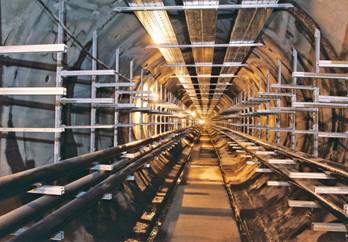
Традиционные технологии возведения кабельных и канализационных тоннелей предусматривают строительство в два этапа. На первом этапе укладывают в грунт железобетонные блоки, т.е. внешнюю оболочку тоннеля. Потом строителям приходится возвращаться к началу коллектора и возводить внутри него железобетонную «рубашку». Возведение таких тоннелей очень трудоемко, дорого и требует много времени. Кроме того, оно создает неудобства для жителей районов, где идет стройка, и негативно влияет на экологию города из-за выхлопов большегрузных автомобилей, подвозящих бетонную смесь. Да и эксплуатационные свойства этих тоннелей оставляют желать лучшего. По данным проведенных обследований, свыше 90% таких сооружений из-за механического износа наносами, выщелачивания, коррозии, трещинообразования выходят из строя ранее предусмотренных проектом сроков. Преждевременный износ тоннелей приводит к их отказу и необходимости выполнения ремонтных работ. Однако ремонтировать их трудно и дорого, и в большинстве случаев невозможно вскрыть. Расходы на содержание этих тоннелей в развитых странах доходят до 50% от общих вложений в строительство. Новая технология прокладки кабельных и канализационных тоннелей, разработанная учеными Московского государственного горного университета (МГГУ) совместно с партнерами, позволяет возводить их без вторичной обделки. Для этого высокоточные железобетонные блоки с внутренней стороны покрывают специальными полимерными составами. Сейчас разработаны три вида таких полимеров, прогнозируемая долговечность которых составляет от 10 до 100 лет (на практике найдут применение два вида – с долговечностью 34 и 100 лет). Технология строительства кабельных и канализационных тоннелей без возведения вторичной обделки («рубашки») увеличивает срок службы и надежность подземных сооружений, и позволяет использовать тоннелепроходческие машины меньшего диаметра, сократить объем разработки грунта, снизить материалоемкость, не требует доставки бетонной смеси по городу. Внедрение этой инновационной технологии снижает стоимость строительства на 25-30%, трудозатраты – в 5 раз, а сроки строительства – в 4 и более раз. Впервые в отечественной практике в тюбингах (железобетонных блоках) предусмотрены специальные закладные детали, позволяющие после окончания проходки в кратчайшие сроки смонтировать кронштейны для укладки электрических кабелей без нарушения поверхности блоков, что повышает гидроизоляционные и противопожарные свойства обделки. При строительстве по новой технологии применяется механизированный тоннелепроходческий комплекс (МТПК), предназначенный для проходки тоннелей в водонасыщенных грунтах с поддержанием заданного давления в призабойной камере. Применение таких МТПК обеспечивает проходку кабельных и канализационных тоннелей практически без просадки земной поверхности (максимально допустимая просадка составляет 3-4 мм). Это способствует сохранности коммуникаций, расположенных выше тоннеля, что особенно актуально для крупных городов, где плотность наземной застройки весьма высока, и достигается за счет постоянного нагнетания быстросхватывающегося раствора за блочное пространство в процессе продвижения проходческого щита. Разработчикам во главе с учеными МГГУ удалось за очень короткий срок – всего 3 года – пройти этапы от научно-исследовательских работ до опытно-конструкторских разработок и промышленного внедрения технологии. По этой технологии уже построены три кабельных коллектора в Москве длиною 1,3 км, 3,5 км и 3 км. В феврале 2009 года в Царицыно (Москва) начнется строительство первого в мире экспериментального канализационного канала с полимерной футеровкой. Работа выполняется в партнерстве с ГУП «Мосинжпроект», ОАО «Институт Каналстройпроект», МГУП «Мосводоканал», ОАО «Моспромжелезобетон», ГУП «НИИМосстрой», ОАО «СУПР», НПО «Космос» и немецкими компаниями. Журнал «Наука и Жизнь» |