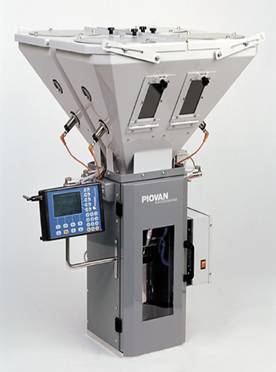
Обязательным для процесса является непрерывная подача сжатого воздуха и циркуляция воды для охлаждения (гидравлического масла, прессформ и других элементов), а также подготовка сырья в случае использования гигроскопичных материалов. Рекомендуемое дополнительное оборудование – это всевозможные системы для работы с сырьём (подача, переработка, смешивание) и некоторые другие узлы в зависимости от конкретного производственного проекта. Типовая схема взаимодействия периферийных устройств с основным оборудованием: 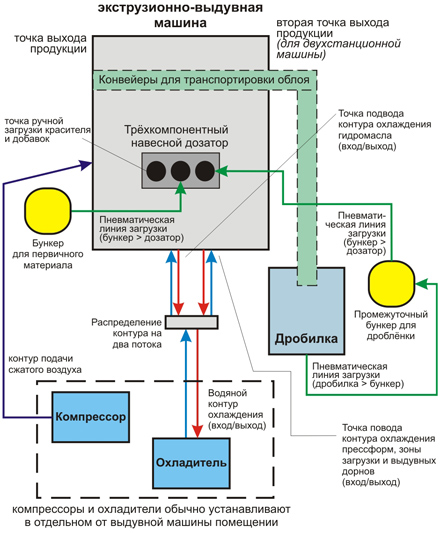
В первой части нашего материала мы поговорим об обязательном дополнительном оборудовании, а во второй – о рекомендуемом. Обязательное дополнительное оборудование Компрессор Вся концепция технологии выдувного формования вообще и экструзионно-выдувного формования в частности основана на использовании сжатого воздуха для придания окончательной формы изделию из эластичной пластиковой заготовки (будь то рукав или разогретая преформа). В экструзионно-выдувном формовании используют давление 7-8 бар. Непрерывная генерация сжатого воздуха для выдувной машины осуществляется воздушными компрессорами. Учитывая, что выдувная машина постоянно без резких скачков требует подачи сжатого воздуха, компрессор должен быть готов к интенсивной безостановочной генерации воздуха. При этом понятно, что работающий постоянно на пределе своей мощности и без пауз компрессор будет потреблять чрезмерное количество энергии, а главное – чересчур быстро исчерпывать свой ресурс. По этим причинам для экструзионно-выдувного формования лучше всего подходят компрессоры винтового типа с заведомо более высокой производительностью, чем нужно выдувной машине в единицу времени и обязательно с ресиверами (хранилищами сжатого воздуха). Подобранный таким образом компрессор опережает по производительности сжатого воздуха потребность выдувной машины и накапливает этот воздух в ресивере, уже из которого он попадает в выдувную машину. В этом режиме работы у компрессора есть возможность время от времени «передохнуть», что хорошо сказывается и на потреблении энергии и на ресурсе техники. Основное применение сжатого воздуха – технологическое: непосредственный выдув изделий, а также поддув рукава до смыкания. Поскольку воздух непосредственно касается пластика, к его качеству предъявляются определённые требования. Самое главное из этих требований и одновременно самое нарушаемое на небрежных производствах – минимизация содержания влаги. Чрезмерное содержание влаги привносит целый ворох негативных технологических эффектов, возникающих в процессе выдува; общий смысл этих эффектов сводится к потере стабильности процесса и качества выпускаемых ёмкостей. Другим пожеланием к качеству воздуха является минимизация содержания масла. Чрезмерное содержание компрессорного масла в сжатом воздухе оказывает некоторое негативное влияние не только на сам технологический процесс, но и на элементы пневматической системы выдувной машины. Для некоторых фармацевтических и/или пищевых производств даже используют более дорогие полностью безмасляные компрессоры, что, впрочем, является требованием/пожеланием конкретного стандарта чистоты отдельно взятого предприятия и не является обязательным для экструзионно-выдувного формования в принципе. Проверенные европейские производители компрессорной техники, такие, например, как Atlas Copco, предлагают к своим компрессорам специальные фильтры отчистки от масла и от влаги. Использование таких дополнительных фильтров гарантирует получение правильного воздуха для стабильного выдувного формования. Охладитель (чиллер) Подавляющее большинство экструзионно-выдувных машин сегодня работают на гидравлических приводах. Гидравлическое масло нагревается в процессе работы, но имеет определённый диапазон температуры, при котором его гидродинамические свойства остаются стабильными, поэтому, естественно, масло требует постоянного охлаждения. Охлаждение масла происходит в маслоохладителе выдувной машины, где поток масла проходит рядом с потоком холодной воды и путём интенсивной теплопередачи – охлаждается. Другой ключевой элемент экструзионно-выдувного процесса, требующий охлаждения – это прессформы. Задача системы охлаждения прессформы – обеспечить максимально быстрое затвердевание изделия после принятия им окончательной формы. Для эффективного решения этой задачи через прессформу в единицу времени нужно пропустить как можно большее количество воды с как можно меньшей температурой. От того насколько хорошо решается эта задача и будет в основном зависеть время цикла, а значит производительность машины. Наконец, охлаждаются в выдувной машине также выдувные дорны, которые непосредственно касаются горячей горловины изделия (и без охлаждения перегреваются и прилипают к горловине) и зона загрузки экструдера. Охлаждение реализуется путём циркуляции воды в замкнутом контуре между машиной и чиллером. Общий смысл системы сводится к тому, что охлаждённая в чиллере вода поступает в машину, где забирает тепло у масла и прессформ, а затем вновь попадает в чиллер, где вновь охлаждается до предыдущей температуры и процесс повторяется. Чиллер обеспечивает охлаждение воды за счёт теплообмена между нагретой водой и хладагентом (например, R407C, низкокипящая жидкость, которая при кипении забирает тепло у воды). При помощи компрессора хладагент циркулирует в замкнутом контуре охладителя, а циркуляция воды между машиной и чиллером обеспечивается насосом охладителя. Как правило, экструзионно-выдувные машины имеют две пары вход-выход. Одна пара ведёт к маслоохладителю, а другая – к гребёнке, распределяющей воду на прессформы, выдувные дорны и зону загрузки экструдера. Перед каждой из прессформ обычно имеется отдельная многоканальная гребёнка, которая разделяет поток воды на количество каналов, соответствующее количеству каналов охлаждения, выполненных в прессформе. Если количество каналов на гребёнке меньше, чем количество каналов в прессформе, то получается, что в единицу времени мы не впрыскиваем в форму максимальное количество воды минимальной температуры, ведь вода в канал охлаждения прессформы, на который не нашлось места в гребёнке, вынуждено попадёт из другого канала прессформы, нагревшись после его прохождения.
|