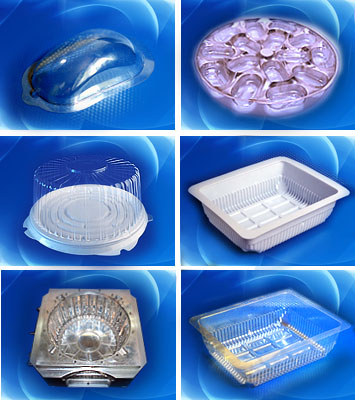
Методом плоской экструзии возможно произвести пленку из любых материалов, используемых для изготовления ленты для термоформования (ПП, ПС, ПЭТ, ПВХ), однако, в большинстве случаев таким способом изготавливаются пленки из полиэтилентерефталата, полистирола и полипропилена. Что касается ПВХ пленок для этих же целей, то они, как правило, изготавливаются посредством каландрования Производство пленок методом каландрирования Каландрованием перерабатывается ПВХ. Теоретически получить пленку ПВХ можно и экструзией, однако, ПВХ очень капризный материал. Существует большая разница между подготовкой ПЭТ, ПП, ПС и ПВХ к расплаву. В процессе смешивания и перемалывания ПВХ композиции ей нельзя передавать чересчур большую энергию, как это происходит в экструдере, например, с полиэтилентерефталатом, иначе произойдет деструкция сырья (точка разложения ПВХ близка к температуре, необходимой для нормального течения экструзии). Поэтому в процессе каландрования отсутствует экструзия, как таковая. В данном случае непрерывный лист или пленку получают пропусканием размягченного материала между двумя или более валками. Каландрование заключается в заливке пластичной массы в щель между двумя валками, где она формуется в пленку, кото¬рая затем проходит через остальные валки. Материал выходит в виде непрерывной пленки, толщину которой определяет зазор между последней парой валков. Поверхность пленки зависит от поверхности последнего валка и может быть блестящей, матовой или структурированной. После выхода из каландра лист охлаж¬дается на охлаждающих валках и проходит через /3-радиоактивный толщиномер до подачи на намотку. Пластичная смесь, подаваемая в каландр, может быть просто расплавом полимера (как в случае, например, с ПЭ); в случае ПВХ проводят большие подготовительные работы по составлению композиции, смешению, желатинизации, фильтрации. Кроме полимера вводят инертные минеральные наполнители (для снижения стоимости и модификации физических свойств), пигменты, технологические смазки, стабилизаторы и пластификаторы. Сухие компоненты, кроме пигментов, загружают в ленточный смеситель и интен¬сивно перемешивают для получения равномерной дисперсии. При получении дисперсной смеси требуемого качества смесь выгружают через клапан в днище смесительной камеры и взвешивают в порционной емкости. Если требуются пигменты, их вводят на этой стадии в каждую емкость отдельно. Эти емкости затем разгружают в первичный смеситель типа «Бэнбери» и пе¬ремешивают при 120-160 °С. Сочетание нагрева и смешения (смеситель типа «кокнетер») вызывает частичную желатинизацию смеси. Частично желатинизированный материал подают в двухвалковую мельницу, где он образует лист вокруг переднего вала. Его можно подавать не¬посредственно в каландр, но для пленок и тонких листов до¬полнительно вводят стренинг-процесс для удаления любых гру¬бых частиц. Типичный стренер состоит из одношнекового экструдера с фильтром непосредственно после шнека. Фильтр со¬стоит из тонких сеток, изготовленных из нержавеющей стали, механически опирающихся на более редкую грубую сетку и ре¬шетник. Каландр может содержать от двух до пяти полых валков, снабженных паровым обогревом или водяным охлаждением, и ха¬рактеризуется числом валков и их расположением, например I, Z, Г (наиболее типичное - Z или Г). К валкам необходимо под¬водить очень большие усилия для формования полимера в тонкую пленку, что вызывает изгиб валков и получение листа, который толще в середине, чем по краям. Некоторые способы борьбы с этим эффектом перечислены ниже: 1) валки могут быть бомбированы, т. е. их диаметр в центре больше, чем по краям; 2) валки могут быть слегка перекрещены, что увеличивает зазор по краям валков; 3) изгибающий момент может быть при¬ложен к концам каждого валка установкой вторых подшипников на каждую щеку вала и их нагружением гидравлическими ци¬линдрами. Каландры типа Z имеют в этом отношении преиму¬щества, потому что прогиб валка не влияет на щель, и, таким образом, разнотолщинность уменьшается. Это происходит пото¬му, что противолежащие валки расположены под прямым углом, а не в линию.
|