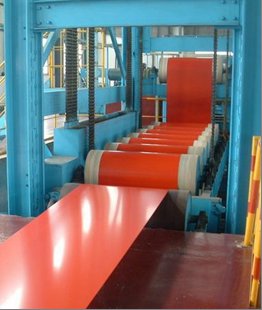
В реактор загружают гликоль и после его подогрева до 100°С — ангидриды. Иногда в реактор добавляют в количестве 10% от массы основных компонентов растворитель, образующий азеотропную смесь с выделяющейся при синтезе водой, что облегчает ее удаление (в этом случае способ получения НПС - в растворе). Процесс поликонденсации проводят при 170—200 °С и работающей мешалке в токе азота. Пары гликоля конденсируются в обратном холодильнике и конденсат стекает в реактор, а пары воды и азот отводятся через прямой холодильник. Водный конденсат собирается в сборнике. Контролируют процесс по кислотному числу. Готовый полиэфир после охлаждения до 70 °С сливают в смеситель, где растворяют в растворителе. Полученный раствор после охлаждения фильтруют и сливают в тару. В зависимости от состава смолы и исходных компонентов подбирают условия проведения процесса. Рассмотрим примеры технологических процессов синтеза НПС. Ниже приведены рецептуры смол, процесс получения которых будет описан. Примеры 2-6 представляют собой патентные разработки. Примеры рецептур НПС № | Компонент | Содержание, масс. части | Пример 1 | Неопентилгликоль | 402 | Адипиновая кислота | 94 | Изофталевая кислота | 404 | Тримеллитовый ангидрид | 100 | Пример 2 | Моноэтиленгликоль | 294 | Неопентилгликоль | 510 | Фталевый ангидрид | 409 | Изофталевая кислота | 458 | Терефталевая кислота | 511 | Пример 3 | Моноэтиленгликоль | 301 | Фталевый ангидрид | 551 | Адипиновая кислота | 852 | Пример 4 | Пропиленгликоль | 787 | Триметилолпропан | 127 | Адипиновая кислота | 155 | Изофталевая кислота | 1092 | Терефталевая кислота | 465 | Пример 5 | Моноэтиленгликоль | 124 | Неопентилгликоль | 468 | Диэтиленгликоль | 213 | Триметилолпропан | 131 | Адипиновая кислота | 689 | Изофталевая кислота | 695 | Пример 6 | Неопентилгликоль | 546 | Моноэтиленгликоль | 106 | 1,6-гександиол | 50 | 1,4-циклогександиметилол | 123 | Пропиленгликоль | 65 | Изофталевая кислота | 1271 | 1,4-цилкогександикарбоновая кислота | 146 | Пример 1. Получение смолы, состоящей из неопентилгликоля, адипиновой кислоты, изофталевой кислоты и тримеллитового ангидрида получают в два этапа. На первом, гликоль, кислоты и часть ангидридов подвергаются обработке для достижения низкого показателя кислотности при температуре 230-240 градусов по Цельсию, затем охлаждаются до температуры 170—180, добавляется остаток ангидридов и процесс продолжается при этой температуре, пока не будет достигнут показатель кислотности 45-50. Затем смолу растворяют в подходящем совместном растворителе и нейтрализуют амином. Пример 2. Реакция этерификации начинается при температуре 188ºС с добавлением 2 м.ч. тринонилфенилфосфита и 1 м.ч. оксидибутилового эфира. Вода, образованная в ходе реакции удаляется дистиллятором. Максимальная температура, при которой идет реакция – 245ºС. Через час после того, как температура достигнет 245ºС, кислотное число доводиться до 3,5 мг КОН/гр. Гидроксильное число полученной смолы – 18,5 мг КОН/гр. Вязкость при 158ºС)–260 дПа·с. Средний молекулярный вес – 5085 г/моль. Температура стеклования данной смолы – 50 ºС. Пример 3. Получение полиэфирной смолы с высоким содержанием сухого вещества происходит также в азотной атмосфере при механическом перемешивании. В качестве инициатора выступает фосфористая кислота (2 м.ч.). Реакция этерификации начинается при температуре 157ºС. Вода, образованная в ходе реакции, отводится дистилляцией. Максимальная температура, при которой идет реакция – 235ºС. Через час после того, как температура достигнет 235ºС, осуществляется азеотропная дистилляция с использованием ксилола, до тех пор, пока не будет достигнуто кислотное число 5 мг КОН/гр. Затем достигается кислотное число 2 мг КОН/гр. После охлаждения до температуры 170 ºС добавляются 857 весовых частей Solvesso 150™, чтобы достичь 75 % содержания сухого вещества. Кислотное число полученной твердой полиэфирной смолы –2 мг КОН/гр., гидроксильное число –20 мг КОН/гр. Вязкость при температуре 23ºС - 73 дПа·с. Средний молекулярный вес –4920 г/моль. Температура стеклования данной смолы – 15ºС. Пример 4. В качестве инициатора выступают дибутилоксид олова (1,1 м.