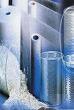
Наибольшее практическое применение находят следующие способы производства изделий из армированных пластиков: - контактное формование с укладкой пропитанного смолой волокнистого холста на форму; - напыление волокнисто-полимерной композиции на поверхность формы; - различные способы формования в закрытой форме; - намотка пропитанного смолой волокна на форму; - пултрузия, или формование профильных изделий путем протяжки волокна через ванну с полимером и калибрующую фильеру. В зависимости от технологии формования значения свойств полимерных композитов могут отличаться в несколько раз. Выбор технологии зависит от конструкции изделия, условий его эксплуатации, объема изготовления и имеющихся производственных ресурсов. Неправильная организация техпроцесса, неудовлетворительная подготовка исходных компонентов, несоблюдение технологических режимов (давления прессования, продолжительности и температуры процесса, предписаний по подготовке сырья и материалов) и многие другие причины могут значительно изменять свойства готовых изделий. Поэтому очень важно не только грамотно, с учетом конструкции и условий эксплуатации изделий, построить технологический процесс, но и при его реализации четко соблюдать технологические режимы. С этой целью необходимо на всех стадиях процесса осуществлять текущий контроль технологических параметров и свойств изготавливаемого изделия. Для изготовления небольших серий крупногабаритных изделий сложной геометрической формы применяют послойную укладку ламината, используя в качестве связующего смолы холодного отверждения (эпоксидные, полиэфирные и др.). Эта технология называется контактным формованием (рис. 1). 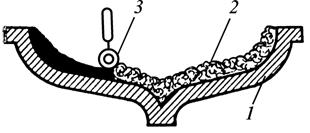
Рис. 1. Схема контактного формования: 1 - форма; 2 - ламинат; 3 - прикаточный ролик При таком способе ламинат 2, представляющий собой армирующий материал, пропитанный полимерной композицией, укладывается на специальную негативную форму 1 (матрицу), затем тщательно прикатывается валиком 3 с целью уплотнения и удаления пузырьков воздуха, после чего полимерная композиция отверждается. Поверхность готового изделия является зеркальным отражением поверхности использованной формы и полностью воспроизводит ее фактуру. При больших толщинах будущего изделия из стеклопластика нанесение ламината проводят в несколько стадий, давая возможность каждому слою отвердиться и охладиться. Это связано с тем, что отверждение смолы происходит с выделением значительного количества тепла (рис. 2). В результате происходит перегрев отверждающейся композиции, появляются значительные внутренние напряжения, приводящие к деформациям, короблению и растрескиванию готовых изделий. 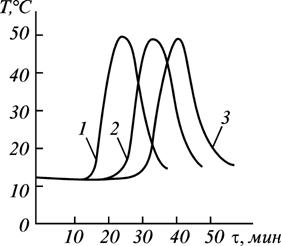
Рис. 2. Влияние продолжительности полимеризации (t) смолы с коротким (1), средним (2) и большим (3) временем гелеобразования на температуру ламината В последние годы получил развитие способ изготовления крупногабаритных изделий из стеклопластика путем напыления на формообразующую оснастку композиции, содержащей связующее (полиэфирную смолу и катализатор отверждения) и рубленое стекловолокно (рис. 3). 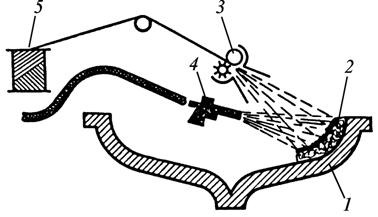
Рис. 3. Схема производства изделий из стеклопластика методом напыления: 1 - форма; 2 - ламинат; 3 - режущее устройство; 4 - напылительный пистолет; 5 - бобина ровинга
|