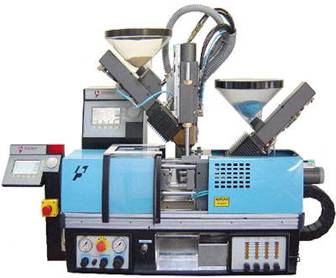
Себестоимость - один из важнейших факторов, определяющих конкурентоспособность производства. При таком крупносерийном и массовом производстве стандартной продукции, каковым является литье под давлением деталей из полимерных материалов (ПМ), этим фактором в первую очередь определяется рентабельность производства. Поэтому снижение себестоимости серийной продукции наряду с освоением новых видов изделий является приоритетной задачей предприятий по производству литьевых изделий. Эти вопросы, без сомнения, в той или иной степени решаются на каждом предприятии. Однако, учитывая актуальность проблемы, специалисты ООО «Промышленные Технологии» сделали попытку систематизировать этапы анализа эффективности налаженного производства при проведении организационно-технических мероприятий по его модернизации и снижению себестоимости литьевой продукции, что, возможно, поможет руководителям проверить, все ли сделано для этой цели. С учетом большой многовариантности литьевых производств мероприятия по их модернизации могут сильно различаться в зависимости от технического содержания, масштаба, продолжительности и экономической эффективности. Кроме того, при разработке мероприятий необходимо прорабатывать не только возможные варианты, но и последовательность их осуществления. Доля косвенных расходов (общепроизводственных и общехозяйственных) принята сравнительно большой в связи с низким уровнем съема продукции с единицы оборудования. Кроме того, следует заметить, что составляющая себестоимости продукции, расходуемая на зарплату сотрудников, принята характерной для отечественного производства, хотя в разных странах и регионах с различным уровнем доходов на душу населения она может значительно различаться. Как показал опыт исследования работы различных литьевых производств, мероприятия по их модернизации целесообразно проводить в несколько этапов, группируя на каждом этапе мероприятия, имеющие одинаковую направленность. На каждом этапе проводится следующая аналитическая работа: •технологический анализ производства; •технико-экономическая проработка вариантов мероприятий; •экономическая оценка вариантов мероприятий; •формирование состава мероприятий. 1-й этап. Совершенствование организации производства На этом этапе проводятся мероприятия, направленные только на совершенствование организации производства, обеспечивающие ликвидацию непроизводственных потерь и не вносящие каких-либо изменений в технологический процесс и его техническое оснащение - оборудование и оснастку, т. е. наименее капиталоемкие мероприятия. Срок их окупаемости составляет обычно от нескольких недель до нескольких месяцев. В результате технико-экономического анализа производства в нем выявляются наиболее вероятные «узкие места», такие, как: •несоответствие ассортимента изделий структуре парка литьевых машин; •несоответствие квалификации персонала составу проводимых работ; •неполное использование возвратных отходов; •нерациональность проектных решений по размещению оборудования и организации материальных потоков. Далее формируется комплекс мероприятий, направленных на снижение непроизводственных расходов и увеличение выпуска продукции, включая: •частичное перераспределение изделий по литьевым машинам; •повышение степени использования возвратных отходов; •повышение квалификации и сокращение численного количества персонала; •внедрение более прогрессивных методов организации ремонта оборудования и пресс-форм; •рациональную организацию материальных потоков по снабжению сырьем, производству и вывозу продукции; •организацию специализированных участков по выпуску однотипной продукции. Снижение себестоимости, достигаемое на 1-м этапе, зависит прежде всего от того, насколько повышение эффективности использования производственных ресурсов и ликвидация «узких мест» способствовали сокращению прямых расходов и увеличению выпуска продукции. 2-й этап. Совершенствование технологии На 2-м этапе разрабатываются мероприятия, направленные на совершенствование технологических процессов на базе имеющихся на предприятии ТПА и пресс-форм. На этом этапе проводится полный технологический анализ производства, включая: •анализ структуры норм расхода материала; •анализ структуры норм обслуживания ТПА и трудозатрат в целом; •анализ структуры технологических циклов. |