Предварительно разрыхленные и смешанные волокна обрабатываются быстровращающимся чесальным барабаном (или несколькими барабанами), отделяются от чесальной гарнитуры с помощью воздушной струи и транспортируются воздушным потоком к месту формирования холста.
Для данного способа характерно следующее: - производство изотропного холста (т. е. без определенной ориентации волокон); - возможность перерабатывать волокна, значительно отличающиеся друг от друга по своим физико-механическим и геометрическим показателям; - производство холстов разного развеса, в т. ч. очень большого, без использования дополнительных устройств; - высокая производительность. Степень ориентации волокна в холсте, полученном аэродинамическим способом, колеблется от 1:1 до 1:3. Холст с развесом до 50 г/м2 из-за небольшой толщины считается двухразмерным (2D) с равномерным расположением волокон на поверхности. Холст с развесом свыше 100 г/м2 отвечает всем требованиям пространственной изотропии (3D). С помощью аэродинамического способа можно выпускать холст с развесом 10–10000 г/м2, но при переработке вторичного текстильного сырья установлено, что технологически и экономически выгодно выпускать среднетяжелый и тяжелый холсты. Недостатком аэродинамического способа является зависимость максимального развеса холста от линейной плотности и вида перерабатываемого волокна. При изготовлении холста с большим развесом из тонкого волокна из-за заполнения отверстий перфорированного барабана (или сетчатого конвейера) увеличивается аэродинамическое сопротивление, и воздушный поток не может полноценно транспортировать волокно. Второй особенностью аэродинамического способа формирования холста, которая сильно проявляется при переработке текстильного вторичного сырья, является разделение смеси на поверхности перфорированной плоскости на компоненты, значительно отличающиеся линейной плотностью. Данная особенность аэродинамического способа формирования холста может быть использована при изготовлении слоистых материалов. Преимуществом аэродинамического способа является хорошая равномерность холста, а также возможность его получения из волокон, переработка которых на чесальных машинах невозможна или невыгодна. В их число входят некоторые твердые и короткие волокна, минеральные волокна, волокна с особо гладкой поверхностью, с очень большой линейной плотностью и с очень высоким содержанием пыли. Холст, полученный аэродинамическим способом, укрепляют с помощью жидких или пенистых склеивающих веществ пропиткой или орошением, а также термопластическим, иглопробивным или (реже) вязально-прошивным способами. Для этого холста характерно то, что он не расслаивается, как это случается с холстом, полученным из слоев прочеса механическим холстообразованием. Холсты, полученные аэродинамическим способом из текстильного вторичного сырья или его смесей с нормальным волокном, могут использоваться для производства подкладочных нетканых материалов, в том числе подкладок для напольных покрытий, масляных прокладок и т. д.; материалов для звуковой, тепло- и гидроизоляции; упаковочных и мебельных материалов; геотекстильных материалов; объемных нетканых материалов, в том числе наполнителей для подушек и спальных мешков, изоляционных прокладок для одежды, материалов для матрацев и т. д. 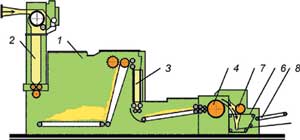
Принцип аэродинамического холстообразования можно рассмотреть на примере агрегата Mat Former французской фирмы Laroche (рис.). Волокна предварительно разрыхляются и перемешиваются в питателе 1 с наклонной игольчатой решеткой, который заполняется бункером 2, оборудованным разрыхляющим барабаном. Далее через бункер 3 материал подается на быстровращающийся расчесывающий барабан 4, находящийся в зоне действия воздушного потока. Частота вращения барабана до 4500 мин-1. Под действием центробежной силы и воздушного потока, создаваемого в транспортирующем канале за счет подсоса из канала 5, волокна отделяются от гарнитуры барабана и транспортируются на поверхность перфорированного барабана или, как в нашем примере, сетчатого конвейера 6, где оседают за счет подсоса воздуха и образуют волокнистый настил. Настил уплотняется барабаном 7 и выводится конвейером 8 из машины. По такому же принципу работают и аэродинамические холстообразователи фирм Curlator Corp, мод. Rando Feeder – Rando Webber, и Proctor Schwarz, мод. Proctor Form (США), DOA мод. 1115-LM (Австрия), Spinbau мод. TurboCard и Hergeth (ФРГ), Bonino (Италия), Gallaghan, мод. 2184MAB (Англия) и др. Компания Dr. Otto Angleitner (DOA) GmbH & Co (Австрия) предлагает холстоформирующую машину, работающую в две стадии: на первой стадии на предварительный прочес наносится порошок термоскрепляющего клеящего вещества, на второй стадии порошок равномерно распределяется внутрь по всему объему холста, развес которого может быть в пределах от 100 до 10000 г/м2. Некоторые рабочие характеристики аэродинамических холстообразователей последних моделей даны в табл. Модель | TurboCard | Bemaformer | - | Mat Former | Feltech | Фирма (страна) | Spinbau (ФРГ) | Bettarini & Serafini (Италия) | Bonino (Италия) | Laroche SA (Франция) | Margassa SL (Испания) | Число чесальных секций | 1 | 1 | до 3 | 1 | 1 | Рабочая ширина, мм | до 6000 | до 3500 | до 4000 | 3900 | до 5000 | Частота вращения расчесывающего барабана, мин.-1 | 4500 | 4000 | 4000 | 4000 | 4000 | Скорость выпуска, м/мин. | до 20 | до 20 | до 20 | 10–15 | до 20 | Развес холста, г/м2 | 50–3500 | 400–4000 | 20–3500 | 30–3000 | 20–3500 | Производительность, кг/ч на 1 м раб. ширины | 500 | 1000 | 450 | 550 | 600 |
|