Высокая функциональность однородного плазменного разряда в вакууме заставляла искать способов получения однородного тлеющего разряда при атмосферном давлении, что сделало бы эту технологию применимой для экструзионных процессов при атмосферном давлении. Недавно, компании Enercon Industries и Sigma Technologies International разработали линейный источник излучения, который может давать стабильный тлеющий разряд для Атмосферной плазменной обработки (APT). Отличия от систем обработки коронным разрядом заключаются в следующем: 1. Инжекция плазменного газа в искровой промежуток. Для того, чтобы получить стабильный тлеющий разряд, свободный от стримерных разрядов, необходимо использовать инертные газы, высокие метастабильные фазы которых позволяют создавать устойчивый тлеющий разряд. Для того, чтобы свести потребление этих газов к минимуму, газ впрыскивается непосредственно в искровой промежуток. Такой метод позволяет осуществлять инжекцию и других газов для обработки, которые становятся высоко ионизированными в разряде и позволяют потребителям создавать необходимый химический состав обрабатываемого полимера. 2. Создание стабильного, гомогенного и однородного тлеющего разряда. В отличие от обработки коронным разрядом, где разряд носит стримерный характер, APT создает однородное тление в искровом промежутке. Это позволяет осуществлять однородную обработку поверхности подложки. Таким образом, достигается более высокое качество обработки поверхности. 3. Более низкое напряжение. Напряжение, необходимое для того, чтобы создать газовый разряд, существенно снижено, по сравнению с системами обработки коронным разрядом. Это позволяет избежать обработки обратной стороны, которая является одним из основных недостатков обработки коронным разрядом. ЭКСПЕРИМЕНТ Целью эксперимента стало определение различий в прочности адгезии на раздир для пленки из LDPE, которая рассматривалась в необработанном виде, после обработки коронным разрядом, а также после обработки с помощью технологии APT. Материалы • Толщина 1 мил – 25 микрон LDPE, удлинение в машинном направлении – 330%, удлинение в поперечном направлении – 550%, прочность на разрыв в машинном направлении – 23МПа, прочность на разрыв в поперечном направлении – 19МПа. Оборудование • Система обработки коронным разрядом с металлическими электродами Enercon Covered Roll; • Лабораторная станция для АРТ Enercon/Sigma; • Тестер фрикционного отслаивания поверхности от Thwing-Albert модель 225-1 с тележкой и фиксатором отслаивания. Пленка из LDPE предварительно обрабатывалась в следующих условиях: Таблица 2: Переменные эксперимента. Обработка подложки | Обработка коронным разрядом | Обработка АРТ | Без обработки | Производительность технологической линии | 50 футов в минуту | 50 футов в минуту | - | Искровой промежуток | .040 | .040 | - | Ваттная плотность | 9 | 9 | - | Дина до испытаний | 30 | 30 | 30 | Химический состав АРТ | - | He/C2H2 | - | Начальная дина после испытаний | 46 | 60 | 30 |
Результаты испытания на прочность к отслаиванию измерялись в соответствии с методом испытаний ASTM D3330A при использовании 180-градусного фиксатора отслаивания и акриловой клеящей ленты ацетатной пленки 3M 800. РЕЗУЛЬТАТЫ Испытания на прочность к отслаиванию осуществлялись со сроками предварительной обработки от тридцати минут до семнадцати дней для определения прочности поверхностного покрытия к отслаиванию и долговечности покрытия. Продолжительность обработки и статистические данные для средних значений адгезии поверхностного покрытия даны в общем виде на рисунках 1 и 2 соответственно. Рисунок 1. Продолжительность обработки LDPE в динах на см. на протяжении 17-дневного периода. 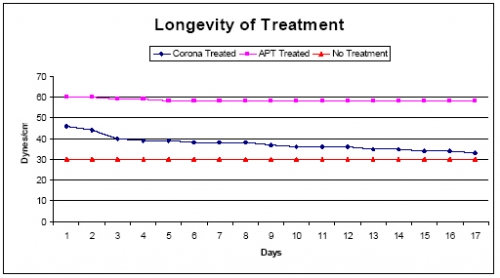
Рисунок 2. Средние значения прочности к отслаиванию LDPE в фунтах на дюйм на протяжении 17-дневного периода. 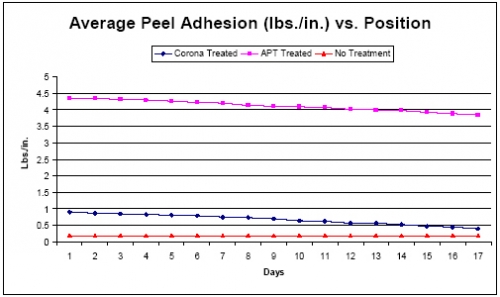
|