Переход от производства пятислойной пленки к семислойной или девятислойной может стать стимулом для развития за счет более высоких эксплуатационных характеристик или более низких затрат. Компании, занимающиеся обработкой стретч-пленок, привыкли к расширению рынка вдвое каждые пять лет. В период между 1985 г. и 1990 г. спрос вырос с 250 миллионов фунтов в год до 500 миллионов фунтов, а за период с 1990 г. до 1995 г. рынок взлетел до 1 миллиарда фунтов. Еще каких-нибудь пять лет тому назад, когда рынок наводнили пятислойные стретч-пленки, спрос на смолу продолжал расти в двухзначном выражении. Но на протяжении последних нескольких лет спрос на смолы для стретч пленки затормозился на 1.4 миллиарда фунтов. Стретч пленка это на 65% - 70% литая пленка, в основном, для механизированного обертывания, и на 30% - 35% экструзионно-раздувная пленка, в основном, для ручного обертывания товаров и нескольких специальных пленок с высокой устойчивостью к прокалыванию. Конкуренция в этом секторе производства пленок стала борьбой за долю рынка не на жизнь, а на смерть. Прибыль обработчиков зачастую составляет всего несколько десятых или сотых цента за фунт, а количество новых установок свелось всего к паре новых машин в год. Единственными североамериканскими компаниями-обработчиками, которые, по-видимому, развиваются и делают инвестиции, являются компании, которые производят новые пленки с большим числом слоев. Когда в середине девяностых появились пятислойные стретч-пленки, они заменили множество одно- и трехслойных пленок, созданных из гексен и/или октен LLDPE. Для этого потребовался четвертый экструдер и пятислойный фидблок, который позволял использовать менее дорогой бутен LLDPE, армированный тонкими слоями подложки из бывшего тогда новинкой металлоценового LLDPE. Типичной пятислойной структурой могла быть следующая: A-B-C-B-A с 10% поверхностными покрытиями из гексен LLDPE, 20% подповерхностными покрытиями из mLLDPE, и 40% ядром из бутенового LLDPE. По мере того, как увеличивалось количество слоев, установки для производства стретч-пленки становились все больше, а производительность все выше. Стандартом пять лет назад были пять 20-дюймовых рулона и три слоя. А теперь это шесть рулонов и пять слоев. На долю пятислойной стретч пленки теперь приходится 40% от всего количества растягивающейся пленки, производимой в Северной Америке, использование металлоценовой смолы выросло с нуля в 1995 г. до 12% от всего LLDPE, который используется для изготовления стретч пленки. Но mLLDPE довольно дорог, поэтому обработчики перешли на изготовление семислойных и девятислойных пленок, преимущественно для того, чтобы сделать возможным применение большего количества смол или бутен LLDPE и меньшего mLLDPE—а также, чтобы в некоторых случаях создавать пленки с более высокими эксплуатационными характеристиками. Например, все производители семислойной растягивающейся пленки говорят, что они могут заменить более толстые пленки с меньшим количеством слоев, не принося при этом в жертву удержание груза. 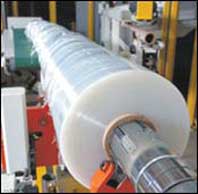
Производство более тонкой пленки без изменения параметров и сложные структуры позволяют сегодняшнему рынку стретч пленки развиваться дальше. Новейшая линия семислойной пленки компании Pliant дает 9,000 футов стретч пленки с толщиной 51 по сравнению со всего лишь 5000 футов традиционной пленки с толщиной 80. На протяжении последних нескольких лет все линии для производства литой стретч пленки, установленные в Северной Америке, были предназначены для изготовления пятислойной или более многослойной пленки. Они устанавливали все новые рекорды по количеству слоев: сначала семь, затем девять. В настоящее время обработчики и производители установок говорят уже об 11, 14, и даже 70 слоях. “Мы освоили промышленное производство для технологии с микрослойным фид-блоком для получения барьерных свойств, но одним из применений может также быть и растягивающаяся пленка. Мы можем производить слои толщиной в ангстрем [1 ангстрем = 0.0001 микрон] или с десятыми долями процента от толщины пленки”, - говорит