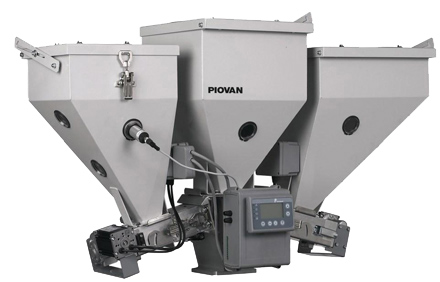
Объёмный дозатор Piovan на три компонента (первичка, вторичка, добавка) В этом случае загрузку можно осуществлять специальными шнековыми загрузчиками. Эти загрузчики передают сырьё не пневматикой по гибкому шлангу, а длинным стальным шнеком, вращающимся в специальной пластиковой трубе. Таким образом, во время передачи сырья из смесителя в экструдер сохраняется исходное качество смеси. 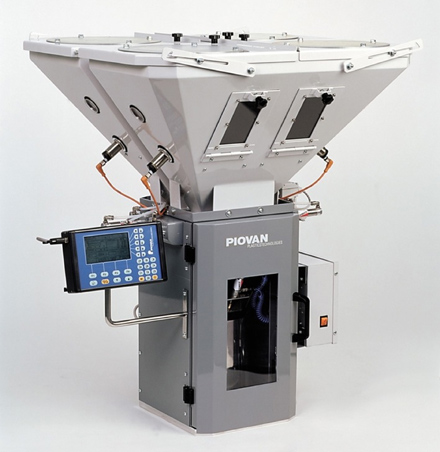
Гравиметрический дозатор Piovan В многослойном экструзионно-выдувном формовании скорость выхода расплава из экструдера имеет ещё более принципиальное значение, т.к. это оказывает влияние на распределение толщин слоёв в общей массе стенки изделия. Чем больше нестабильность выхода потока тем большими будут колебания процентного соотношения слоёв относительно друг друга (чем больше поток, генерируемый одним экструдером, тем толще слой за который «отвечает» этот экструдер). По этой причине для соэкструзионного выдува рекомендовано применение гравиметрических (весовых) дозаторов. Обычный дозатор просто вращает шнек, приблизительно регулируя объём подаваемого компонента; объём, но не массу. Как сказано выше, дроблёнка представлена в бесформенных частицах, поэтому при том же количестве оборотов шнека дозатора её может попасть в экструдер больше или меньше. Гравиметрический дозатор взвешивает количество подаваемого материала и, следовательно, позволяет соблюсти стабильную рецептуру смеси, что обеспечивает стабильную экструзию. Гравиметрическое дозирование в выдуве в общем-то рекомендовано не только для многослойных применений. Наиболее прогрессивные производства однослойных выдувных изделий так же стараются применять весовое дозирование, ведь ключ к успешному выдувному формованию – стабильность всех параметров, факторов и процессов. Сбор облоя При использовании внутри-машинных систем удаления технологического облоя (а такие системы применяются сейчас почти повсеместно) «лишний» пластик вырубается (или срезается) и просто падает вниз. В зависимости от типа устройств удаления облоя и системы внутренних склизов в машине точки выпадения могут быть расположены по-разному, однако всегда есть возможность собрать их из-под машины специальной конвейерной лентой. Небольшая по высоте (от пола) горизонтальная конвейерная лента располагается с лицевой стороны машины прямо под узлами смыкания. Ширина этого конвейера подбирается таким образом, чтобы беспорядочно ссыпающийся облой всегда попадал на ленту, а не на пол. Облой, упавший на пыльный пол, ещё менее приветлив при вторичной переработке, чем чистая дроблёнка, поэтому для дополнительной защиты по краям конвейера устанавливают пластины-ограждения. Эти пластины выполняют роль склизов, и улетевший в сторону фрагмент облоя благодаря такой защите всё равно спускается на ленту, а не мимо. Длина конвейерной ленты должна охватывать все точки выпадения облоя, т.е. всю ширину машины, а иногда и больше (если применяются ротационные срезчики облоя). 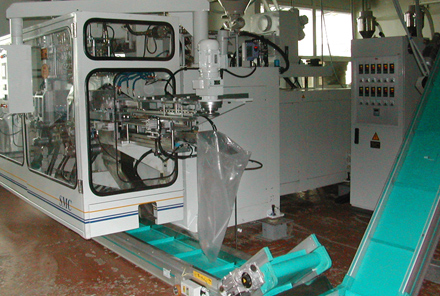
Экструзионно-выдувная машина SMC 3000DSTL с горизонтальным и наклонным конвейером Задача конвейера, описанного выше, собрать весь облой из-под машины. Вторая задача – транспортировка облоя непосредственно в дробилку и для этого используется второй конвейер. Второй конвейер обычно устанавливается перпендикулярно первой ленте и имеет наклонное направление транспортировки для подъёма облоя с горизонтального конвейера в приёмное окно дробилки. Переработка В отличие от дробилок, используемых для ТПА, которые задействованы время от времени, дробилки, приставленные к экструзионно-выдувным машинам, работают постоянно и это лишь часть их специфики. К другим особенностям выдувных дробилок можно отнести следующее: • Необходимость перерабатывать не только толстые и горячие фрагменты облоя, но и периодически целые выдувные изделия – внутренняя камера и система ножей дробилки должна быть спроектирована таким образом, чтобы изделие не подпрыгивало на ножах, а сразу разрубалось. • При отстройке машины могут возникать большие объёмы брака к переработке – дробилка должна быть способна в течение получаса-часа спокойно измельчать количество полимера в три-четыре раза превышающее штатный режим (дробление только облоя). • Кроме того, после отстройки накапливается количество дроблёнки заведомо превышающее её обычную пропорцию – дробилка должна либо иметь большую встроенную камеру для временного хранения излишков облоя, либо быть соединена пневмозагрузчиком с отдельностоящим хранилищем уже из которого дроблёнка будет передаваться дальше в смеситель-дозатор. • Дроблёнка составляет 30-50% смеси, из которой производится выдувное изделие, поэтому качество дроблёнки напрямую влияет на стабильность экструзионно-выдувного процесса и качество изделия – дробилка должна измельчать облой и брак в максимально равномерные и одинаковые по форме частицы. • На кусках облоя и, особенно, на бракованных изделиях (которые обычно просто бросают на пол, а потом собирают) скапливается пыль и грязь, поэтому дробилка должна иметь хорошую систему пылеотделения. Правильное дробление – ещё один фактор стабильности экструзионно-выдувного формования. Наиболее профессиональные и проверенные решения можно получить у компаний, специализирующихся именно на регрануляции. Наиболее известный эксперт по дробилкам и мировой лидер в этом направлении – шведская компания Rapid. Rapid выпускает модели, исполнения и различные опции к дробилкам в зависимости от применения и не только имеет специальную линейку для выдувного формования, но несколько сублинеек для конкретных выдувных задач.
|