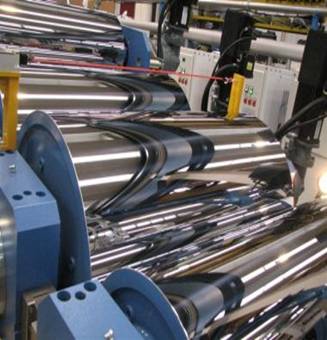
Технология разработана в сотрудничестве с одним из крупнейших итальянских производителей каландровых линий – компанией Comerio Ercole. Суть технологии в практически непрерывном поточном производстве. Из экструдера выдавливается тонкий слой ПВХ, наносимый на разматываемую полиэстеровую сетку. После нанесения, полученный двухслойный материал прокатывается через горячие валы, что придает материалу заданные технические характеристики. Процесс производства такого полуфабриката может длиться в течение недели, после чего двухслойную ткань переворачивают и повторяют процесс для получения трехслойного материала. Схема линии, предложенной компанией B. G. Plast 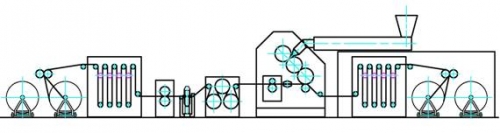
Данная технология применяется для производства так называемых «литых» баннерных тканей. В процессе производства из экструдера выдавливается ПВХ и наносится на разматываемую полиэстеровую сетку. Данный процесс может длиться в течение недели, после чего ПВХ наносят на вторую сторону рулона ткани. Линия включает в себя следующие наименования: 1. Приводного размотчика полиэстеровой сетки – 2 комплекта; 2. Аккумулятора 20 метров полиэстеровой ткани; 3. Платформа для экструдера и системы электрорегулирования; 4. Машины центрирования полиэстеровой сетки перед входом в каландр; 5. Двухшнековый экструдер TB-125-30 с вакуумным насосом для дегазации; 6. Плоская экструзионная головка; 7. 3-валковый каландр производства Comerio Ercole; 8. Машины терморегулирования нагреваемого масла для каландра; 9. Участок охлаждения ткани с 3-мя охлаждающими валами; 10. Измеритель толщины на воздушной подушке; 11. Устройство подрезания краев с 2-мя лезвиями; 12. 2-х позиционная намоточная станция; 13. Система электрорегулирования производства Siemens plc; С анализом рынка баннерных тканей вы можете ознакомиться в исследовании: «Рынок баннерных тканей в России». www.polymery.ru
|