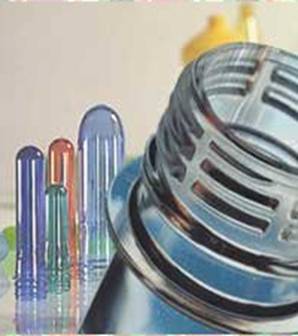
Твёрдое, бесцветное, прозрачное вещество в аморфном состоянии и белое, непрозрачное в кристаллическом состоянии. Переходит в прозрачное состояние при нагреве до температуры стеклования и остаётся в нём при резком охлаждении и быстром проходе через так называемую «зону кристаллизации». Одним из важных параметров ПЭТФ является вязкость определяемая длиной молекулы полимера. С увеличением вязкости скорость кристаллизации снижается. Прочен, износостоек, хороший диэлектрик. Существующие на сегодняшний день технологии производства ПЭТФ разделяют по типу синтеза:
1) Синтез полимера посредством поликонденсации этиленгликоля с диметилтерефталатом (ДМТ). Данная технология широко использовалась до начала 90-х годов прошлого века. В настоящее время практически не используется по причине высокой себестоимости производства ДМТ. 2) Синтез полимера посредством поликонденсации этиленгликоля с терефталевой кислотой. Также схемы синтеза полимера разделяют на периодическую (используется преимущественно при мелко-тоннажном производстве) и непрерывную. Краткое описание "классической" двустадийной установки синтеза высоковязкого ПЭТФ. Классическая схема синтеза ПЭТФ состоит из двух стадий. Первая стадия, именуемая стадией поликонденсации состоит из: * пастосмешения - процесса при котором смешивается основное сырье, катализаторы и добавки; * этерификации - процесса получения сложных эфиров из кислот и спиртов; * предполиконденсации и поликонденсации - процесса синтеза полимера из полифункциональных соединений, сопровождающийся выделением низкомолекулярных побочных продуктов; * гранулирования - процесс получения низковязкого аморфного полимера в виде бесцветных гранул. На второй стадии классической схемы синтеза ПЭТФ, именуемой твердофазной дополиконденсацией (Solid State Polycondensation или SSP), происходит нагрев предварительно охлажденного гранулята до высоких температур с целью увеличения молекулярной массы, а следовательно повышения вязкости полимера. Технологический процесс синтеза ПЭТФ пищевого назначения 2R MTR Компании Uhde Inventa-Fischer GmbH состоит из следующих этапов: 1) Приготовление катализатора и стабилизатора - порошкообразный или жидкий катализатор, а также стабилизатор и добавки растворяются в гликоле при повышенной температуре. Раствор направляется в резервуары и далее для смешивания с основным сырьем. 2) Смешивание пасты - ТФК, изофталевая кислота (ИФК), раствор гликолей с катализаторами и стабилизаторами перемешиваются в емкости в определенном соотношении. Емкость оборудована специальной конструкцией, которая обеспечивает образование однородной пастообразной массы. 3) Этерификация и поликонденсация (двухреакторная технология) - основными аппаратами реакционной системы этерификации и поликонденсации являются запатентованные Компанией реакторы ESPREE® и DISCAGE®. Паста поступает в нижнюю часть реактора ESPREE® колонного типа, где происходит реакция этерификации при температуре до 270 градусов Цельсия. Окончательная вязкость полимера достигается в реакторе DISCAGE®, в котором продукт находится под вакуумом. Данный реактор оснащен мешалкой коробчато-клеточного типа без центрального вала с редукторным двигателем инверторным приводом, оснащенной многочисленным перфорированными дисками и съемниками, действующий как винтовой конвейер. Это позволяет транспортировать полимер со стороны низкой вязкости в сторону высокой вязкости, а затем через разгрузочный желоб в аппарат резки (гранулирования). 4) гранулирование и кристаллизация - в аппарате резки поток расплава продавливается через перфорированную плиту в резательную камеру, через которую течет горячая вода (подводное гранулирование). Установленная за перфорированной плитой ротационная резальная головка режет жгуты полимера в гранулы, которые при контакте с ножом остывают и приобретают типичную сферическую форму. Далее гранулят направляется в центробежную сферическую сушилку, где происходит отвод технологической воды. Затем высушенный горячий гранулят выгружается из сушилки и кристаллизуется на виброконвейере. Гранулят собирается в термостатированном бункере, откуда подается в силос кондиционирования с помощью пневмотранспортной системы. 5) Кондиционирование гранулята - в силосе кондиционирования гранулят в противотоке обдувается воздухом с постоянной температурой для снижения содержания ацетальдегида без повышения вязкости полимера. Из силоса кондиционирования гранулят поступает в охладитель и затем в силосы хранения. Гранулят готов к растарке в транспортную упаковку. Управление одностадийным технологическим процессом полностью автоматизировано от момента загрузки сырья до упаковки товарного продукта в транспортную тару. C текущей ситуацией и прогнозом развития российского рынка ПЭТФ можно познакомиться в отчетах Академии Конъюнктуры Промышленных Рынков «Рынок ПЭТФ в России в 2008-2009 гг». www.polymery.ru |