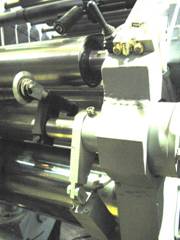
Преимуществами новой системы является то, что она полностью упраздняет необходимость наблюдения со стороны оператора, гарантируя тем самым полный контроль качества и в особенности во всем, что касается постоянства скорости запитки. Резина в виде непрерывной полосы обычно подается между валками каландра с помощью фиксированной опоры и колебательного конвейера. При этом мониторинг резиновой массы осуществляется десятью ультразвуковыми датчиками (которых может быть и меньше в зависимости от ширины полосы), равномерно распределенными по всей ширине материала. Такие датчики работают в очень узком звуковом конусе. Расчетный алгоритм основывается на следующих основных соображениях: ширина резиновой полосы определяется положением, в котором установлены ножи на участке смесительных вальцов, и ее мониторинг обеспечивается потенциометром; положение колебательного конвейера контролируется поворотным потенциометром. Регулирование резиновой массы осуществляется двумя пересекающимися контурами, первый из которых обеспечивает подстройку заданного значения общего количества, а второй осуществляет регулирование резины. Резина подается от смесительных вальцов, оборудованных ножами дистанционного управления, позволяющих автоматически повышать или же наоборот понижать ширину резиновой полосы в ходе запитки. Положение ножей на участке смесительных вальцов определяется с помощью математической формулы, полученной машиностроителем на основании многолетнего практического опыта. В частности, это достигнуто благодаря тому, что в лабораториях компании «Комерио Эрколе» установлен блок моделирования промышленного каландра с соответствующими смесительными вальцами, который дал возможность определить коэффициент поправки К, необходимый для учета характеристик резинового сырья, используемого при производстве. В результаты теоретических расчетов вносятся коррективы от ПИД-управления, в котором сопоставляется заданная высота резиновой массы и реальная высота, рассчитываемая как усредненное значение всех показаний измерения ультразвуковых датчиков. Такая формула начинает работать после того, как линия вышла на режимные показатели, и поэтому система подстройки резиновой массы должна включаться после стабилизации темпов производства. ПЛК управления также пользуется полученной информацией о распределении резины по ширине массы, определяемой как разница показаний различных датчиков. ПЛК управляет замедлением и остановкой колебательного конвейера в точке с низшим количеством резины, выражаемой в смысле положения колебательного конвейера. Расчетная программа позволяет также регулировать время остановки в двух крайних положениях, что представляет собой «системный параметр» в ручном режиме управления и что определяется распределением в автоматических условиях управления. Если смесительные вальцы снабжены блендером, можно работать с двумя резиновыми блоками одновременно с собственной системой управления для каждого. Первая система контролирует подачу резины на выходе из экструдера или другого смесительного устройства, вторая же контролирует резину на выходе блендера, сбрасываемую между вальцами запитки каландра. Обе эти точки запитки резины контролируются четырьмя ультразвуковыми датчиками того же типа, что и используемые в каландре. Сигнал поправки от первого резинового блока изменяет скорость работы экструдера ли смесительных вальцов, расположенных в непосредственной близости выше по линии, в то время, как во втором резиновом блоке сигнал поправки сдвигает передвижную платформу блендера, положение которой определяется соответствующим линейным потенциометром. www.comercole.it |