Система гравиметрического контроля (СГК) От проектирования СИСТЕМЫ ГРАВИМЕТРИЧЕСКОГО КОНТРОЛЯ (СГК) зависит точность смешения компонентов в рецептурах и стабильность работы линии в целом. СГК отслеживает расход сырья (поток массы кг/м) в режиме реального времени и сравнивает этот показатель со скоростью тянущего устройства (м/мин). При отклонении фактического метрического веса от заданного расчетного. СГК корректирует параметр до установленного значения. В соответствии с технологией производства, устройства и программное обеспечение СГК, поставляются для отслеживания одного или нескольких потоков сырья на выбор заказчика. Количество компонентов/потоков сырья может быть увеличено уже в процессе эксплуатации оборудования. Базовая система гравиметрического контроля включает в себя: • Загрузочную воронку • Весовую воронку из оргстекла • Дозирующий клапан и раму • ПЛК с интерфейсом • Измерение скорости линии с замкнутой системой управления • Измерение скорости вращения шнека • Измерение производительности шнека за один оборот (гр/об.) • Интерфейс для управления более высоким уровнем • Принтер СИСТЕМА ПОДАЧИ СЫРЬЯ 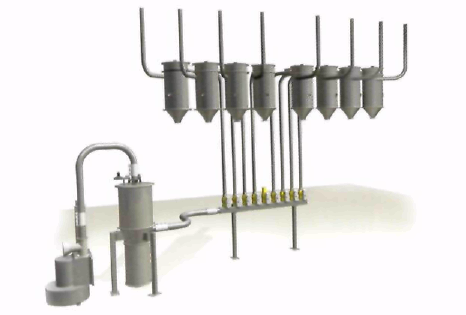
Система подачи сырья обеспечивает автоматизированную транспортировку сырья от склада/силосов до дневных силосов или непосредственно в дозирующие станции линии, а также автоматизированный учет расхода сырья, когда при достижении определенного уровня компонента в силосах направляется запрос поставщику на отгрузку нового объема сырья. Также система включает вакуумный насос и фильтрующую систему для удаления нитей, волокон и полимерной пыли. Подача добавок осуществляется тоже централизованной станцией. Для чувствительных к влаге видов сырья, таких как РА, PET, EVOH «EXTROY» проектирует системы сушки сырья в линии, непосредственно перед загрузкой его в экструдер. 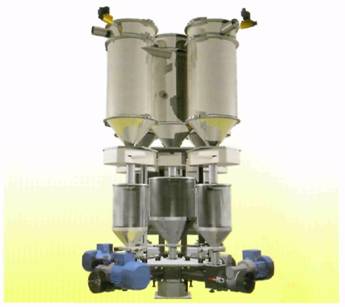
Для того, чтобы гранулы каждого компонента сырья поступали в станции дозирования без перебоев и синхронизировано с работой линии, оптимизируется длина и диаметр трубопроводов; осуществляется подбор мощности насосов; используется система прочистки, продува трубопроводов после смены сырья при помощи клапанов; осуществляется координация времени ожидания при смене компонентов загрузки. Все это снижает лишние издержки в обслуживании основного и вспомогательного оборудования: освобождает время операторов соэкструзионной линии на основную высокоинтеллектуальную работу по управлению технологическими параметрами и контролю за качеством продукции, практически, исключая физический труд по подготовке, растарке, расчетам расхода сырья, способствует значительному повышению производительности за счет автоматизации. Устройства поверхностной обработки пленки Оптимальные устройства короной обработки и их характеристики подбираются под производимые типы пленок: • С уровнем поверхностной обработки от 38 до 54 дин Изготовленные полностью из нержавеющей стали • Анодированные алюминиевые рамы и крепления Сегментные электроды позволяют выбирать ширину электродов в соответствии с шириной пленки или производить выборочную активацию пленки • Автоматическое открытие/закрытие электродов воздушными клапанами • Алюминиевые или стальные валы коронатора для различных диаметров, с внешними подшипниками для защиты их от озона • Три варианта изоляционного покрытия валов коронатора: керамическое, с силиконовыми рукавами, с вулканизированными силиконовыми рукавами. • Вентилятор откачки озона используется для охлаждения электродов и поддержания их температуры в эффективном диапазоне. • Возможность обработки уже разделенного полотна пленки с одной или двух сторон • Возможно принудительное охлаждение вала коронатора • Безопасность эксплуатации Тянущее устройство 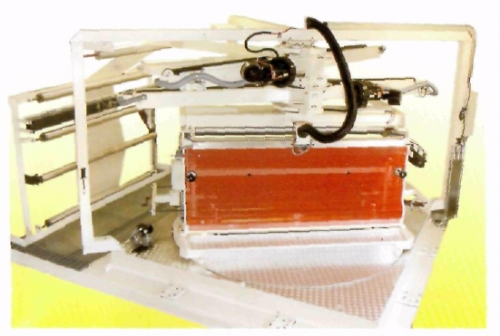
|