБС, в которых ПК образует матрицу, требуют более высокой температуры при переработке, чем АБС, и поэтому они более подвержены термодеструкции. Было найдено, что смесь ПК-АБС, прошедшая четыре-пять циклов литья под давлением испытывает значительную потерю механических свойств, сопровождаемую увеличением вязкости расплава. Вновь сшивание и окисление каучуковой фазы были названы главными причинами наблюденных изменений. Деструкция АБС под действием окружающей среды и фотоокисления оказывает такой же эффект на ПБ. Материалы, находившиеся вне помещения до 10 лет, проявляли, по данным термического анализа, значительное увеличение Т компонента ПБ. Самые большие изменения происходили на поверхности отливок; был предложен полуколичественный метод измерения степени деструкции на основе дифференциальной сканирующей калориметрии (ДСК). Образцы, находившиеся на солнечном свете в течение 6 лет, проявили уменьшение ударной вязкости; однако измельчение и переработка расплава состаренного полимера не производились, так что трудно было оценить влияние экспозиции на солнце на возможность восста¬новления этих материалов. Если деструкция ограничивается поверхностным слоем, суммарный эффект воздействия окружающей среды и фотоокисления на объемные свойства восстановленного АБС может быть минимальным. Сочетание жесткости (в особенности под действием высокой температуры) и стойкости к растворителям, присущей сплавам полиамидов, например, ПА-66 с поли-2,6-диметил-1,4-фениленоксидом (ПФО), стимулировало масштабные промышленные разработки этих материалов. Однако термодинамическая несовместимость полиамидов и ПФО потребовала включения привитого сополимера, содержащего два полимерных скелета, необходимых для получения желаемой морфологии и достаточной адгезии между двумя полимерами. Включение этого привитого сополимера выполнялось in situ реакционной экструзией ПФО, модифицированного малеиновым ангидридом, который реагирует с концевыми группами полиамида. Введенные небольшие количества (2-10 %вес.) сополимера стирол-малеиновый ангидрид (СМА), содержащего 8 %вес. МА, также могут выполнять эту функцию. Сплав полиамида и ПФО имеет приблизительный состав 50:50 по весу; однако полиамид образует непрерывную фазу, содержащую выраженную дисперсную ПФО фазу. Сопротивление ударному воздействию и трещинообразованию было предметом подробного изучения, и включение эластомерного модификатора, как правило, в форме блок-сополимера полистирола (ПС) и каучукоподобного углеводородного полимера (например, полибутадиена (ПБ)) было признано необходимым. Конечный сплав - это сложное соединение четырех различных полимерных скелетов и вспомогательных стабилизаторов. |