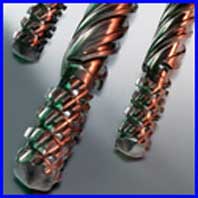 В современной пластмассовой промышленности и с самых первых дней возникновения экструзии пластмассы, конечные потребители всегда зависели от фирм-изготовителей комплектного оборудования (OEM) и/или производителей шнеков. С годами большинство производителей усвоили несколько основных правил, связанных с конструкцией шнека, но до конца они так и не поняли, почему же их поставщики рекомендовали им обратить особое внимание на некоторые характеристики шнеков, которые они приобретали. Эта статья даст некоторые базовые знания, необходимые конечному потребителю для того, чтобы принимать правильные решения при использовании или приобретении нового одношнекового компонента для гладкоканального применения. Номенклатура Прежде, чем начать, нам необходимо дать характеристику некоторых основных компонентов однозаходного шнека. Эти характеристики представлены на Рисунке 1. 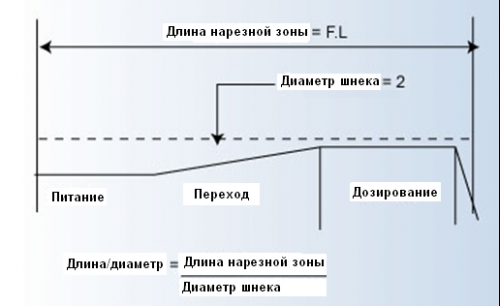
Рисунок 1.
Отношение длины и диаметра Некоторые производители комплектного оборудования определяют свое собственное отношение L/D (или отношение длины и диаметра) не так, как другие. Некоторые производители определяют его как "закрытую" часть шнека, или измеряют длину нарезной части с передней части загрузочного отверстия до конца шнека. Некоторые измеряют длину нарезной части от центра загрузочного отверстия, в то время как другие измеряют реальную «эффективную» длину всей нарезной части при определении отношения длины и диаметра. То, как они определяют отношение длины и диаметра, это особый вопрос, а вот реальный объем, который должен обработать экструдер, определяется, как показано на Рисунке 1. Пример того, как определяется отношение длины и диаметра для 2.5" шнека, будет выглядеть следующим образом: Диаметр шнека = 2.5" Длина нарезной зоны = 63" отсюда, L/D = 63" / 2.5" = 25.2 L/D Компания-производитель комплектного оборудования классифицировала бы этот экструдер как 24:1 L/D, а производитель шнеков, как правило, оценивал бы его как 25.2 L/D, поскольку именно таков объем машинной работы, которую должен выполнить производитель шнеков для того, чтобы завершить изготовление продукта. Отношения длины и диаметра типовых экструдеров обычно составляют 24:1 и 30 или 32:1, но имеются и специальные применения, для которых создаются очень короткие экструдеры 10:1 L/D и очень длинные 50:1 L/D. Надлежащее отношение длины и диаметра определяется той технологией и тем применением, требованиям которых необходимо удовлетворять.
Зона питания - Глубина Обратимся к Рисунку 1. Зона питания шнека является первым элементом, в котором полимер вводится в шнек. Как правило, у гладкоканальных экструдеров это самая глубокая зона шнека. При использовании шнеков более мелкого размера, с диаметром 2.5" и менее, следует уделять особое внимание этой части шнека для того, чтобы снизить риск скручивания пополам из-за создания чрезмерного крутящего момента шнека. Иногда рекомендуется использовать более мелкие шнеки, изготовленные из нержавеющей стали 17-4 Ph, или какого-либо иного высокопрочного материала для того, чтобы снизить риск возникновения данного типа отказа. Основное правило заключается в том, что зона питания шнека не должна быть глубже, чем: Fdmax = .2(диаметр шнека) Ур. 1 Это для шнеков, которые имеют диаметр 4.5" и менее. Так, например, для шнека 2.5" это будет: Fdmax = .2*(2.5") = .500" Ур. 2 Если конструкция шнека требует, чтобы у него была зона питания, превышающеяя это максимальное значение Fdmax, следует сделать соответствующие расчеты крутящего момента. Затем, если прочность шнека превысит коэффициент безопасности 2:1 исходной стали, с расчетом на которую проектируется шнек, следует выбрать сталь с большей прочностью.
