Широкое распространение процессов термоформования объясняется простотой, компактностью, относительной дешевизной используемого оборудования и технологической оснастки. Термоформование используют, прежде всего, при производстве тары и упаковки для пищевой, парфюмерной, фармацевтической, химической, нефтяной промышленностей, одноразовой посуды, а также целого ряда полых полимерных изделий, имеющих различное техническое назначение. Многие виды полимерных изделий, например, крупногабаритные и тонкостенные сложной конфигурации, можно изготовить только методами пневматического или вакуумного формования. Все вышеизложенные причины позволяют достойно конкурировать процессам термоформования с другими альтернативными методами производства изделий из полимерных материалов. Реализация методов термоформования достаточно проста: листовую или плёночную полимерную заготовку нагревают до температуры высокоэластического состояния, а затем, деформируя её различными способами, придают последней необходимую форму, фиксация которой осуществляется путём охлаждения отформованного изделия. В зависимости от способа создания движущей силы процесса деформирования заготовки в готовое изделие различают следующие основные методы термоформования пластмасс: вакуумный, пневматический, гидравлический, механический, комбинированный. При вакуумформовании (рис. 1) плоскую заготовку 3 из термопластичного полимерного материала, прижатую по периметру к рабочей камере вакуум формовочной машины прижимной рамой 2, сначала с помощью нагревательного устройства 1 разогревают до высокоэластического состояния (рис. 1а). Затем (рис. 16) в полости, образованной поверхностями заготовки 3 и формующей матрицы 4 (или формующего пуансона), создают разряжение, в результате чего за счет возникающего перепада давления происходит формование изделия 5. После охлаждения изделия до температуры его формоустойчивости последнее извлекают из формующего инструмента (снимают с формующего инструмента), предварительно открыв прижимную раму 2. 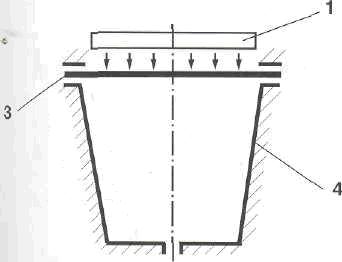 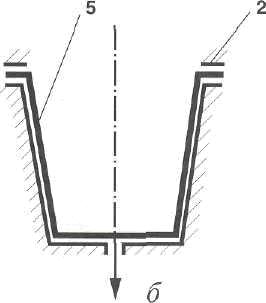
I — нагревательное устройство; 2 — прижимная рама; 3 — плоская полимерная заготовка; 4 — формующая матрица; 5 — отформованное изделие Рис. 1. Схема реализации процесса вакуумного формования Реализация процессов пневмоформования отличается от вакуумного формования только тем, что перепад давления создают за счёт использования в качестве рабочей среды сжатого газа, как правило, сжатого воздуха, с избыточным давлением до 2,5 МПа. При гидравлическом формовании роль рабочей среды выполняет подогретая жидкость, нагнетаемая насосом под давлением 0,15-2,5 МПа. Механическое формование (механотермоформование) (рис. 2) отличается от процессов пневматического формования тем, что придание плоской разогретой заготовке 3 формы готового изделия 5 осуществляется за счёт её механической вытяжки металлическим пуансоном 4. 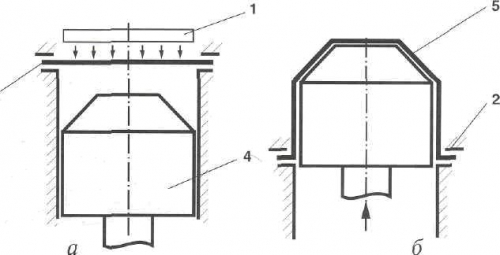 I — нагревательное устройство; 2 — прижимная рама; 3 — плоская полимерная заготовка; 4 — формующий пуансон; 5 — отформованное изделие Рис. 2. Схема реализации процесса механотермоформования Следует отметить, что современные технологии производства предусматривают и совмещение разных методов формования изделий, например: пневмовакуумное, пневмомеханическое и т.п. Схема реализации механовакуумного формования приведена на рис. 3. Реализация этого комбинированного метода формования состоит из двух этапов: на первом из них (рис. За) разогретую до необходимой температуры нагревателем 1 плоскую заготовку 2 механически вытягивают с помощью пуансона 4. На втором этапе (рис. 36) вытянутую заготовку формуют в матрице 5 за счет создания вакуума в ее полости. Среди всех видов пневмо- и вакуумформования можно выделить три основных: позитивное, негативное и свободное. При позитивном формовании (формование на пуансоне) внутренняя поверхность изделия в точности воспроизводит форму или рисунок формующего инструмента. Негативное формование (формование в матрице) дает возможность получать изделия, наружная поверхность которых в точности воспроизводит форму или рисунок внутренней поверхности матрицы. Свободное формование осуществляют в пройме прижимной рамы машины без использования формующего инструмента. Кроме перечисленных основных, существуют и другие разновидности технологических методов термоформования изделий из плоских полимерных заготовок.