Основной особенностью данной установки является использование моношнековых экструдеров в отличие от основной тенденции рынка, связанной с преобладающим Накопив опыт создания многочисленных малых и средних установок для переработки крошки ПЭТ, полученной из отработанных бутылок, компания «БГ Пласт» (BG Plast) недавно разработала новую линию для производства 1.500 кг листа АПЭТ из крошки без сушки и кристаллизации, полученной на 100% из бывших в употреблении бутылок.
|
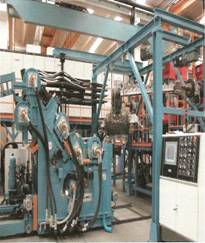
Основной особенностью данной установки является использование моношнековых экструдеров в отличие от основной тенденции рынка, связанной с преобладающим использованием двойных шнеков однонаправленного вращения. Компания уделила много усилий для разработки целой серии одношнековых экструдеров для переработки этого материала, снабжая их специальными системами дегазации, присоединенными к фильтрующему насосу сухого типа, который генерирует глубокий вакуум с высокой производительностью (5 мбар при 2.000 куб.м/ч). Кроме того, в них предусмотрена система весового дозирования 4-х компонентов для запитки 3-х экструдеров. Две из этих установок диаметром 150 и 100 мм предназначены для переработки бутылочной крошки и отходов термоформовки, в то время как третья установка диаметром 70 мм перерабатывает первичный материал. Наличие 4-х дозаторов на каждый экструдер дает возможность работать с различными рецептурами, применяя различные добавки, которые необходимы, например, для производства СРЕТ,против блокировки, для окрашивания и пр. Экструдеры подают материал внутрь фильтрующего двухкаскадного блока за счет объемных насосов. Внутри этого блока имеется устройство укладки в слои различной формы, позволяющее придать слоям различную конфигурацию в зависимости от потребностей. До поступления в каландр экструдируемая заготовка пропускается через плоскую головку шириной 1.400 мм с внутренним делением лезвия. Суженная форма головки и вертикальность ее размещения позволяют производить работу в непосредственной близости от точки пересечения валков каландра, что позволяет осуществлять четкий контроль материала, который предстает в достаточно разжиженной форме. Каландр горизонтального размещения состоит из 5 валков, 4 из которых обладают диаметром 500 мм и один, находящийся в центральном положении, диаметром 650 мм. Первый валок снабжен механизмом смещения осей, позволяющим поддерживать на отличном уровне соблюдение допусков по толщине, что особенно важно при работе с тонкостенными изделиями. Благодаря моторизованным раскаточным приспособлениям и специальному обрезиненному валку с терморегулированием становится возможным дублировать на таком каландре любую пленку барьерного типа за счет EVOH для получения специальных листов, применяемых в пищевой промышленности. Предыдущий участок линии включает в себя цифровой толщиномер на воздушной подушке, устройство для обработки двухфасадной короны, силиконовую ванну с печью сушки и первый тяговый механизм с вращающимися лезвиями для боковой обрезки. Между первым и вторым тяговыми механизмами располагается автоматический накопитель вместимостью 40 м, необходимый для бесперебойной смены катушки, учитывая, что рабочая скорость в машине достигает уровня 50 погонных метров в минуту. Перед вторым тяговым механизмом установлены дополнительные вращающиеся лезвия, позволяющие разрезать полотно на 3 полосы с замоткой на катушки на отдельных закаточных устройствах. И, наконец, установка пригодна также для производства полипропиленовых и полистироловых листов без необходимости внесения существенных изменений. |