Одной из самых давно встречающихся в области производства ситуаций является ситуация, при которой заказчики требуют, чтобы технология отрасли могла работать за пределами имеющихся у нее на данный момент мощностей для того, чтобы добиться соответствия требованиям заказчиков. А после того, как новый уровень достигнут, на отрасль снова начинают оказывать давление.
Именно так все и происходит в области пневмоформования толстого термопластического листа. От простых держателей до панелей управления машин, ведущие компании мира, занимающиеся пневмоформованием, вынуждены соглашаться с постоянно растущими требованиями для того, чтобы создавать все более и более сложные детали. Наряду с повышением степени сложности деталей, повышаются и требования к жесткости допусков, как для формования, так и для обрубания деталей в соответствии с размерами. Пневмоформование толстого листа аналогично давно известной технологии вакуумного формования в том плане, что форма вводится в нагретый термопластический лист, и используется вакуум для вытяжки сопротивляющегося воздуха из промежутка между формой и листом. Давление воздуха окружающей среды затем заставляет горячий лист принимать форму формы, а затем лист остывает с получением жесткой формы. При пневмоформовании отсек с регулируемым давлением подводится под заднюю часть листа со стороны, противоположной форме. При создании вакуума в камеру вводится сжатый воздух, он распластывает горячий лист по поверхности формы. Обычно используемыми значениями давления являются от 35 фунтов на кв. дюйм до 60 фунтов на кв. дюйм (от 241 кПа до 414 кПа). Тем не менее, для производства крупных деталей, изготавливаемых из материалов с более высокой прочностью в нагретом состоянии, может потребоваться более высокое давление. Материал будет повторять все детали формы, такие как острые и резкие углы, логотипы и фрагменты букв, и даже общую текстуру, как поверхностную, так и глубокого нанесения. Детали поверхности будут исполнены так, что детали будут неотличимы от деталей, изготовленных литьевым формованием. При создании деталей и корпусов у пневмоформования имеется множество преимуществ перед литьевым формованием: | 1. Более низкие начальные инвестиции для небольшого количества деталей (менее 2,000) | 2. Меньшая продолжительность полного цикла формования: от 8 до 12 недель | 3. Меньшие затраты на форму - 10 - 20% от литьевого формования | 4. Детали относительно свободны от напряжения |
Единственными недостатками являются финансовые соображения: | 1. Затраты на переработку смолы в лист и использование сверхгабаритного листа, чтобы создать зажим во время нагревания и формования, добавляются к материальным затратам. | 2. Для деталей с одной поверхностью нужны дополнительные трудозатраты, чтобы что-то предпринять при отклонениях или наличии деталей с обратной стороной при необходимости. | 3. Подрезание избытка материала, используемого для зажимания и всех отверстий, требует дополнительных трудозатрат помимо затрат на само формование. |
Типичным примером сравнения между пневмоформованием и литьевым формование является сопоставление, проведенной для "компьютеризованной машины стенографа суда". Трехкомпонентный корпус состоит из основания, крышки и небольшой дверцы доступа. По оценкам заказчика, максимально требуемым количеством будет от 1000 до 1200 сборок. Для допроизводственной демонстрации продукта потребуется ускоренный период от разработки до внедрения проекта. 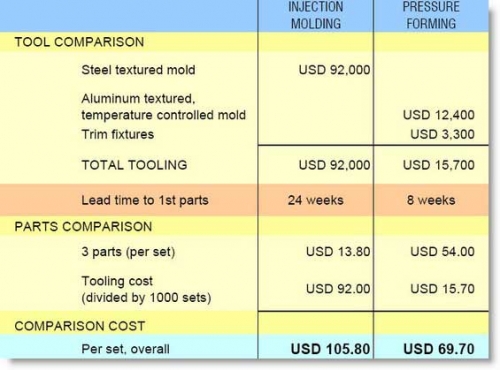
Не существует единой формулы, которую можно было бы использовать для расчета типа: размер детали x материал x и т. д. для сопоставления затрат при литьевом формовании и пневмоформовании. Для каждого проекта необходимо создавать оценку затрат и сравнивать их. Термопластические материалы, которые чаще всего используют для пневмоформования, обычно имеют рейтинг по огнестойкости для использования при создании корпусов электронных устройств. Примерами таких материалов являются: FRABS, PVC/акриловые сплавы, модифицированный полифениленоксид, поликарбонат, PVC, и смеси ABS/поликарбоната. Чем крупнее деталь, тем больше экономия за счет затрат на инструмент. Затраты на формы для пневмоформования не увеличиваются пропорционально увеличению размера формы. Нередко Вы можете удвоить размеры детали при увеличении размера формы всего лишь на 25% - 30%. А стоимость форм для литьевого формования, напротив, растет непропорционально увеличению размера.
Формы для пневмоформования всегда будут изготавливаться из алюминия из-за его способности к теплопередаче, которая очень важна для охлаждения формуемого листа. Алюминий также экономичен при литье и/или машинной обработке, и хорошо выдерживает давления, которые создаются в форме. В формах для пневмоформования можно контролировать температуру за счет создания каналов жидкости в обратной части поверхности формы. По этим каналам течет вода или раствор этиленгликоля с контролируемой температурой, так отводится тепло, которое отадется из горячеформованного листа в форму. Поскольку давление удерживает форму, по крайней мере, на протяжении части цикла охлаждения, при непосредственном контакте с формой теплота будет передаваться быстрее и более однородно, чем при осуществлении простого вакуумного формования. Менее продолжительные циклы охлаждения важны для экономии затрат на деталь, а однородное охлаждение чрезвычайно важно для создания низкого остаточного напряжения в готовой детали. Чем выше температура формы в ходе формования, тем сильнее усадка пластмассы во время формования и охлаждения. Таким образом, за счет тщательного контроля однородности общей температуры в форме мы можем контролировать степень однородности размеров готовой детали, а также избежать коробления после формования. Детали, изготавливаемые пневмоформованием, могут быть дороже деталей, изготовленных вакуумным формованием, из-за большого количества брака, создающегося за счет более высоких косметических требований и более жестких размерных допусков.
