Параметры материала и технологии Наиболее очевидными параметрами материала и технологии являются состав материалов основной подложки и реализуемая технология (экструзия, нанесение экструзионного покрытия, нанесение печати и т. д.). После подробного анализа этих факторов, их воздействия на обработку коронным разрядом определение размерности становится еще более сложным. Следует начать с состава материала подложки, и предположить, что все материалы простые, т. е. чистые материалы без каких-либо добавок. Данные о поверхностном натяжении типичных подложек, которые используются в экструзионной и перерабатывающей отраслях, даны в таблице 3. Таблица 3 показывает имеющиеся проблемы, поскольку большинство материалов определяется диапазоном типовых значений поверхностного натяжения. Различные значения поверхностного натяжения каждого конкретного материала могут объясняться несколькими оказывающими воздействие факторами, такими как метод производства (выдувная пленка или литая пленка), колебания температуры экструзионной головки во время экструзии, а также тип и количество загрязнения, которое всегда присутствуют даже в самой высококачественной пленке. Если данный материал обрабатывается при определенной заданной плотности мощности, его поверхностное натяжение будет увеличено. Тем не менее, и получаемое конечное поверхностное натяжение, и размер повышения зависят от исходного значения поверхностного натяжения материала. Так, например, применение плотности мощности 1.2 при обработке PET при 41 дине может дать повышение до 46 дин, но применение той же плотности мощности 1.2 при обработке PET при 44 динах может дать повышение всего лишь до 48 дин. Хотя конечный дин уровень и выше во втором случае, прирастающее увеличение меньше из-за исходного значения дин уровня. Далее изменение реакции чистого материала на обработку коронным разрядом усугубляется наличием определенных концентраций добавок. Влияние концентраций добавок будет рассмотрено в данном разделе ниже. Как уже упоминалось ранее, различные материалы или подложки по-разному реагируют на обработку коронным разрядом. Некоторые материалы, такие как некоторое полиэфиры, хорошо воспринимают обработку, и демонстрируют быстрое повышение поверхностного натяжения при относительно низких уровнях плотности мощности, скажем от 0.9 до 1.2. Другие материалы, такие как полиэтилен, хуже воспринимают обработку, но демонстрируют менее существенное повышение поверхностного натяжения при умеренных значениях плотности мощности, скажем от 2.0 до 2.5. И, наконец, есть материалы, такие как полипропилен, которые сложно обрабатывать, и которые дают лишь умеренное повышение поверхностного натяжения при относительно высоких уровнях плотности мощности, скажем от 2.5 до 3. 0. Колебания в области реакции материала на обработку коронным разрядом еще более усиливаются из-за различий в технологических параметрах. Ясно, что для экструзии, нанесения экструзионного покрытия и экструзионного ламинирования требуются различные уровни обработки для того, чтобы получить приемлемые качество продукта и уровни производительности. Тем не менее, менее очевидным выглядит тот факт, что экструзионное покрытие из определенной смолы, например, РЕТ, даст подложку с реакцией на последующую обработку, отличающуюся от реакции той же смолы, которая подвергалась экструзии в литую пленку. Еще одним усложняющим ситуацию фактором, который существенно повышает требования в области плотности мощности, является сочетание экструзии литой пленки с использованием рамы для растягивания и ориентирования плёнки. В таких случаях различия в реакции на обработку коронным разрядом обусловлены следующими элементами: 1. Изменениями молекулярной структуры в результате процесса экструзии. 2. Температурой подложки в момент ее попадания на станцию для обработки коронным разрядом. 3. Размещением станции для обработки коронным разрядом относительно места экструзии. Изготовление литой пленки хорошо показывает все более слабую реакцию на обработку коронным разрядом из-за молекулярной структуры, температуры подложки и размещения станции для обработки (см. рисунок 27). В этом случае пленку экструдируют, отливают на охлаждающие вальцы, а затем биаксиально растягивают при нагревании перед намоткой. 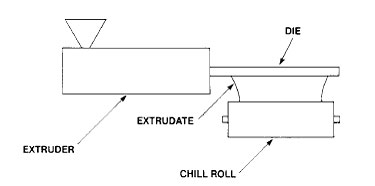 Рисунок 27. Начало производственной линии
|