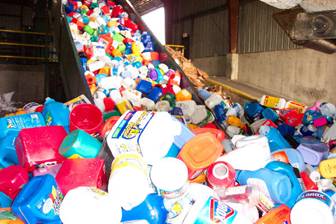
Для выпуска высококачественных изделий и минимализации брака при литье под давлением в ходе производственного процесса следует применять методы контроля свойств отливок. Контроль также связан с внушительными затратами и необходимостью проведения различных испытаний в лабораторных условиях, по результатам которых можно до определенной степени корректировать процесс литья. Во время пускового периода достаточно сложно добиться заданного уровня качества, тем временем пусковой период машины может длиться до нескольких часов. Получается, что в течение этого времени оборудование выпускает брак, а квалифицированный персонал занят корректировкой параметров процесса. Для того чтобы можно было сократить проверки, оказывающие поддержание заданного качества отливки, необходим контроль и регулировка именно тех параметров, которые и определяют свойства отливки и поддаются изменению в процессе хода машины. Многочисленные исследования показывают, что непосредственное влияние оказывают:
• температура расплава в зоне перед шнеком • температура стенки формы • скорость впрыска • давление в форме • деформация и герметичность формы Все вышеперечисленные параметры достаточно легко поддаются корректировке. Для их стабилизации существуют два способа: поддержание вторичных параметров, оказывающих на них воздействие и прямые регулировки. Например, температура расплава в зоне перед шнеком: данный параметр в первую очередь определяют колебания температуры расплава в форме, скорость охлаждения и динамические и статические потери давления. Именно изменение потерь давления и оказывает особо сильное влияние на воспроизводимость качества отливки. Специалисты советуют для поддержания постоянного уровня температуры расплава перед шнеком требуется: точная настройка регулятора температуры стенки цилиндра, неизменность частоты вращения шнека, скоростного напора и длительности пластикации. www.promlitie.ru |