Необходимо также уделять внимание второй поверхности, или той стороне детали, которая находится напротив детализированной поверхности формы. Для создания пневмоформованных деталей, которые могут составить конкуренцию по конструкции деталям, изготовленным литьевым формованием, часто бывает необходимо добавление монтажных стоек, ребер, зазоров и т. д. Такие вставки могут создаваться механической обработкой, на винтонарезных станках, литьевым формованием или же с помощью термоформования; их также можно соединять с помощью скрепления или ультразвуковой сварки. Решение относительно того, будет ли деталь окрашена или же будет текстурирована форма, будет использоваться однородно окрашенный материал или же материал с поверхностным покрытием с выбранной окраской на любом основном листе, зависит от того, какой внешний вид желает получить заказчик, или же от финансовых соображений, связанных с размером партии деталей. Здесь не существует готовой формулы, которую можно использовать, просто расчет, основанный на здравом смысле. Например: Формы + Доп. затраты на подходящий по цвету лист/ Количество деталей по сравнению с: Затратами на окрашивание + доп. затраты на погрузку/разгрузку Еще одним фактором, который следует учитывать, является возможность сочетания пневмоформованных деталей с металлическими окрашенными деталями. Может оказаться, что желательно окрашивать все детали для получения хорошего соответствия цвета и текстуры всей сборки. При пневмоформовании часто используются надрезы и негативно сформованные участки в вертикальных стенках деталей. Они используются конструкторами для того, чтобы получить жесткое соответствие допусков при сборке деталей. Для извлечения сформованной детали из формы необходимо, чтобы одна или несколько секций формы убиралась обратно в форму, чтобы деталь можно было извлечь. Это движение можно получить за счет использования пневматических или гидравлических цилиндров, или же электрических винтовых приводов, встроенных в форму. Еще одним вариантом является петлевое убирание подрезных формовочных секций, которые висят по открытому краю формы с негативными гнездами так, чтобы они не мешали извлекать деталь из формы. Существует также идея с извлечением свисающих частей формы вместе с формованной деталью, с последующим удалением и возвращением на место в форме до того, как следующий нагретый лист поступит туда для формования. Надрезы усложняют конструкцию формы и повышают начальные затраты, они также создают постоянные затраты на материально-техническое обслуживание. Тем не менее, эти затраты составляют лишь часть тех затрат, которые понадобятся для создания той же детали с помощью литьевого формования.
Не существует единых установленных для всей отрасли размерных допусков, поскольку они определяются степенью сложности оборудования и особенностями практики каждого отдельного производителя, занимающегося пневмоформованием. Компаниям, которые скажут, "Да, мы сможем выдержать очень жесткие допуски", понадобится современное управляемое компьютерами оборудование для формования и вырубания, а также очень жесткий контроль при создании инструмента. Одной из компании, которая имеет достаточно хорошее оборудование и обширный опыт для выполнения таких работ, является компания Profile Plastics Corporation из Лейк Блаффа, Иллинойс, расположенного к северу от Чикаго в США. На проходившей в сентябре 1998 года Конференции по термоформованию SPE эта компания получила награду года за лучший "Многокомпонентный корпус медицинского устройства". Победившей сборкой деталей стал корпус Ergodyne ON 3. Компания разработала машину, которая помогает сестрам перемещать пациентов с кроватей на каталки и обратно, таким образом, уменьшается вероятность повреждений, которые можно получить при подъеме и перетягивании.
Для этой машины требовалась сборка корпусa, и компания-разработчик хотела, чтобы у нее был свежий и высокотехнологичный вид. Высокие затраты и большой период от разработки до внедрения продукта, связанные с использованием инструментов для литьевого формования, заставили разработчиков искать другие варианты. Profile Plastics приняла заказ на разработку и производство корпуса. Шесть пневмоформованных деталей были разработаны для создания сборки сложного корпуса с помощью целого ярда прорезей. Формы для пневмоформования были изготовлены из алюминиевых заготовок при контролируемой температуре, затем было осуществлено химическое травление с получением мягкой матовой текстурированной поверхности. Температурный контроль позволял выдерживать жесткие размерные допуски формования, получать низкое остаточное напряжение для недопущения коробления, сохранять свойства материала, а также осуществлять контроль однородности блеска.
В трех деталях имелись прорези, в одной из них, в горизонтальной крышке имелись 1-дюймовые изгибы с обеих сторон детали, имевшей 8 дюймов в ширину и 10 дюймов в глубину. В качестве материала был выбран ABS, модифицированный PVC для получения огнестойкости. Экструдированные листы были предварительно окрашены, и для того, чтобы гарантировать соответствие цветов, каждaя партия материала, поступавшая для серийного производства, проверялась спектральным фотометром.
Толщина материала крышки перед формованием составляла 0.325 дюйма (8.2 мм), что позволило получить деталь с довольно однородной толщиной стенок 0.100 дюйма (2.5 мм). Для производства других деталей с менее жесткими формовочными отношениями использовались исходные листы меньшей толщины. При производстве этих деталей достигается исключительная однородность формования, нарезания и создания блеска.
www.newchemistry.ru |