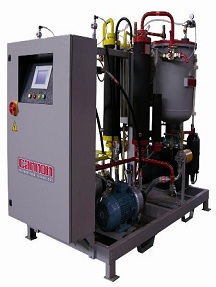
В себестоимости отдельных видов продукции доля исходного сырья может доходить до 80-85 процентов! При этом стоимость сырья, перерабатываемого в течение года, легко может оказаться на порядок выше, чем стоимость самой машины. Нетрудно подсчитать, что при таком раскладе уже 3-4 процента ежегодно сэкономленного сырья (а по-настоящему добротная машина мирового уровня в сравнении с машинами «так себе» может легко довести эту цифру до 8-10 процентов!) способны «обнулить» экономию, полученную в результате приобретения машины далеко не самого высокого качества. Ежегодно! А ведь эти машины рассчитаны на службу своему хозяину многие, многие годы - 12-15 лет как минимум! В этом еще одна огромная разница между пенозаливочной машиной и автомобилем, который даже при максимальном уровне экономичности на бензине, на «дизеле» ли, в состоянии сэкономить своему владельцу в год разве что на пару обедов в ресторане. При этом мы не говорим о качестве, которое обеспечивается только высококачественным же сырьем и оборудованием и служит источником дополнительной прибыли для производителя, обеспечивая ему стабильное положение на рынке. То, что давно очевидно для высокоразвитого европейского рынка, все еще упорно игнорируется на нашем. Иногда сознательно, из-за возможности сэкономить несколько тысяч евро, но чаще всего бессознательно, вследствие узкого кругозора и отсутствия информации во всей ее полноте. Именно поэтому основной целью данной статьи является, по возможности, пролить свет на ключевые моменты техники и экономики процессов переработки ППУ. Что же отличает по-настоящему хорошую машину от «так себе» оборудования, и за счет чего обеспечивается высокое качество и рентабельность в случае машин «брендового» уровня? Процесс переработки ППУ – это, в конце концов, суть реакция химическая, где роль машины заключается лишь в запуске процесса и обеспечении наиболее благоприятных условий его протекания, причем на всех без исключения этапах переработки! Начиная с подготовки компонентов. Один из них, полиол, или компонент А, будучи сложносоставным, должен постоянно поддерживаться в гомогенном состоянии за счет постоянного перемешивания. С этой целью рабочая емкость под полиол должна быть оснащена мешалкой, а самому компоненту, наряду с изоцианатом, или компонентом Б, даже в нерабочее время необходимо периодически «прогоняться» по т.н. «большому кругу» системы рециркуляции. Этот режим, названный режимом «выходного дня», позволяет поддерживать машину и сырье в состоянии постоянной готовности. Как режим «stand by» в телевизоре или компьютере. Под готовностью сырьевых компонентов понимается чистота от разного рода механических включений, обеспечиваемая системой патронных, а лучше пластинчатых, самоочищающихся фильтров, а также поддержание температуры на заданном уровне (22-24ºС) с помощью системы термостатирования. Здесь эта задача, в частности, возложена на трубчатые теплообменники на возврате компонентов в расходные емкости после рециркуляции. Желательно, чтобы и сами емкости были с водяной рубашкой, поддерживающей заданный режим температуры. Нагрев воды производится ТЭНами, охлаждение – отдельным холодильным агрегатом, или, как его еще подчас называют, чилером, предлагаемым в качестве опции там, где отсутствует сетевая охлажденная вода с температурой не выше 10-12ºС вне зависимости от времени года. Расходные емкости, кроме того, должны быть оснащены датчиком уровня (рабочего и аварийного минимума и максимума), управляющим автоматической системой их пополнения из транспортных бочек с помощью т.н. «бочковых» пневматических насосов. Подготовленные таким образом компоненты подлежат дозированию и смешиванию в заданном соотношении. Дозированию – высокоточному, которое способны обеспечить только высококачественные насосы аксиально-поршневого типа. Насосы могут быть регулируемой или постоянной производительности. Во втором случае производительность, причем даже еще в большом диапазоне, регулируется частотными вариаторами. Предельно высокий уровень технологической гибкости - в комбинации переменной производительности с «частотниками». Желательно наличие т.н. магнитных муфт, позволяющих уйти от то и дело протекающих и требующих замены уплотнительных прокладок, особенно на агрессивном изоцианате. Дозирование - важнейший этап переработки, сопоставимый по важности лишь с процессом смешивания и заливки. А это уже задача смесительной заливочной головки, по праву считающейся «базовым элементом» любой заливочной машины. В 90 процентах случаев идеальным вариантом головки высокого давления является двухкамерная головка, изобретенная Cannon в середине 70-х годов прошлого века, и в числе прочих достоинств обеспечившая этой итальянской компании всемирную славу и известность. Не говоря уже о коммерческом успехе. Это и не удивительно, поскольку двухкамерная конструкция головки позволила разрешить ранее неразрешимую дилемму, заключавшую в себе две противоречащие одна другой задачи: создать, с одной стороны, высочайший режим турбулентности с целью идеального смешения компонентов и, с другой, тут же «погасить» эту турбулентность с целью выхода полученной смеси из головки равномерным и, главное, ламинарным потоком, что, вопреки расхожим мнениям, создает наиболее благоприятные условия для дальнейшего протекания процесса пенообразования и растекания пены. |