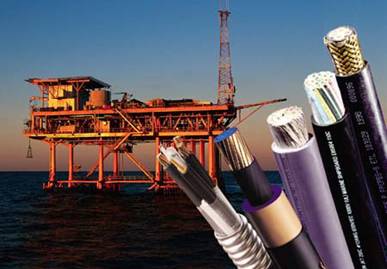
Учёные из различных областей – физики, химики, инженеры-механики, специалисты в области полимеров, работающие в отделе исследований и разработок при технологическом центре компании General Cable в городе Индианаполис (штат Индиана, США), разрабатывают материалы для производства изоляции и оболочек выпускаемых компанией силовых кабелей, предназначенных для использования в электроэнергетике, нефтехимическом, угледобывающем, ядерном, военном и других секторах. Путём добавления перекисей в термопласты, они создают термоотверждающиеся или сшиваемые полимеры, которые выдерживают более высокие температуры, чем могут выдержать неизменённые термопластические изоляционные материалы. Как объясняет руководитель технической службы компании г-н Брюс Джонстон (Bruce Johnston), полимер в гранулах длиной 0,125 дюймов должен поглотить перекись примерно в соотношении: от 1% до 3% своей массы. Для того чтобы увеличить срок службы материала и улучшить его электрические свойства, можно также добавить антиоксиданты. При проведении каждой серии экспериментов команда специалистов загружает смесительную установку гранулами термопластической смолы, которые могут включать полиэтилен низкой плотности (LDPE), линейный полиэтилен низкой плотности (LLDPE), этилен-винилацетат (EVA), полипропилен (PP), хлорированный полиэтилен (CPE) или кремнийорганическое соединение, вливают перекись и запускают смеситель. Затем могут быть добавлены дополнительные агенты для стабилизации смеси полимера и перекиси. При изучении новых материалов, как подчёркивает г-н Джонстон, смесь проверяют каждые 15 минут, поскольку в случае неправильно установленной температуры приходится много времени тратить на очистку установки. Обычно время смешивания составляет 2 часа, но некоторые материалы поглощают перекись за 20 минут. Сополимеры, такие как, например, этилен-винилацетат и этилен-акрилат (EEA), относительно мягкие и поглощают перекись при комнатной температуре. Другие материалы поглощают перекись только при нагревании. Если смеситель должен быть нагрет для того, чтобы произошло поглощение перекиси, гранулы полимера могут стать липкими и пристать к барабану смесительной установки. Тогда придётся понизить температуру барабана и продолжать смешивание до охлаждения гранул. Термопласты могут также разрушиться или полностью расплавиться, если температура смешивания будет слишком высокой. Более высокие усилия сдвига и несоответствующий контроль температуры, характерные для предыдущего оборудования, приводили к тому, что команде исследователей приходилось многократно запускать и останавливать высокоскоростной смеситель для того, чтобы поддерживать низкие температуры. На предприятии компании General Cable в Индианаполисе уже имелась в эксплуатации смесительная установка производства компании Munson Machinery (г. Ютика, штат Нью-Йорк), поэтому команда Джонстона совместно с компанией Munson выбрала самую подходящую для своих целей машину. Было выбрано роторное перемешивающее устройство периодического типа марки MX-1-SSJ меньшего размера, чем стандартная промышленная установка. Смеситель ёмкостью 1 кубический фут мягко проворачивает, разрезает и перемешивает материал во вращающемся барабане. Такой ход машины обеспечивает снижение до минимума вероятность возможной деградации хрупких или чувствительных к температуре материалов. Смешивание с низким усилием сдвига минимизирует теплоту трения и образование тонкодисперсных частиц. Эта смесительная установка также оснащена гидравлическим устройством, предназначенным для наклона установки при выполнении операции по удалению материала или операции очистки. Группа разработчиков предусмотрела также так называемую водяную рубашку, которая позволяет эксплуатировать смеситель при температурах до 200°F. Все эти факторы служат обеспечению равномерного нагрева и устраняют операции по повторному перемешиванию. Для того чтобы определить оптимальный объём загружаемой партии, были проведены эксперименты с партиями объёмом в 50 фунтов (50 х 453,6 г) – это примерно максимальная ёмкость смесительной установки. Однако было определено, что для материалов с удельной массой более 1,0 достаточно партий объёмом 25 фунтов для того, чтобы наложить покрытие на 3000 – 4000 футов (900 – 1200 метров) проволоки диаметром 1,6 мм (14 AWG) – для первоначальной оценки. Для некоторых материалов с удельной массой менее 1,0 требовались партии объёмом 50 фунтов. Представители компании General Cable утверждают, что описанная смесительная установка легко адаптируется для различных объёмов партий материала и различных уровней температуры, при этом снижается до минимума нежелательное усилие сдвига, тепловыделение и ухудшение свойств или деградация материала. По материалам "КАБЕЛЬ-news"
|