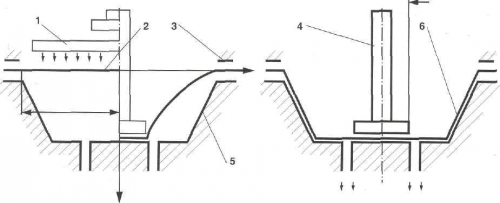 а б 1 — нагреватель; 2 — плоская заготовка; 3 — прижимная рома; 4 — пуансон; 5 — матрица; 6 — отформованное изделие Рис. 3. Схема реализации комбинированного процесса механовакуумформования изделий из плоских полимерных заготовок (а - нагрев и предварительная механическая вытяжка заготовки; б - вакуумформование изделия) Особенности технологии термоформования Во всех методах формования изделий из пластиков лист термопласта перед формованием нагревают до температуры высокоэластичного состояния, а затем закрепленную по контуру заготовку устанавливают над формовочной камерой. Формование происходит под действием перепада давлений, создающегося между внутренней и внешней поверхностями листа. При вакуумформовании этот перепад равен разности давления окружающего воздуха и остаточного давления в форме, при пневмоформовании - разности между давлением сжатого воздуха и атмосферным давлением, при штамповке - давлением на заготовку с помощью специальных механических пуансонов. Во многих случаях формованию предшествует подготовительная операция по изготовлению заготовок. При массовом и крупносерийном производстве изделий, как правило, либо завод-поставщик сырья, согласно договоренности, поставляет мерные заготовки, либо проектируется многоместная оснастка с учетом размеров выпускающихся листов термопласта. Кроме того, в случае применения комплексных линий, экструдер настраивается на выпуск листов с необходимыми габаритами. При изготовлении мелких серий производится раскрой заготовок из стандартных листов. При этом учитывается, что листовые термопласты при нагреве дают усадку. Поэтому перед раскроем материала следует определить усадку для данной партии материала вдоль и поперек направления экструзии. Учитывать при раскрое следует и ориентацию исходного листового материала (направление экструзии). В направлении наибольшей ориентации исходной заготовки готовое изделие должно получить наименьшую вытяжку и, наоборот, в том направлении, в котором заготовка была наименее ориентирована (поперек экструзии), вытяжка должна быть наибольшей. При несоблюдении этого условия возникает неравномерность утонения материала, неоднородность деформационных свойств, остаточные напряжения, что приводит к деформации изделия после съема с пресс-формы. Раскрой листовых материалов производится вручную резаками, а также гильотинными ножницами, дисковыми или ленточными пилами. Сегодня, как правило, используются плоскощелевые экструдеры с рабочей шириной экструдированного листа равной ширине матрицы формовочной машины. В случае использования широкоформатного экструдера устанавливаются станции резки и дополнительные посты намотки. К заготовкам из термопластов, подлежащим формованию, предъявляются такие требования: они должны быть однородными, без посторонних включений и изъянов; разнотолщинность заготовок не должна превышать 10% по отношению к номинальной толщине; для листовых заготовок вязкость расплава материалов должна обеспечивать возможность нагревания в закрепленной раме и не давать большого провисания листа; термическая усадка листа должна быть минимальной и не превышать 3-5%. Перед формованием заготовки нагреваются до температуры формования. Как правило, нагрев осуществляется вне формовочной зоны в различных электронагревательных устройствах. При пневмоформовании лист разогревается в свободном состоянии без фиксации в прижимной раме. Такой нагрев улучшает качество получаемого изделия за счет максимальной релаксации внутренних напряжений. При вакуумформовании лист нагревается в жестко зажатом состоянии, поэтому возможно провисание листа под собственной тяжестью вследствие температурного расширения или чрезмерного снижения вязкости материала при температуре формования. Для предотвращения провисания листа применяют предварительную вытяжку и ориентацию листовых материалов при экструзии. Возникающая при разогреве таких листов до рабочих температур усадка компенсирует тепловое расширение материала. Разогрев листа следует производить равномерно. Неравномерный разогрев ведет к возникновению в листе внутренних напряжений, неравномерной вытяжке и образованию на изделии складок. Для создания равномерного температурного поля повышают температуру периферийных участков нагревателя с целью компенсации тепловых потерь в окружающую среду. В этом случае нагреватель должен быть разделен на зоны с индивидуальными регуляторами для дифференцированного регулирования температуры по всей поверхности нагреваемого листа. Допустимый перепад температур по поверхности листа ±(5-10)°С. Нагрев листа до температуры формования может осуществляться инфракрасными нагревателями, расположенными с одной или с обеих сторон нагреваемого листа. В качестве нагревателей используют элементы сопротивления, изготовленные из нихромовой проволоки, лент или стержней. На некоторых машинах в качестве нагревательных элементов используют трубчатые электронагреватели (ТЭНы). Они состоят из жаропрочных металлических трубок, внутри которых расположена нихромовая спираль, изолированная