Зона питания - Длина Основной функцией зоны питания шнека является функция подачи твердого материала. Основное теоретическое правило для подачи по конвейеру твердых материалов гласит, что "пластмасса должна прилипать к цилиндру для того, чтобы полимер мог продвигаться дальше". Для того, чтобы такое функционирование могло осуществляться, коэффициент трения (COF) полимера должен быть выше у стенок цилиндра, чем у основания шнека. У некоторых полимеров от природы коэффициенты трения лучше, чему других. Поэтому в случаях использования таких смол нет необходимости иметь длинную зону питания. Обычно для большинства смол длина зоны питания, равная четырем или пяти диаметрам, после загрузочного отверстия позволяет создать давление, достаточное для того, чтобы протолкнуть материал далее. В случае подачи смолы похуже или же материалов с низким коэффициентом трения, можно использовать длину зоны питания размером от восьми до десяти диаметров. Обычно одной из причин использования более длинных зон питания является необходимость большего нагревания для твердых форм смолы, чтобы заставить ее приклеиваться к цилиндру, что затем должно способствовать созданию давления, необходимого для дальнейшей передачи твердого материала. Следует также отметить здесь, что в случае подачи не очень качественного материала имеет смысл использовать внутреннее охлаждение шнека для того, чтобы сохранить основание шнека в охлажденном состоянии и улучшить коэффициент трения между смолой и сталью основания шнека. Также здесь следует отметить, что для того, чтобы найти какое-то средство улучшения подачи твердых материалов с низким коэффициентом трения, в начале шестидесятых в Европе была разработана технология с нарезной зоной питания. Эту технологию в США еще только предстоит полностью освоить, но она постепенно становится одной из значительных технологий обработки.
Переходная зона Переходная зона или зона сжатия традиционного экструдера это та часть, в которой происходит большая часть расплавления полимера. Это та часть экструдера, которая переходит от глубины питания до глубины дозирования, и в которой осуществляется воздействие на смолу заставляющее ее плавиться. В этой части шнека основание шнека постепенно становится тоньше, заставляя материал устремляться к стенкам цилиндра, где и происходит плавление. Пример 1: F =.006" / 1" = .006 дм/дм Самым существенным фактором, который должен приниматься во внимание при проектировании переходной зоны, является то, что кривая перехода должна как можно точнее соответствовать скорости плавления материала. Такие расчеты имеют решающее значение для того, чтобы максимально увеличить скорость работы экструдера и снизить степень износа, которому подвергаются компоненты шнека и цилиндра. Далее в нашей статье мы рассмотрим степень сжатия и вернемся к данному положению. Обычно зона перехода для шнека 24:1 L/D составляет между пятью и десятью диаметрами в длину в зависимости от типа обрабатываемого полимера.
Зона дозирования Зона дозирования или зона подачи шнека это та часть, в которой завершается плавление полимера и осуществляется прокачка для преодоления давления головки. Для того, чтобы оценить скорость прохождения материала в шнеке или осуществить обратный расчет глубины дозирования для примерного количества прохождения материала, которого хотят достичь, можно использовать простую формулу расчета, такую, как эта: Скорость = 2.3*D2*hm*SG*N Ур. 3 Скорость = пропускная способность (в фунтах в час) D = диаметр шнека (в дюймах) hm = глубина зоны дозирования (в дюймах) SG = относительный удельный вес полимера (г/куб. см) N = скорость шнека (в оборотах в минуту) Это преимущественно для применений с низким давлением головки.
Степень сжатия Термин «степень сжатия» является, пожалуй, самым неправильно понимаемым и неправильно используемым, но, тем не менее, широко используемым термином во всей шнековой терминологии. Большинство людей понимает термин «степень сжатия» так, как показано на Рисунке 2.
Рисунок 2.
Следовательно: Степень сжатия = Hf/Hm Ур. 4 Примером этого может быть следующая ситуация: у шнека 2.5" глубина зоны питания (hf) .300" и глубина зоны дозирования (hm) .100", тогда степень сжатия определяется как составляющая: Пример 2: CR = .300" / .100" = 3:1 Ур. 5 Но может также быть шнек 2.5" с глубиной зоны питания (hf) .450" и глубиной зоны дозирования (hm) = .150" a, и при этом степень сжатия составит: Пример 3: CR = .450" / .150" = 3:1 Ур. 6 У обоих шнеков степень сжатия 3:1, но они абсолютно разные. У первого из них будет значительно более высокая скорость сдвига, кроме этого у него будет скорость прохождения материала всего около 2/3. У второго шнека будет значительно более низкая скорость сдвига, у него будет более высокая скорость прохождения материала, и с его помощью можно будет обрабатывать материалы с более высокой чувствительностью к сдвигу. Кроме того, мы в данном случае даже не рассматривали кривую перехода. У двух шнеков могут быть различные степени сжатия; но, если длина переходной зоны различна, у них все же может быть одинаковая скорость плавления. При описании геометрии шнека, проследите, чтобы все детали были приняты во внимание. Точные параметры прокачивания можно рассчитать с помощью более сложных формул, но основным фактором для конструктора шнеков должно быть понимание параметров полимерного потока.
|