Для сравнения рассмотрим весы для ПВХ (без силосов) и автоматизацию загрузки мела и диоксида титана (ТiO2) в биг-бегах, а также шести других добавок, таких как стабилизаторы и модификаторы из мешков и биг-бегов. Добавка пигментов в этом сравнении не учитывается. Транспортировка снизу на уровень загрузки (рис.1) осуществляется в мешках и биг-бегах, как с 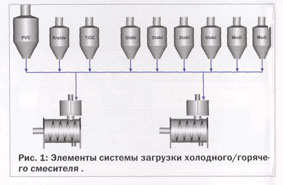 помощью грузового подъемника, так и пневмотранспортом. В обоих случаях необходим подготовительный бункер для каждого компонента над смесителем. Бункеры не влияют на величину издержек, поскольку разгрузчик и загрузочная воронка имеют общий корпус, фильтр, разгрузочный узел, а также шнековый дозатор с запорным клапаном (рис. 2). 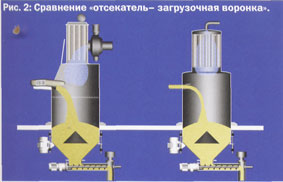
Пример 1: загрузка продукта сверху, подача в смесители отводными трубами (требуется повышенная высота здания). ПВХ подается из силоса на весы. Остальные исходные материалы, такие как мел, ТiO2, стабилизаторы и модификаторы подаются наверх в оригинальной таре, в мешках или биг-бегах, с помощью грузового подъемника и высыпаются в подготовительный бункер (рис. 3). Загрузку в обе
мешалки осуществляет только одно дозирующее и взвешивающее устройство, состоящее из общих весов для ПВХ, общих весов для мела и ТiO2, и весов для добавок (фото 1). С точки 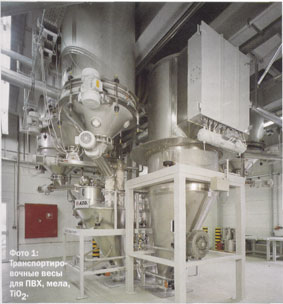 зрения промышленного оборудования это выгодное по цене исполнение, при условии, что в обеих мешалках производится один и то же продукт. Расходы в этом случае зависят от высоты сооружения. Это не является проблемой в уже имеющемся здании, однако в строящемся здании никто не захочет вкладывать средства в дополнительные 3-5 метров высоты. Другой проблемой являются слишком длинные отводные трубы. Даже если они изготовлены из резины, нет полной гарантии, что они полностью опорожняются после каждой партии. Ведь если в смеситель попадает не весь материал, теряется смысл в точном взвешивании. Пример 2: загрузка продукта сверху, распределение в смесители посредством передвижных весов (здание имеет меньшую высоту). Исполнение аналогично описанному выше, однако без пневмотранспорта, но с загрузочными воронками в качестве подготовительных бункеров. Исходные материалы подаются наверх посредством грузового подъемника, а затем загружаются в подготовительный бункер. Воронки расположены линейно в один или два ряда, обеспечивая простоту загрузки. ПВХ из силоса подается непосредственно на двое всасывающих весов (рис. 4 , фото 2). 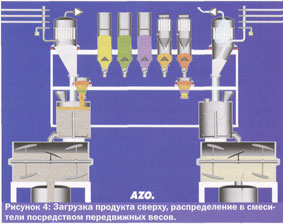 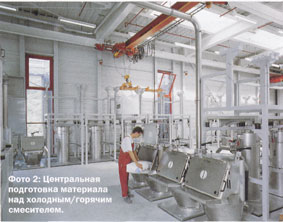
Под бункерами располагается линейно движущееся устройство с двумя весами, которые перемещаются независимо друг от друга, взвешивают и собирают исходные материалы в соответствии с рецептурой. Каждые из весов принадлежат к определённой линии для смешивания, что позволяет избежать смешивания компонентов, относящихся к раз личным составам. Кроме того, каждый подготовительный бункер используется только один раз, т.к. обое весов имеют доступ к каждому из бункеров. Ещё одним преимуществом этой установки является то, что весы могут располагаться непосредственно над смесителями, так что необходимы лишь короткие вертикальные отводные трубы, по которым даже самые тяжёлые компоненты проходят без остатка. Поскольку на таких весах наряду с большими количествами (например, мел) взвешиваются и очень малые количества добавок, они могут быть дополнительно оснащены весами для взвешивания последних. При этом речь идет о весах с опрокидывающейся платформой с диапазоном взвешивания до 1, 3 или 5 кг в зависимости от требований. Достигаемая точность измерения составляет от ±1 до ± 5 г. Весы с опрокидывающейся платформой расположены таким образом, что дозирование из каждого бункера может осуществлять либо на большие, либо на весы для малых количеств. Последние разгружаются затем на большие весы, так что в конце концов в смеситель загружаются все продукты. Таким образом, малые количества соединяются с большими без потерь (рис. 5). 