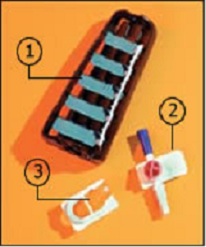
Маркировка в процессе формования, декорирование пленкой и пленочная ламинирование становятся хорошо зарекомендовавшими себя методами. Что же станет следующим шагом на пути к реализации общей тенденции исключения вторичных технологических этапов за счет реализации всех необходимых операций при формовании? Следующей задачей на повестке дня является сборка в процессе формования. 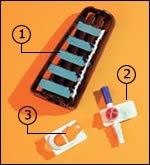 | 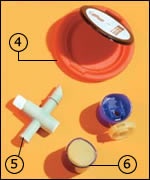 | Примеры сборки в процессе формования: - Вентиляционная решетка из PBT, ABS, и PP от Innatech.
- Медицинский клапан из PC, PP, и TPV от MGS Mfg.
- Поворачивающийся дозатор для соков из PP и PE от Gram Technology.
- Дозатор с диском сверху из PP от Ferromatik Milacron.
- Перепускной клапан с передвижным центральным элементом из PP и PE от Gram Technology.
- Нажимной дозатор из PP для продуктов личной гигиены от Ferromatik Milacron.
| Обсуждение этой проблемы с теми, кто занимается формованием, изготовлением пресс-форм и оборудования, скоро делает очевидным тот факт, что сам термин “сборка в форме” (или IMA) может определяться самым различным образом. Для целей данной статьи мы будем отграничивать его от общей области использования многократного формования или формования поверх жесткого на мягкое. Хотя для сборки в процессе формования обычно требуется многократный впрыск, суть этого явления заключается в соединении внутри пресс-формы отдельных компонентов, которые в противном случае пришлось бы соединять вне формы с помощью сопрягающей клепки, сварки или адгезионного связывания. “Если в процесс формования включается операция, которая должна реализоваться далее по технологической цепочке, можете рассматривать это как сборку в процессе формования”, - говорит Боб Хэр, генеральный директор отделения в США компании Ferromatik Milacron Europe. Может показаться, что под это определение подходит тканевое или ковровое ламинирование. Но это можно рассматривать как форму формования с заливкой: широко используемого метода, рассмотрение которого лежит за рамками данной статьи. Все станет ясно из приводимых примеров, которые будут рассматриваться далее, IMA это более, нежели просто формование поверх или формование заливкой, хотя обе или одна из этих технологии могут использоваться при реализации технологии IMA. Множество преимуществ Как это обычно бывает с другими операциями, производимыми в процессе формования, и повышающими стоимость продукции, достоинства IMA частично связаны с экономической выгодой и частично с повышением качества. “Существует потенциал для создания более прочного продукта, который не подвергается усадке или короблению, возникающим при осуществлении вторичных операций, особенно в тех случаях, когда соединяются две или более части одной детали”, - говорит Уэйд Кларк, президент компании, занимающейся формованием и изготовлением пресс-форм, Electroform. “Можно производить одну цельную деталь с меньшими затратами в одной установке с небольшой пресс-формой. Но если рассмотреть все затраты, связанные с включением детали в работу сборочной линии и с самой линией, экономия от включения сборки в формование будет огромной”, - добавляет Йоаким Крагл, менеджер по технологии обработки компании Engel. “Мы отвечаем только за одну установку и одну технологию. Если бы мне надо было осуществить сборку детали из трех компонентов, то было бы три автоматизированных линии, это увеличивает потенциальные возможности нарушения производственного процесса”, - отмечает он. Отказ от использования конвейеров, загрузочных бункеров, приспособления для крепежа, установок для ультразвуковой сварки и т. д. позволяет устранить потенциальные источники лома деталей, который возникает из-за неправильного обращения, расположения, отклонений от технологии или загрязнения. Создатели установок и пресс-форм также сходятся во мнении по поводу и других преимуществ, которые дает IMA: - Производство готовой детали прямо в форме позволяет исключить необходимость ведения учета для незавершенного производства.
- IMA позволяет обойтись без отдельных прессов и пресс-форм, что уменьшает потребность в трудозатратах и производственных площадях.
- IMA позволяет осуществлять правильное фиксирование или размещение деталей для сборки, что может быть большим плюсом для деталей косметического назначения.
- IMA позволяет снизить затраты времени на производство сборки по сравнению с тем количеством времени, которое необходимо для формования каждого из компонентов в отдельности с последующим их соединением.
- IMA позволяет производит детали со свойствами, которые были бы слишком затратны, или которые вообще невозможно было бы получить за счет традиционных методов с технологической цепочкой.
