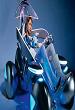
Дороговизна нефтяного сырья и полимеров, а также прогресс в сферах биотехнологии, нанотехнологии, экологической химии и науки о материалах задают быстрый темп восстановлению производства пластмасс и тканей, основанных на натуральных веществах. Генри Форд еще в тридцатых годах 20 века использовал соевые бобы для производства красок, эмалей и деталей из литой пластмассы для своих автомобилей Model T. Из пластмасс на растительной основе изготавливали крышки бардачка, рычаги переключения передач, кнопки звукового сигнала, педали газа, распределительные головки, элементы внутренней отделки, рулевые колеса, приборные панели и отделка корпуса. Волокна из конопли, древесной массы, хлопка, льна и китайской крапивы использовались в качестве наполнителей и для придания жесткости материалу. Детали на основе пластмасс из нефтяного сырья, которые со временем становились все более дешевыми и качественными, постепенно занимали прочное место в автопромышленности. В настоящее время автомобильные компании стараются вернуть пластмассы растительного происхождения в активное использование, чтобы снизить свою зависимость от иностранной нефти и уменьшить ущерб, наносимый экологии. Были разработаны пластмассы из натуральных материалов с более высоким качеством поверхности, более крепкие и жаропрочные, которые можно использовать для изготовления внутренних деталей транспортных средств. Совместный японский проект, объединивший автоиндустрию, правительство и ученых, при участии корпорации Mazda, продемонстрировал один из таких материалов. Предназначенная главным образом для автомобильного сектора, эта биопластмасса сделана из природных материалов. Она углеводо-нейтральна за счет сниженного количества ископаемых веществ, необходимых для ее производства, благодаря чему выделение углекислого газа также уменьшается. Биопластмасса изготовлена из 88% кукурузного сырья и 12% — нефтяного. Она крепче своих конкурентов: ударное сопротивление выше в 3 раза, а жаропрочность на 25% превышает современные биопластмассы, используемые для электроприборов. Кроме того, технический процесс ее изготовления основан на ферментации натуральных крахмалов и сахаров, за счет чего потребление энергии снижается на 30% по сравнению с производством полипропилена. В отличие от современных полипропиленов, новая биопластмасса обладает большей жесткостью, что позволяет делать более тонкие детали и экономить на материале. Эти свойства будут крайне полезны для повышения продуктивности массового производства деталей автомобилей, в ходе которого часто используется оборудование для опрессовки под давлением. Производители биопластмассы — Nishikawa Rubber Co. Ltd и университеты Хиросимы и Кинки — сосредоточили усилия на разработке нового вещества, которое бы позволило повысить жесткость и жаропрочность их продукта, в результате чего возможная сфера применения могла бы значительно расшириться. Ведется разработка автомобильной пластмассы, не содержащей нефтяного сырья, чтобы сделать автомобили полностью перерабатываемыми. Исследователи компании Ford работают над этой идеей, поставив себе главной задачей разложение пластмассы. Другие проблемы, которые эта команда должна преодолеть, — это снижение поглощения влаги (так как пластмассы на основе природных волокон сильнее впитывают жидкость, что приводит к снижению прочности) и проблема запаха. 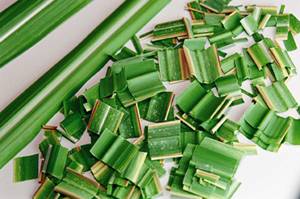
Хотя эти задачи еще не решены, материалы, основанные на природном или переработанном сырье, уже сейчас используются в некоторых автомобилях Ford: |