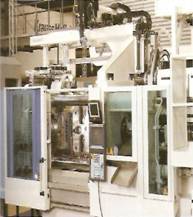
Экономия возникает благодаря уменьшению числа составных компонентов изделия, что в свою очередь снижает затраты на изготовление и монтаж. Литье под дав¬лением многокомпонентного изделия из расплавов различных полимеров на одной пресс-форме может осуществляться разными методами, такими, как например, многокомпонентное, многоцветное и сэндвич-литье под давлением, а также литье под давлением, совмещенное со сборкой изделия. Пример тому - SkinForm, при которой отлитые под давлением несущие части изделия покрываются в форме мягкой полиуретановой оболочкой. Так за один рабочий цикл производят разнообразные высококачественные изделия, например, детали отделки салона автомобиля. „Х-Форм" вместо технологии „Металл-резина" Актуальным примером комбинированной технологии многокомпонентного литья, открывающей новую гамму применений в области переработки пластмасс, является технология „X-Форм" (X-Form), одновременно объединяющая в себе три процесса - литье под давлением, экструзию и реакционное формование. Технология „Х-Форм" разработана для производства сложных изделий, в которых часто используются соединения металл-резина. Например, крышки корпусов с интегрированным уплотнением или опоры двигателей. Данная технология, по сути, заключается в том, что термопластичный полиуретан (TPU) новой марки непосредственно во время охлаждения переходит в сшитый полиуретан TPU-X. Этот процесс реализуется на осуществляющем прямое компаундирование термопластавтомате, который, в свою очередь, объединяет в себе непрерывный процесс экструзии, служащий для равномерного распределения сшивающего агента в расплаве TPU с цикличным процессом литья под давлением. В качестве практического применения данной технологии ее создатели разработали и изготовили конкретное изделие - гаситель колебаний, который применяется в различных монтажных опорах или ходовой части автомобиля. Гаситель колебаний состоит из двух компонентов: первый -усиленный стекловолокном термопластичный корпус с гильзой, а второй - находящийся между корпусом и гильзой эластичный демпфирующий элемент из TPU-X. Сюда же добавляется и расположенное по периметру эластичное уплотнение, также из ТРи-Х. Преимущество - выигрыш времени Серьезным преимуществом технологии „Х-Форм" является сокращение времени цикла до 60 секунд. Это становится возможным благодаря производству конечных изделий за три технологические операции, одновременно происходящие в производственной ячейке. Четвертая операция - извлечение готового гасителя колебаний роботом с линейными перемещениями. Демпфирующий эластичный элемент должен воспринимать сильные колебания и поэтому имеет толщину стенки 15 миллиметров. При подобной концентрации материала следовало бы рассчитывать - из-за требующегося времени охлаждения - на большее время цикла. Только использование пресс-формы с поворотным столом позволяет реализовать цикл за 60 секунд. В ходе первой технологической операции из полиамида отливается корпус с гильзой. Для каждой последующей операции пресс-форма поворачивается на 90 градусов. На второй и третьей позициях пресс-формы в две стадии отливается демпфирующий элемент из TPU-X. Четвертая позиция служит для съема готового изделия, причем при сомкнутой пресс-форме. По сравнению с классической переработкой время цикла изготовления уменьшается в четыре - шесть раз. Следует подчеркнуть, что в отношении технологии „Х-Форм" речь идет о классическом двухкомпонентном литье под давлением. Для темперирования пресс-формы не требуется наличие специальных горячих и холодных зон, что значительно упрощает ведение процесса. Данный процесс был разработан KraussMaffei, Muenchen (Мюнхен, Гер.мания), совместно с Elastrogran GmbH, Lemfoerde (Лемфёрде, Германия) и Mues Products & Moulds GmbH, Kolbermoor (Кольбермоop, Германия). C анализом российского рынка полимерных компаундов можно познакомиться в отчете Академии Конъюнктуры Промышленных Рынков «Рынок полимерных компаундов в России». www.polymery.ru |