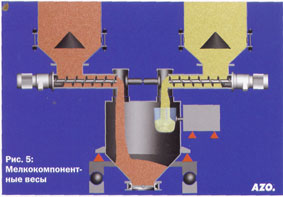
Пример 3: загрузка продукта снизу с пневматической транспортировкой наверх (уменьшенная высота здания). Дозирование и взвешивание осуществляется также, как и в представленном выше исполнении или неподвижными весами для каждого смесителя. Но исходные материалы не высыпаются вниз, а пневматически подаются наверх. Находящиеся на нижнем этаже загрузочные воронки могут располагаться на складе материалов, т.к. могут преодолеваться длинные транспортные пути. При этом большим преимуществом является то, что мешки не попадают в производственную зону. Это позволяет защитить установку от пыли, т.к. основным источником загрязнения являются пустые мешки. Транспортировка может осуществляться посредством всасывающей или нагнетательной пневматики. Как правило, предпочтение отдаётся нагнетательной транспортировке. При этом может осуществляться подача в бункер, из которого в это же время осуществляется дозирование (рис. 6). 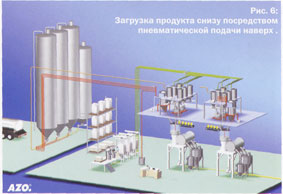 Но может возникнуть проблема, связанная с противовзрывной защитой. Существуют исходные материалы, в частности модификаторы, требующие защиты от взрыва в соответствии с VDI 2263. Если энергия воспламенения продукта < 10 мДж, а показатель KST > 200, то закон предписывает обеспечение конструктивной защиты от взрыва, Это указано в спецификациях продукта, предоставляемых поставщиком. В таком случае подготовительный бункер должен быть оснащен либо предохранительной мембраной, либо быть устойчивым к ударной волне. Кроме того, необходимы быстродействующие заслонки и шлюз на выходе, препятствующие распространению взрыва на другие приборы или помещения. Пример 4: взвешивание сверху, транспортировка наверх предварительно взвешенных партий Все приемные бункеры, устройства загрузки мешков или станции биг-бегов находятся на нижнем этаже, загрузка в них осуществляется напрямую. Чтобы система не становилась слишком дорогой, для одной или двух линий смешивания предусмотрена только одна система взвешивания. При этом смесители должны использоваться поочередно, что, однако, не влияет на число партий. Обе линии должны производить один и тот же продукт. Партии компонентов взвешиваются поочерёдно для каждой из двух линий. Поскольку число тактов очень высокое и составляет 12-16 партий/час, необходимо двое или даже трое весов, в зависимости от требуемого количества сырья. Четыре компонента, подлежащие взвешиванию при 15 партиях в час, делают необходимыми 60 взвешиваний В час. Если вычесть время на разгрузку весов, составляющее 1 минуту на партию, остается 45 минут на 60 взвешиваний, т.е. 45 секунд на 1 взвешивание. Кроме того, загрузка компонентов в смеситель может осуществляться в различной последовательности. При одновременном дозировании мелкие компоненты могут также подаваться на весы для ПВХ и выгружаться вместе с остальными. На рис. 7 представлено решение с одними весами для ПВХ, одними для мела и ТiO2 и одними для остальных добавок. С помощью этой системы можно сначала дозировать ПВХ, затем добавки, а в конце - мел и ТiO2. Пример 5: Дозирующий бункер со взвешиванием сверху; стандартизированный бункер (дозирующий бункер со встроенным дозирующим устройством). 