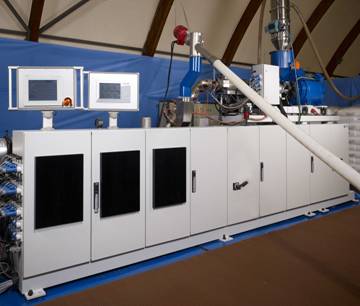
Пожалуй, самое интересное технологическое новшество в экструзии древесно пластиковых (ДП) профилей - устранение этапа промежуточного приготовления древесно-полимерной композиции с ее дальнейшей грануляцией через экструзионную грануляционную линию. Таким образом снижается себестоимость данных профилей, сокращается количество минимально необходимого оборудования для начала производства и, следовательно, данный бизнес можно считать более доступным. Особенно интересен может быть путь использования рециклята муниципальных пластиковых отходов и отходов производств деревообработки, бумажно-целлюлозной, текстильной промышленности, отходов переработки некоторых растительных сельхозкультур, некоторых отходов мясо-молочной промышленности (для экструзии профилей по технологии «Fasalex»). Задача выработки рециклята из пластиковых отходов в наших условиях весьма сложна: сбор, сортировка, чистка, дробление, агломерирование и пр. – но, в принципе, выполнима, что доказывает опыт успешной работы нескольких фирм в Швеции по переработке пластикового рециклята и отходов деревообработки в ДП профили различного строительного назначения. Такие линии «прямой экструзии» разработала фирма «Reifenhauser»: его основа – двухшнековый экструдер c встречновращающимися шнеками, шнеки – 75 мм., L/D – 30. В его задней части расположен одношнековый питатель (диаметр шнека 50 мм.) с прямым приводом вала этого шнека. Данный узел служит для предварительной пластикации связующего полимера – из гранул в расплав при температуре + 180 ºС. Далее данный расплав поступает в основной рабочий цилиндр экструдера и продвигается шнеками к выходной профильной экструзионной фильере. При этом, конечно, данный цилиндр имеет свои режимы нагрева и охлаждения зон, темперирования шнеков и их скорости вращения, определяемые технологией переработки. Древесный наполнитель и прочие аддитивы поступают в основной цилиндр экструдера через многокомпонентный гравиметрический дозатор. В дозатор данные компоненты поступают из обычных емкостей или даже из биг-бегов и из прочей отпускной товарной упаковки с помощью вакуум загрузчиков, работу которых – периодичность и продолжительность включения, в зависимости от программируемого расхода контролирует PLC. Формующие инструменты спроектированы и изготовлены, таким образом, что позволяют экструдировать ДП профили с довольно высокими скоростями (до 2-3 м/мин), по сравнению со скоростями по предыдущей технологии. Даунстрим – обычный для профильной линии, плюс на калибрационном столе – охлаждающая оросительная ванна и щёточная очистка профиля. Такая линия в Латвии уже успешно производит ДП декинговые профили и ДП подоконники Впрочем, «Reifenhauser», не монополист в этой области. «ICMA San Giorgio» (Италия) предлагает аналогичные линии «прямой экструзии» ДП профилей с содержанием древесного наполнителя до 70%. Дополнительное преимущество данной технологии заключается в том, что предварительная пластикация термопласта при такой высокой температуре перед подачей в основной цилиндр экструдера позволяет значительно быстрее избавиться от влаги в древесном наполнителе, что значительно улучшает качество профилей. Американские производители ДП профилей обычно не превышают содержание древесного наполнителя в профилях более 50 % , в отличие от европейских с их долей до 60 – 80 %. Правда, при этом межремонтный период шнеков сокращается до 6 000 – 8 000 рабочих часов. Но применение метода горячей изостатической обработки шнеков и цилиндров таких экструдеров, разработанного немецкой металлургической фирмой «Reloy», увеличивает этот период до 25 000 часов. Наряду с развитой технологией экструзии древесно – полимерных профилей на основе композиции, состоящей из древесного наполнителя, других аддитивов и связующего термопласта, некоторые производители начали в качестве связующего успешно использовать реактопласты. «Wood K Plus» и «Borealis» разработали новую композицию на основе меламин – формальдегидной смолы - «HipeResin» (high performance resin) , которая позволяет экструдировать древесно-полимерные профили с улучшенными физико-механическими свойствами по сравнению с такими же профилями из древесно – полимерных композиций (ДПК), где связующими являются термопласты. “HipeResin” с добавлением некоторых процессинговых аддитивов и смазок при экструзии имеет реологию, аналогичную реологии термопластов. Данный состав в смеси с древесными наполнителями назван разработчиками «HiperWood» и его возможно экструдировать на обычных экструзионных линиях для термопластов. Данное меламиновое связующее лучше взаимодействует с древесными волокнами при переработке по сравнению с термопластами. Обычно для получения качественного ДПК на основе термопластов древесные волокна необходимо подвергнуть ацетилированию. Меламиновая композиция для достижения сходных и лучших характеристик этого не требует. Меламин более совместим с целлюлозой и не нуждается в дополнительных связующих агентах для лучшего взаимодействия с древесными волокнами. Вследствие этого данная древесно – меламиновая композиция имеет большую огнестойкость, большее сопротивление термодеструкции, профили из неё имеют повышенную прочностные характеристики и большую устойчивость к ползучести. Из данного состава уже успешно экструдируются пустотные декинговые профили, имеющие толщину стенок 2 – 2,5 мм. и вес погонного метра 1,5 кг.. Прочностные характеристики данных древесно – меламиновых профилей сходны с аналогичным профилям из древесно – полипропиленового состава. Австрийскими учеными из Института Агробиотехнологии разработаны полимерные составы, в которых наполнителем является бумага или отходы бумажного производства – так называемые РРС – бумажно - пластиковые композиции (БПК). Ранее этот институт разработал и довел до промышленного применения в экструзии различных профилей ДПК со связующими полимерами животного и древесного происхождения – казеин, лигнин и пр. – по технологии «Fasalex» - «жидкое дерево». |