от стенок трубки электроизоляционным материалом, обладающим хорошей теплопроводностью (например, оксидом магния). Применяют также кварцевые излучатели, трубка которых заполняется инертным газом. По оси трубки в дисковых изоляторах проходит вольфрамовая спираль, нагревающаяся при работе до 2473° К. Эти нагреватели работают в коротковолновом диапазоне инфракрасного излучения. Они обладают малой инерционностью и высоким КПД. Конструкция нагревателя должна обеспечивать равномерную температуру по всей поверхности нагреваемого листа. Поэтому, если площадь обогреваемого листа превышает 0,5 м2, нагреватель разбивают на несколько тепловых зон с индивидуальным регулированием температуры. В каждую зону, снабженную индивидуальным регулятором температуры, входит один или несколько нагревательных элементов, сгруппированных таким образом, чтобы обеспечивать компенсацию потерь тепла на краях листа. Для нагрева жестких (полистирол, поликарбонат, полипропилен) и толстолистовых термопластов рекомендуется применять двусторонний обогрев. Поэтому машины снабжают двумя нагревателями с одинаковой площадью нагрева, излучающие поверхности которых направлены навстречу друг другу. При этом в большинстве случаев мощность верхнего нагревателя в 1,5 раза больше мощности нижнего. На одно- и двухпозиционных машинах чаще всего применяют подвижные нагреватели, перемещающиеся в горизонтальной плоскости; на многопозиционных обычно используют неподвижные нагреватели. Подвижный нагреватель для одностороннего нагрева состоит из каркаса и нагревательных элементов. Нагреватель находится в рабочем положении, в котором он остается до тех пор, пока лист не будет нагрет до заданной температуры. По окончании нагрева он отключается и отодвигается влево. При этом он оказывается над штабелем заготовок, верхняя из которых предварительно подогревается теплом, выделяемым остывающим нагревателем. В некоторых конструкциях нагрев листовых заготовок производится в закрытых камерах. По принципу действия эти камеры можно разделить на камеры с чисто конвективным обогревом (с помощью горячего воздуха), камеры с инфракрасными нагревателями и камеры со смешанным лучисто-конвективным обогревом. В камерах с конвективным обогревом нагрев заготовки осуществляется потоком горячего воздуха, поступающего от воздуходувки через электрический калорифер. Недостатком таких камер является большая продолжительность нагрева, достигающая для толстолистовых заготовок 40 мин. В камерах инфракрасного обогрева обычно используют двусторонний нагрев. Применение таких камер полностью исключает влияние микроклимата цеха на скорость и равномерность нагрева, однако наличие камеры утяжеляет машину и увеличивает ее габариты. Наилучшие результаты дает применение комбинированных камер, сочетающих инфракрасный и конвективный нагрев. Контроль температуры нагреваемого листа может производиться либо по продолжительности нагрева, либо по показаниям измерительных приборов. Применяют как контактные, так и бесконтактные методы замера. К контактным методам относится использование различных термопар, чувствительный элемент которых соприкасается с поверхностью заготовки. Иногда прибегают к заделке спая в толщу листа. Бесконтактные методы замера температуры основаны на применении различных пирометров. При нагревании термопластов можно отметить два ясно выраженных перехода: из твердого стеклообразного состояния в высокоэластическое и затем в вязкотекучее. Между температурой стеклования и температурой текучести лежит область высокоэластического состояния, в которой термопласты, подобно каучукам, могут растягиваться, если на них действует внешняя сила, и возвращаться к исходной форме, если действие этой силы прекращается. Эта область может быть как очень малой, так и настолько большой, что температура текучести может быть практически недостижимой, т.к. еще до перехода в вязкотекучее состояние полимер претерпевает термическое разложение. У аморфных полимеров (ПС, ПММА) область высокоэластического состояния значительна (до 60-70°С), полимеры же с преобладанием кристаллической структуры (ПЭ, ПП) имеют меньшую область (около 10°С), что вносит определенные сложности в переработку таких материалов методами термоформования. В момент вытяжки заготовки в материале возникают упругие силы, которые после снятия давления формования стремятся вернуть изделие к первоначальной плоской форме заготовки. Чтобы зафиксировать конфигурацию отформованного изделия, не снимая давления формования, изделие охлаждается до температуры, ниже температуры стеклования. С бизнес-планом организации производства тортниц из БОПС можете познакомиться в работе Академии Конъюнктуры Промышленных Рынков «Бизнес-план организации производства тортниц из БОПС ленты». |