ч.) и тринонилфенилфосфит (1,1 м.ч.). Реакция этерификации начинается при температуре 177ºС. Максимальная температура, при которой идет реакция – 230ºС. Через час после того, как температура достигнет 230ºС, осуществляется азеотропная дистилляция с использованием Solvesso 150™, до тех пор, пока не будет достигнуто кислотное число 6,4 мг КОН/гр. Затем достигается кислотное число 5,3 мг КОН/гр. Кислотное число полученной твердой полиэфирной смолы – 5,3 мг КОН/гр. Средний молекулярный вес –5410 г/моль. Температура стеклования данной смолы –49ºС. Пример 5. В качестве инициаторов выступают дибутилоксид олова (1 м.ч.) и тринонилфенилфосфит (2 м.ч.). Реакция этерификации начинается при температуре 165ºС. Максимальная температура, при которой идет реакция – 230ºС. Через час после того, как температура достигнет 230ºС, осуществляется азеотропная дистилляция с использованием Solvesso 150™, до тех пор, пока не будет достигнуто кислотное число 0,8 мг КОН/гр. После охлаждения до температуры 170ºС добавляются 857 весовых частей Solvesso 150™, чтобы достичь 70% содержания сухого вещества. Кислотное число полученной твердой полиэфирной смолы –0,8 мг КОН/гр. Вязкость – 49 дПа·с. Средний молекулярный вес –4590 г/моль. Температура стеклования данной смолы –14ºС. Пример 6. В качестве инициаторов выступают хлориндигидроксид (Fascat 4101™, 1 м.ч.) и тринонилфенилфосфит (2 м.ч.). Реакция этерификации начинается при температуре 183ºС. Максимальная температура, при которой идет реакция – 230ºС. Через час после того, как температура достигнет 230ºС, кислотное число доводится до 2,4 мг КОН/гр. Кислотное число полученной полиэфирной смолы –2,4 мг КОН/гр., гидроксильное число –25 мг КОН/гр. Средний молекулярный вес –4560 г/моль. Температура стеклования данной смолы –45ºС. Примеры производства материалов на основе НПС Для лучшего понимания дальнейшего использования НПС, приведем примеры материалов, получаемых на их основе. А). Покрытия на основе насыщенных полиэфиров, полученных по рецептуре №2 и №3, приведенной в предыдущей части главы. Coil coating (первичное покрытие) 1.1. Получение лакокрасочного покрытия Полиэфир, полученный в Примере 2, растворяется в следующем растворе: Solvesso 150™, эфир двухосновной кислоты, бутил гликоль в весовом соотношении 3:6:1 до получения 50% раствора. Вязкость полученного раствора - 17 дПа·с при температуре 23ºС. К 13,3 весовым частям полученной полиэфирной смолы добавляются 2,1 части противокоррозионного пигмента (Halox CW491™), 2.1 части противокоррозионного пигмента (Zinkfosfaat ZP/M™),4.1 части вещества, препятствующего оседанию пигмента в краске (10% раствор Bentone SD2 в Solvesso 150™), 6.4 части диоксида титана (Kronos 2160™), 10.4 части растворителя (Solvesso 150™/бутил гликоль 3:1), 0.2 части противопенной добавки/активатора (50% раствор Disparlon L1984™ в Solvesso 150™) и 5 частей наполнителя - Blancfixe Micro. Затем смесь доводят до состояния пигментной пасты, при температуре не выше 70ºС. После охлаждения до комнатной температуры к 7,5 частям данного 50% раствора полиэфирной смолы, добавляются 2,7 части полиэфирной смолы, полученной в Примере 3, 2.8 частей сшивающего агента, содержащего аминогруппы (Cymel 325™), 0.4 части катализатора (Nacure 4167™), 1.2 части сшивающего линейные полимеры агента (Epikote 828™). Полученная смесь разбавляется смесью растворителей - Solvesso 150™ и бутилгликоля - в соотношении 3:1, до получения вязкости с 40-59 Па·с (при температуре 23ºС, (DIN standard 53 211). Применение покрытия (предварительный слой - Coil coating). Оцинкованная сталь (Galfan) покрывается предварительным лакокрасочным покрытием, описанным