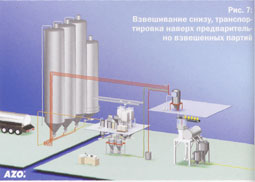 Значительную часть цены составляет стоимость подготовительных бункеров. Каждая фирма имеет другое исполнение или иные размеры. Лишь немногие установки могут использовать бункеры, аналогичные, находящимся в составе других линий, хотя это и сулит значительную экономию средств (рис. 8). 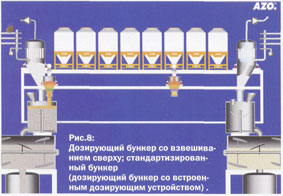 Между тем, существуют решения для дозирующих бункеров, такие, как, например, DosiBox®, стоимость которого составляет лишь малую часть стоимости обычного приемного бункера. Стоимость воронок или приемников составляет приблизительно 15 - 20 тыс. евро за штуку. DosiBox® из полиэтилена с объемом 1000 литров и встроенным шнековым дозатором стоит около 2 тыс. евро, т.е. вместо одного традиционного бункера можно приобрести 10 стандартных DosiBox® (фото 3). 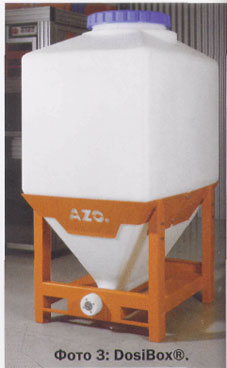 Двое подвижных весов с грузозахватным приспособлением управляют соответствующим бункером, открывают заслонку и вращают шнек до выгрузки требуемого количества. Затем они перемещаются к следующему бункеру. Все компоненты собираются и выгружаются в смеситель в соответствии с рецептом. Пустой бункер извлекается и снова наполняется на складе сырья, или лучше всего, непосредственно у поставщика. Целесообразно иметь два бункера для каждого компонента, это дает возможность работать со вторым во время наполнения первого. При загрузке или после нее бункер взвешивается, характеристики продукта и масса регистрируются системой управления. После фиксирования весами каждого извлечения, устанавливается оставшееся количество и перед выгрузкой бункера подается сигнал. Этот позволяет своевременно подготовить резервный бункер. Установка полностью опорожняет первый бункер, а затем двигается дальше и в соответствии с заданным составом смеси завершает взвешивание её компонентов. Последующая загрузка осуществляется в центре из мешков или биг-бегов. Штрих-код обеспечивает загрузку нужного продукта в соответствующий бункер. Установка на дозирующее устройство является хаотичной, т.к. устройство управления распознает бункер по штрих-коду. Идеальным является вариант, когда поставщик доставляет товар непосредственно в DosiBox®. Пример 6: Дозирующий бункер со взвешиванием внизу. 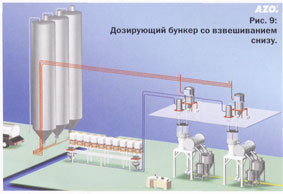 На рис. 9 показана расположенная на нижнем этаже система DOSINENTER® с многочисленными DosiBox®. Эта система автоматически взвешивает и подготавливает малые количества. Подача в горячий смеситель осуществляется пневматически. В целом можно сказать, что решения со стандартными бункерами являются более дешевыми, чем остальные. По этой причине, схема приведенная в примере 5, бесспорно является самой выгодной, даже в сравнении с примером 1, где для двух линий смешивания предусмотрена только одна общая система. Но если в примере 1 учитывать также увеличение высоты здания, то экономия не достигается. Системы сразу становятся дороже при использовании пневматической подачи, особенно ввиду обширных предписаний, например, АТЕХ* (см. пример 3, здесь исходные материалы подаются наверх не смешанными). * АТЕХ - свод директив Евроюза по взрывозащите в производственных помещениях.
Руди Бауман, руководитель отдела сбыта
AZO GmbH + Со. KG, Industriegebiet Ost, D-74706 Osterburken Тел.: +49 (0)62 91/92-0, Факс: /92-95 00 info@azo.de; www.azo.com |