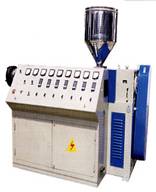
В этом случае проверяется время погружения стального шарика в раствор из циклогексанона и порошкообразного ПВХ. Чем выше значение К, тем более вязким является расплав и тем тверже и жестче получаемый оконный профиль. С другой стороны, при более высоких значениях К переработка становится более тяжелой, требуется больше энергии для пластификации, и переработка осуществляется очень близко к температурам разложения ПВХ. Для рецептур оконного профиля значение К обычно составляет 68, иногда 65, иногда 70. Например, в стандартном ПВХ российских марок С 70 58 М он составляет 70. Другим критерием качества ПВХ является форма поверхности зерен. Она должна быть максимально большой, т.е. быть сильно "изрезанной бороздами". Этим обеспечивается хорошее "впитывание" стабилизаторов и скользящих добавок и гарантируется хорошее диспергирование аддитивов. Гладкая поверхность зерен практически не дает возможности связывания аддитивов, зерна ПВХ не охвачены стабилизаторами и скользящими добавками. Следствием этого являются местные разложения ПВХ и образование пятен (крапинок) на поверхности профиля. Следующий критерий - насыпной вес ПВХ должен быть в пределах 580-600 г/л. Слишком малый насыпной вес ведет к пропорциональному уменьшению производительности экструдера, поскольку в экструдере выход материала определяется объемом пластификата. С уменьшением же выхода уменьшается и степень пластификации расплава, а также заполнение междушнекового пространства, начиная с зоны сжатия (компресии). Практически, переработка ПВХ с низким насыпным весом означает недозагрузку шнеков. Таким образом, все это негативно сказывается на пластификации, ударной вязкости, свариваемости профилей. Точно также хорошая сыпучесть является предпосылкой для хорошей пластификации. Плохая сыпучесть ведет к уменьшению выхода и имеет те же последствия, что и малый насыпной вес. Процесс смешивания также сильно зависит от насыпного веса и сыпучести ПВХ. Так, при малом насыпном весе допустимый объем заполнения смесителя может быть значительно превзойден. Процесс смешивания при этом нарушается, сухая смесь (dry blend) перемещается в основном только в горизонтальном направлении, в вертикальном же практически не происходит никакого перемещения, при этом не создается процесс завихрения. Следствием этого являются неравномерное диспергирование и колебания в экструзионном процессе. Слишком малая сыпучесть приводит к увеличению времени смешивания в результате более длительного опорожнения смесителя и уменьшает этим общую производительность смесителя. Рассмотрим также некоторые конкретные аспекты применения аддитивов (стабилизаторов, скользящих добавок, модификаторов, наполнителей и т.д.). Достаточная стабилизация надежно обеспечивает устойчивость белого цвета профиля. При этом даже короткие остановки из-за отключения тока, перерыва в подаче материала на 5-10 мин. не приводят к термическому разложению материала, хотя и могут вызвать его некоторое пожелтение. Весьма важна дозировка (соотношение) внутренних и внешних скользящих добавок Передозировка скользящих добавок ("пересмазанная" смесь) проявляется в том, что имеется слишком много внешних скользящих добавок, материал плохо пластифицируется и находится в порошкообразном состоянии при дегазации, наблюдаются высокое давление и низкая температура массы. Предотвращение этого возможно путем снижения количества скользящих добавок. Недостаток скользящих добавок ("недосмазанная" смесь) проявляется в слишком сильной пластификации, образовании пузырьков от перегрева на внутренних поверхностях, высоком трении в зоне выхода, высокой температуре и низком давлении массы. Предотвращение - путем увеличения количества внешних скользящих добавок. Поскольку на практике работают не с отдельными аддитивами, а с Masterbatcn (маточная смесь или суперконцентрат), то для изменения количества внешних скользящих добавок варьируют общее количество компаунда. Но поскольку при этом меняется и количество стабилизатора, то такому изменению ставятся нижние допустимые границы. В зависимости от изготовителя, геометрии шнеков и производительности, минимальные значения лежат в пределах 4,2-4,6 частей на 100 частей ПВХ. В сомнительных случаях рекомендуется консультироваться с изготовителем сырья. Комбинация скользящих добавок всегда рассматривается в сочетании с ПВХ и имеет рещающее значение для глянца поверхности и возможности появления отложений на фильере или калибраторе. Для увеличения глянца и пластификации добавляется оксидированный РЕ-воск в количестве 0,05-0,2 частей на 100 частей ПВХ. Уменьшения же отложений можно добиться путем добавления силикагеля. Важное значение имеют и модификаторы ударной вязкости. Это особенно важно для стойкости оконного ПВХ-профиля при очень низких зимних температурах. С увеличением вязкости, однако, снижается жесткость профиля. Следует отметить, что ранее широко применявшийся модификатор EVA теперь практически полностью заменен на акрилат. Модификатор может либо уже содержаться в сухой смеси (7-8 частей), либо сополимеризироваться прививкой при полимеризации (6-7 частей). В Европе очень часто используется второй вариант, что обеспечивает более высокую равномерность показателей ударной вязкости и хорошее качество поверхности. Добавление модификаторов целесообразно в пропорции 6-8 частей, поскольку увеличение выше этого значения приводит к удорожанию рецептуры, не обеспечивая сколько-нибудь заметного дальнейшего повышения ударной вязкости. Полезно применение также добавок текучести на акриловой основе в пределах 1-2 частей, вводимых также для улучшения пластификации. |