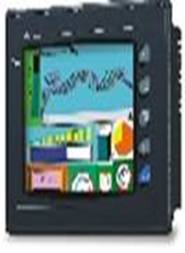
В общем случае изготовление продукции из пластика подразделяется на следующие фазы: загрузка сырья, механическое перемещение шнеком внутри корпуса экструдера с разогревом, плавление и перемешивание сырья до получения рабочей массы, инжекция через фильеру (эксктрузионную головку) с получением изделия нужной формы, охлаждение изделия для получения твердости и выход готового изделия. Каждый из этапов требует поддержания в соответствующей зоне экструдера определенных давления и температуры, а также максимально эффективной выдержки каждого этапа по времени. Для решения данной задачи компания Delta Electronics предлагает комплектный набор оборудования: • программируемый контроллер типа DVPSA или DVPSV с модулями аналоговых входов/выходов DVP-AD/DA для общего управления всеми технологическими процессами; • частотный преобразователь серии VFDG для регулирования оборотов шнека, а соответственно, скорости перемещения материала и рабочего давления в зонах; • модульный термоконтроллер DTC для получения информации и регулирования температуры в каждой зоне (каждый модуль управляет своим нагревателем); • панель оператора для оперативного отображения текущих значений параметров и задания новых. Рассмотрим, как работает система управления.
Программируемый контроллер оперативно получает данные о температуре и давлении в каждой зоне, а также о текущем положении подвижных деталей установки, например при помощи потенциометрических датчиков линейного перемещения. После оперативной обработки данных контроллер корректирует работу исполнительных устройств: приводного двигателя шнека через частотный преобразователь, нагревательных элементов через модульный термоконтроллер, положение задвижек путем подачи сигналов на электромагниты. Оператор контролирует процесс и вводит параметры посредством человеко-машинного интерфейса (панели). Панель оператора также позволяет загружать готовый набор параметров (рецепты) для контроллера под каждый вид продукции, вести архив данных, выводить предупредительные и аварийные сигналы. Для сокращения количества проводов все устройства связаны последовательным каналом передачи данных по RS485 со скоростью 38 400 бит/сек. по протоколу MODBUS. Так как изготовление продукции из пластика связано с достаточно сильным нагревом исходного сырья, а затем охлаждением готового изделия, большую долю в производственных издержках составляет расход электроэнергии. Соответственно экономия электроэнергии является одним из основных путей сокращения издержек. Применение вышеуказанного комплекта оборудования снизит потребление электроэнергии за счет точной дозировки ее подачи в требуемые точки технологической установки. Например, за счет исключения перегревов нагревателей, регулирования скорости вращения шнека путем математической обработки частотным преобразователем VFD¬G входных аналоговых сигналов от контроллера и формирования наиболее оптимальной частоты привода, поддер¬жания наиболее оптимальной консистенции рабочей массы, что снижает сопротивление при ее движении внутри корпуса и через фильеру. Отсутствие перегрева сокращает также расход электроэнергии на охлаждение готового изделия. www.polymery.ru
|