в п. 1.1. Время отверждения в печи - 33 секунды при температуре 358ºС. Максимальная (пиковая) температура нагревания металла (ПТМ) – 210ºС. На предварительное покрытие наносится верхний слой на основе полиэфирной смолы - Uralac SN841™ (производства DSM Resins). Время отверждения в печи – 42 секунды при температуре 232ºС. Can coating Получение лакокрасочного покрытия Полиэфирная смола, полученная в примере 2, растворяется в следующем растворе: Solvesso 150™, сложного эфира двухосновной кислоты в весовом соотношении1:1 до получения 55% раствора. К 76.6 частям полученного раствора добавляются 18.4 части полиэфирной смолы с высоким содержанием сухого вещества, полученной в примере II и 5 частей эфира. В результате получается «смешанный полиэфир» с Тg 32ºС. К 97.5 частям полученной смеси добавляются 97,5 частей пигмента (Kronos 2310™) и 15 частей Solvesso 150™. Затем доводят до состояния пасты температуре не более 70ºС. После охлаждения до комнатной температуры к данной смеси к 18.5 частям «смешанной полиэфира», полученной выше, добавляются 14,9 частей изоцианового сшивающего агента (Uradur YB147™). Полученная смесь разбавляется Solvesso 150™ до получения вязкости с 90-110 Па·с при температуре 23ºС. Применение покрытия (Can coating) Покрытие, описанное в п. 2.1, наносится на электролитическую белую жесть при помощи 40 µm напылительной машины. Время отверждения в печи-10 мин при температуре 180ºС. Б). Покрытия на основе насыщенных полиэфиров, полученных по рецептуре №6 и №3, приведенной в предыдущей части главы. Coil coating (лицевое покрытие, top coat) Получение лакокрасочного покрытия. Полиэфирная смола, полученная в Примере 6 растворяется в смеси Solvesso 150™ и бутилгликоля (в соотношении 4:1) до получения 60% раствора. Вязкость полученного раствора 31 дПа·с. К 63.3 частям полученного раствора добавляются 31.5 частей полиэфирной смолы с высоким содержанием сухого вещества, полученной в примере 3 и 5.2 части Solvesso 150™. В результате получается 60% раствор «смешанной смолы» с Тg 18ºС. К 28.1 частям полученной смеси добавляются 67.4 части пигмента (Kronos 2310™) и 15.6 частей растворителя (Solvesso 150™). Затем доводят до состояния пасты при температуре не более 70ºС. После охлаждения до комнатной температуры к 18.5 весовым частям 60% раствора смешанных смол, добавляют 15.1 часть сшивающего агента (Cymel 303™, пр-ва компании Dyno Cytec), 4.9 частей катализатора (Dynapol BL1203™), 1.03 частей стабилизатора (Tinuvin 292™), 8.4 части матирующей добавки (Syloid ED 44™), 4.4 части катализатора (Nacure 2500™) и 8.4 части растворителя (Solvesso 150™/бутил гликоль 3:1). Применение лакокрасочного покрытия (верхний слой – top coat, coil coating). Лакокрасочное покрытие, описанное выше, используется в качестве завершающего верхнего слоя поверх предварительного покрытия (койл коутинг, алюминий). Время отверждения в печи - 41 секунда при температуре 300ºС. ПТМ – 241ºС. Can coating (лаковое покрытие) Получение лакового покрытия Полиэфир (№3) растворяется в смеси Solvesso 150™ и бутилгликоля (в соотношении 4:1) до получения 50% раствора. Вязкость полученного раствора 35. 68,4 части полученного раствора полиэфирной смолы смешиваются с 22,6 частями полиэфирной смолы (№3) и 9 частями смеси Solvesso 150™ и бутилгликоля ( в соотношении 4:1), в результате получается 50% раствор с Тg24°C. К 60.9 частям полученного раствора 8,4 части сшивающего агента Uramex BF891™ и 5 частей 75% раствора сшивающего агента Epikote 834™ в бутил гликоль ацетате, а также 18,5 частей растворителя (Solvesso 150™/изопрофорон 1:1). Применение покрытия Данное покрытие наносится на электролитическую белую жесть. Время отверждения в печи – 12 минут при температуре 185С. C текущей ситуацией и прогнозом развития российского рынка полиэфирных смол можно познакомиться в отчете Академии Конъюнктуры Промышленных Рынков «Рынок насыщенных полиэфирных смол в России». |