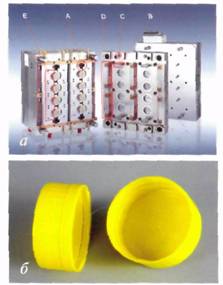
Тот факт, что существенный потенциал решения этой задачи кроется в оптимальной конструкции и рациональном исполнении литьевой формы, лишний раз (но убедительно) доказала фирма Taiwan Mold Tool Co., Ltd., которая получила заказ от крупного мирового производителя упаковки на разработку и изготовление многогнездной литьевой формы (см, фото, а) для производства крышек (см. фото, б) 5-галлонных бутылей (22,7л) на литьевой машине фирм ы Arburg( Германия) с усилием смыкания 3000 кН. Главное требование заказчика заключалось в том, чтобы время цикла литья указанных деталей не превышало 16 с (например, время цикла для литьевой формы, изготовленной другой фирмой для производства таких же крышек, составляло 20 - 22 с). Основным путем достижения этой цели было выбрано сокращение времени охлаждения отливок за счет более эффективного теплообмена между расплавом ПМ и поверхностью оформляющих гнезд. С этой целью для изготовления формообразующих детали был и выбраны марки сталей с высокой теплопроводностью (производитель - фирма Uddeholm, Швеция) и оптимизирована система охлаждения формы. Кроме того, специалисты фирмы Taiwan Mold Tool предложили заказчику наиболее привлека¬тельные по соотношению «цена/качество» сплавы для элементов литьевой формы от ведущих мировых произ-водителей: для основных плит - от Thyssen (Германия), для направляющих деталей - от Daido (Япония), для направляющих и покрытий плит - от DME (Бельгия). Для подачи расплава ПМ в оформляющие полости было решено использовать горячеканальную систему (ГКС) от компании Synventive. Технические условия на детали - от компании HASCO (Германия). Плавная работа системы выталкивания обеспечивалась четырьмя газовыми пружинами от фирмы Azol-Gas (Испания), а также механизмом подачи сжатого воздуха, который был размещен внутри формы. Форма работает следующим образом (см. фото). При закрытии литьевой формы: 4 толкателя (В) входят в 4 фиксатора (А): 3 упора блока шиберов (D) толкают 2 шибера (Е), которые закрывают 8 вкладышей оформляющих гнезд; расплав ПМ впрыскивается в литьевую форму. При открытии литьевой формы; 4 газовые пружины (С) толкают верхнюю и нижнюю пластины системы выталкивания от оформляющего гнезда, чтобы в первую очередь освободить плоскость разъема; 4 толкателя (В) выталкивают 2 шибера (Е) из 8 вкладышей до тех пор, пока они не закрепятся фиксаторами шиберов. Затем крышки выталкиваются в два этапа с помощью выталкивающих плит. Восьмигнеадная литьевая форма (а) для изготовления крышек (б) из ПЭВП или ПЭН П для 5-галлонных бутылей Время проектирования формы было сведено к минимуму, прежде всего благодаря компьютерному моделированию с использованием геометрической ЗВ-модели крышки. Заказчик был полностью удовлетворен предложенной конструкцией формы, выбранными материалами, позволившими сэкономить средства при требуемых функциональных возможностях, и дал «добро» на изготовление литьевой формы. Фирма Taiwan Mold Tool изготовила разработанную 8-гнездную литьевую форму всего за семь недель и затем провела ее испытания, чтобы убедиться в ее надежной работе, надлежащем качестве крышек и надежном срабатывании кольца безопасности крышки при ее откручивании. Во время литьевых испытаний формы был снят видеофильм о шести полных циклах литья, который показывал функционирование движущихся деталей, открытие и закрытие формы, автоматическое перемещение выталкивателей. Кроме того, на экране можно было увидеть отдельные конструктивные и оформительские элементы формы: гравировки, литниковую систему, ГКС, вентиляционные отверстия, фитинги системы охлажления и др. После завершения испытаний литья заказчику был и с курьерской связью направлены образны полученных крышек, а также (по электронной почте) следующие файлы: видеофильм о работе формы, сведения о режиме литья, чертежи формы, план будущих работ и предложения. После положительного ответа от заказчика (е некоторыми пожеланиями) были проведены и задокументированы в виде видеофильма окончательные испытания формы и осуществлена (за 15 дней) окончательная доработка литьевой формы, которая полностью удовлетворила заказчика. Он попросил поставить ему изготовленную форму и сопутствующую документацию, куда вошли: CD с чертежами формы и ЗD-моделью изделия, распечатанные чертежи формы, сертификаты на сталь и ее термообработку, сведения об окончательных параметрах литья под давлением и др. Масса 8-гнездной формы для литья под давлением указанных крышек составила 1,25 т, время цикла, как и требовалось, — 16 с. www.newchemistry.ru |