При этом была использована комплексная литьевая форма в комбинации с высокоточной техникой компании Arburg: двухпозиционная литьевая форма (4+4-гнезда) с возможностью светолучевой обработки изделия, поворотное устройство Index, тяговый механизм сердечника, устройство для извлечения изделий из формы, а также электрическая универсальная литьевая машина с гибкой роботизированной системой. Другими участниками этого проекта были компании: Elmet (литьевая форма, LSR-установка), Momentive Performance Materials (LSR), Kiki (монтаж, испытания на герметичность) und Sabic (термопласт Ultem). Компания Dymotek продемонстрировала производство высокоточных одноходовых насосов для перекачивания жидкостей со встроенными уплотнителями. Электрическая универсальная литьевая машина модели Allrounder 570 A для изготовления двухкомпонентных изделий из силиконового каучука работает с усилием запирания 2000 кН (220 т) и оснащена двумя узлами впрыска типоразмера 170 (3.7 унций). Жидкий силиконовый каучук был выбран для изготовления как насосного устройства, так и уплотнителей с тем, чтобы обеспечить требуемую водонепроницаемость изделия, устойчивость его к коррозии и экстремальным температурам. Масса впрыска из расчета на одно изделие составляет 14,46 г, а время цикла – 45 с. ТПА оборудован роботизированной системой Multilift V вертикального действия, с помощью которой изделия забираются с устройства для извлечения их из литьевой формы и передаются на станцию сборки и проверки функциональности. Узлы впрыска расположены по схеме L: термопласт впрыскивается при этом с задней стороны машины, а LSR – традиционным образом в горизонтальном направлении через неподвижную плиту. Формуемые из материала Ultem изделия во время цикла их изготовления подвергаются в автоматическом режиме воздействию излучения для обеспечения более прочного соединения силикона с материалом Ultem. Узел впрыска, предназначенный для переработки LSR и термостатируемый с помощью жидкости, оснащен специальным транспортно-смесительным шнеком, а также находящимся под пружинной нагрузкой дисковым обратным клапаном. Оптимальное нагревание литьевой формы обеспечивается с помощью 21 электрического нагревательного контура. 15 из них находятся на неподвижной плите и 6 – на перемещающейся плите. Охлаждающая система каналов включает в себя 8 контуров охлаждения. Описание процесса изготовления изделий
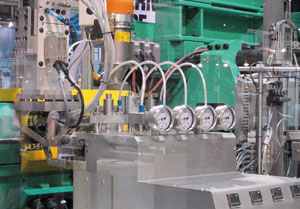
Полностью собранные изделия проходят полномасштабную проверку (по падению давления) для выявления возможных неплотностей 4+4-гнездная литьевая форма оснащена индексной плитой, поворот которой осуществляется с помощью гидравлического тягового сердечника. На первой стадии технологического процесса в нижней части литьевой формы из термопластичного материала Ultem изготавливаются одновременно четыре заготовки, которые затем подвергаются воздействию света с целью обеспечения более прочного соединения термопласта с силиконом. После поворота индексной плиты, на второй станции методом литья силиконового каучука на подложку из термопласта Ultem осуществляется формование силиконовых частей (насоса и уплотнителя). Силиконовый каучук подается в каждое гнездо формы через два оборудованных запорными иглами сопла. По окончании процесса литья под давлением четыре готовых насосных блока удаляются из литьевой формы с помощью извлекающего устройства, которое передает эти блоки на роботизированную систему Multilift V вертикального действия, оснащенную четырехгнездным захватом. Роботизированная система поворачивает изделия на 180° и транспортирует их на сборочную станцию, где в силиконовый насос с нижней стороны вставляются сопла – отдельно изготовленные литые изделия, поступающие от разделительного механизма. Сопла сначала запрессовываются и прижимаются к уплотнительной губке, а затем с помощью воздействующего с верхней стороны подающего цилиндра устанавливаются в требуемое положение. На следующей стадии технологического процесса осуществляется 100%-ная проверка правильности работы собранных насосов путем измерения потери давления и установления тем самым наличия неплотностей. В процессе испытаний определенное давление поддерживается в течение примерно 2 с. Если в течение этого времени давление упадёт ниже предварительно заданного минимального уровня, изделие признается дефектным и отправляется в контейнер для брака. Если контролируемые показатели оказываются в пределах допусков, готовые изделия укладываются на конвейер для отправки на охлаждение и упаковку. Комплексная литьевая форма 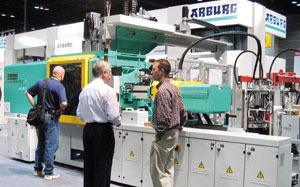
Компании Dymotek и Arburg представляют комплексную линию для изготовления двухкомпонентных изделий из термопластов и жидкого силиконового каучука Специфическое требование, предъявляемое к литьевой машине и литькомпонетных изделий из термопласта и силиконового каучука, заключается в том, что внутри литьевой формы горячие и холодные зоны должны быть оптимальным образом отделены друг от друга. Это необходимо для надежного обеспечения заданных условий вулканизации LSR-компонента. В нижней части 4+4-гнездной литьевой формы находится зона с горячим каналом, предназначенная для изготовления заготовки из термопласта, а в верхней части – холодноканальная зона, где без образования отходов осуществляется формование насоса и уплотнителя из LSR. Еще одной особенностью является то, что гидравлическое сопло с запорной иглой расположено в литьевой форме. Кроме того, литьевая форма оборудована выталкивающим устройством, которое извлекает из нее изделия и передает их на роботизированную систему Multilift V. Простое обслуживание с помощью системы управления Selogica Вся установка, включающая в себя роботизированную систему Multilift V, дозирующую и вакуумирующую системы для LSR, а также три масляных термостата, обеспечивающих максимальную температуру 160°, программируется и управляется непосредственно с помощью системы управления Selogica с сенсорным экраном. Эта система управления содержит расширенный набор символов для процесса переработки LSR и возможность графического изображения процесса работы роботизированной системы Multilift. Прочие периферийные устройства подключаются к Selogica через специальные разъемы. Источник: Пласткурьер
|