Процесс гомогенизации. Когда сырье прошло стадию сушки, оно поступает через бункер в шнек. Конструкция шнека оптимизирована для получения однородного расплава ПЭТ при температуре 280 – 300 С. Отливка преформ. Полученная в процессе гомогенизации однородная масса поступает в пресс – форму. Здесь происходит непосредственно изготовление преформ. Пресс-форма представляет собой плиту, состоящую, как правило, из двух частей: горячей холодной. Горячая часть содержит каналы, по которым однородная масса ПЭТ поступает в холодную часть. Холодную часть также можно разделить на две части: подвижная и не подвижная. Неподвижная часть – это гнезда, в которые поступает расплавленный ПЭТ. Подвижная – пальцы, которые входят в гнезда и формируют толщину стенки и длину будущей преформы. Охлаждение и выгрузка преформ. Преформу при ее производстве следует охлаждать быстро, так, чтобы ПЭТ не успел закристаллизоваться и затвердел, т.е. перешел в стеклообразное состояние, сохранив аморфную, некристаллическую структуру, которую он имел в расплавленном состоянии. В противном случае, будет невозможно выдуть бутылку из преформы. С точки зрения технологического процесса, охлаждение преформ происходит в холодной части пресс-формы. После охлаждения преформ, происходит их выгрузка. Выгрузка может производиться по-разному. В первом случае, в составе пресс-формы может быть третья часть, прикрепленная к ней перпендикулярно. Сразу после готовности преформ данный робот автоматически подходит и забирает преформы. Такой подход позволяет значительно сократить время цикла, тем самым повысив производительность оборудования. Однако данная технология запатентована и применяется только на оборудовании фирмы Husky. Второй подход, когда готовые преформы сдувают мощным потоком воздуха в некую емкость. Ведущие поставщики оборудования для производства преформ На заре формирования рынка ПЭТ преформ в России, технологические линии не могли быть охарактеризованы как высокопроизводительные. Первая преформа (42 г.) была достаточно тяжелой. Ее производство требовало сравнительно большего времени одного цикла, что не могло не оказывать влияния на производительность в целом. Такая ситуация во многом была вызвана наличием устаревшего оборудования у производителей напитков. Стоявшие на предприятиях полуавтоматы просто не могли выдуть сравнительно качественную бутылку из преформы менее, чем 42 г для бутылки 1,5 л. Переход производителей напитков на современное оборудование, вызвал гонку за повышением производительности со стороны производителей преформ. Рынок требовал инноваций со стороны поставщиков оборудования. Выиграл эту гонку канадсий поставщик – Husky. Доли ведущих поставщиков оборудования для производства преформ в России 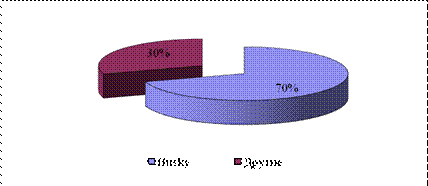
Помимо Husky в числе основных поставщиков оборудования могут быть названы Netstal, Sipa, Engel. Тем не менее, лидеры рынка по-прежнему отдают свое предпочтение Husky, серии HyPet. В России наибольшее распространение получила HyPet 300. Ниже представлены варианты ее использования.
Варианты использования HyPet 300 Варианты | Количество гнезд впрыска | Выход продукции, млн. штук/год | 500 млгазированный напитокгорлышко: 28 мм PCOмасса: 26-29 грамм | 72 | 170,5 | 500 млбутылка для водыгорлышко: 30/25 мммасса: 13-18 грамм | 72 | 285,6 | 500 млготовый к употреблению чай/напитки горячего розливагорлышко: 28 мммасса: 28-32 грамм | 72 | 127,7 | 473 млмолочные продуктыгорлышко: 27-30 мммасса: 28-32 грамм | 72 | 140,3 | 591 млсоки и изотоникигорлышко: 43 мммасса: 26-29 грамм | 48 | 74,8 |
Следует обратить внимание, что помимо представленной системы HyPet 300, компания Husky может предложить системы HyPet 90, 125, 225, 400 и 500, а также Index и Index SB. Однако в России повышенным спросом отличается система HyPET серии 300. Ниже приведен анализ стоимости данной системы для изготовления бутылки 1,5 л общим объемом производства 150 – 200 млн. шт. в год. Пресс-форма – 72 гнезда.
|