IMA обычно требует большого объема партии, поскольку инструментарий может потребовать на 30 - 70% больших затрат, чем при использовании стандартных пресс-форм с той же кавитацией. Источники, как правило, сходятся во мнениях, что партии деталей примерно в 250,000 являются кандидатами для IMA. Они также согласны с тем, что IMA развивается в Европе более быстрыми темпами, чем в Северной Америке, и преимущественно в области производства автомобильных деталей и потребительских товаров, а также, в меньшей степени, деталей медицинских устройств. Специальные технологические разработки для IMA скорее делаются в области инструментария, нежели в области конструкций прессов для формования. Такие производители установок, как Arburg, Engel, Krauss-Maffei и Milacron считают, что установка для IMA не сильно отличается от установок для других многокомпонентных формовочных работ, но отмечают, что отличие заключается во владении ноу-хау интеграции средств автоматизации и программирования последовательности операций. “Если установка снабжена системой управления с обратной связью, которая может обеспечивать воспроизводимость и точность реализации технологии, ее можно использовать для сборки в процессе формования”, - говорит Петер Липп, генеральный менеджер по литьевому формованию компании Krauss-Maffei. В некоторых случаях поставщики специальных инструментов для IMA сотрудничали с определенными создателями прессов. Примером может служить сотрудничество между Ferromatik и Foboha, немецкой компанией, изготавливающей пресс-формы с одним или более четырехгранным поворачивающимся “кубом”. Аналогичным образом датская компания, Gram Technology , поставщик пресс-форм с многогранным поворачиванием “Spin Stacks,” сотрудничает при реализации ряда проектов с Demag Plastics Group. Engel использует различные подходы: “Мы либо создаем пресс-форму сами, либо работаем с нашими партнерами в Северной Америке”, - говорит Крагл. “Поскольку мы также создаем установки для многокомпонентного формования и у нас есть потенциал в области автоматизации, сборка в процессе формования является для нас существенным компонентом нашей профессиональной компетенции”. Множество способов внедрения IMA Компании, производящие пресс-формы, разработали целый ряд способов внедрения IMA. В рамках некоторых подходов используются односторонние инструменты с перемещающейся или вращающейся плитами. В других случаях используются многоэтажные пресс-формы с множеством линий разъема с традиционной линейной конструкцией или более новыми конструкциями с ротационными столами. В целом ряде случаев в односторонних инструментах используются вращающиеся или же подвижные плиты для изменения конфигураций гнезд между впрысками. Как односторонние, так и многоэтажные пресс-формы приобретают дополнительную универсальность за счет одного или нескольких револьверных устройств центра поворота, у каждого из которых могут иметься четыре грани для выполнения различных функций. И для многих применений используется робототехническое устройство или аналогичное устройство для перемещения деталей между гнездами или даже между установками. 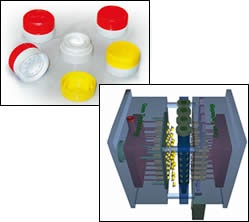 Инструмент Spin Stack от компании Gram Technology формует крышку с резьбой и соответствующее горлышко с резьбой и с отрывным язычком в двух отдельных частях формы, прежде чем соединить обе детали вместе. Так, например, технология IMA для односторонних пресс-форм это новая концепция “формования с перемещением” от производителя пресс-форм StackTeck. По словам менеджера общих продаж Джордана Робертсона, погрузочно-разгрузочное устройство инструмента приводится в движение механически за счет движения пресс-формы для перемещения деталей из одного гнезда в другое. “Манипулятор робота приводится в движение положением хода центральной части стека”, - говорит Робертсон. Здесь используется спиральное устройство для управления роботом через движение зажимного устройства”. Перемещение с помощью робототехнического устройства из одной установки в другую используется при создании применения от Gram Technology. Два прозрачных поликарбонатных корпуса формуются на двух формах “Spin Stacks” на одной установке, а силоксановая мембрана переносится с отдельной установки и вставляется в один из корпусов. При одном положении поворачивающихся стеков, контактирующая поверхность поликарбонатного корпуса повторно нагревается так, что оба корпуса свариваются при соединении расположенных друг против друга стеков. Компания Engel предложила вариант этой технологии для производства состоящего из двух компонентов фильтра грубой очистки вентиля из LSR и PBT. Детали отдельно формуют на установке без поперечной планки со смещенным ротационным столом. Робототехническое устройство собирает деталь в форме за счет прижимания одной детали к другой для сопрягающейся клепки. Более ранняя односторонняя концепция IMA разработана компанией JSW, которая является партнером Sakamoto Tool and Die Ltd. из Японии в деле разработки технологии Die Slide Injection (DSI). Представленная на рынок в 1991 г. DSI позволяет производить полые детали с помощью формования двух отдельных половин с последующим их соединением за счет перемещения плиты. Окончательно два компонента соединяются с помощью герметизации формованием поверх. По словам Роберта Коламбуса, генерального директора Чикагского технического центра JSW, две таких системы уже используются в Азии. 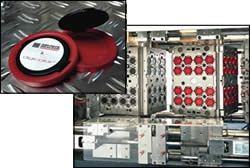 Высокопроизводительная пресс-форма TwinCube от компании Foboha была продана в прошлом году Stull Technologies для производства полипропиленовых крышек и оснований, которые приклепываются друг к другу, инструментом для формования разбрасывателя крышек для дисков. |