Гэри Оливер, старший научный сотрудник компании Cloeren Inc. “Разработчики заинтересованы, но испытаний пока никто не проводит”. Все больше и больше слоев Большинство новых линий, производящих пленки с большим числом слоев, было приобретено новыми игроками рынка стретч-пленки, что в результате привело к перераспределению долей рынка. Chaparral Films из Морисвилля, Техас, была первой компанией, которая начала производить пятислойную стретч-пленку в 1994 г., и, по имеющимся данным, была первой, кто начал производить семислойную в 1996 г., хотя об этом никогда не сообщалось официально. По сведениям источников из компании Cloeren, которая создавала головки экструдеров и фидблоки, а также была инвестором, Chaparral производила и большее количество слоев на экспериментальной основе. (ITW Stretch Packaging Systems из Гленвью, Иллинойс, купила Chaparral в 1996 г., но она производит только пятислойные пленки.) Poly Rafia из Атлакомулко, Мексика, была еще одной компанией, которая в 1996 г. начала производить семислойную пленку, а в 2001 г. добавила к имеющейся и вторую линию. Когда компании Quintec Films Corp. из Шелбивилля, Теннесси, и Pinnacle Films Inc. из Шарлотта, Северная Каролина, начали промышленное производство осенью 1998 г., обе эти компании стали производить только семислойную пленку. Quintec получила Патент США #6,265,055 в июле 2001 г. на производство стретч пленки “с двумя внешними слоями и, по крайней мере, пятью внутренними слоями”. 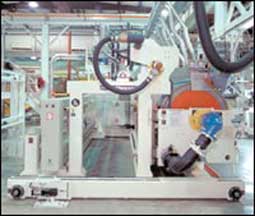
Для производства семислойной пленки с высоким содержанием mLLDPE с высокой производительностью необходимы охлаждающиеся вальцы самого крупного в Северной Америке диаметра. (Фото: Pliant) “При наличии достаточного количества экструдеров и слоев Вы сможете производить рентабельную высокопроизводительную пленку с металлоценами. Мы увидели такую рыночную возможность”, - говорит Уильям Райс, президент Pinnacle, в которой в апреле прошлого года была установлена вторая линия для производства семислойной пленки. “Большинство старых давно работающих на рынке игроков не может себе позволить добавлять новые высокотехнологичные мощности. Они не делают повторных инвестиций в линии по производству семислойной пленки”. Тем не менее, две компании, давно работающие на рынке обработки, с тех пор увеличили мощности по производству семислойной стретч пленки: Pliant Corp из Шаумбурга, Иллинойс, и AEP Industries Inc. из С. Хекенсека, Нью Джерси. Тем временем, компания Sigma Plastics Group, крупный производитель пленки для изготовления пакетов, работающий на рынке стретч пленки с 1994 г., установила первую в мире линию для производства девятислойной пленки в Белльвилле, Онтарио, в 2000 г. “За последние восемь лет мы, начав с нуля, получили 15% долю рынка. И мы здорово этим гордимся”, - говорит Пер Найлен, исполнительный вице-президент компании Sigma Stretch Film, которая базируется в Линдхерсте, Нью-Джерси. Совсем недавно, AmTopp из Ливингстона, Нью-Джерси, дочерняя компания Inteplast Group компании Formosa, заказала линию Battenfeld Gloucester для производства девятислойной пленки с доставкой в этом году на предприятие компании в Лолите, Техас. Одной из причин, по которой объем производства смолы для стретч-пленки не слишком сильно растет в настоящее время, является то, что пленка стала значительно тоньше. В 1985 г., стандартом считались 90 единиц (0.0009 дюйма). В настоящее время стандарт составляет от 65 до 80 единиц. Одним из основных последствий уменьшения толщины является снижение производительности старых линий. “Оборудование, которое использовалось для производства пленки на 1 мил при 3000 фунтов в час, сейчас производит пленку с толщиной 70 единиц, таким образом, мощность этих установок снизилась на 30%”, - отмечает Эндрю Кристи, президент Optex Process Solutions LLC в Фултоне, Нью-Йорк, консультант по растягивающимся пленкам. Единственным способом сделать так, чтобы более старая установка могла работать с современной производительностью, является использование новейшей намоточной установки, но компании, занимающиеся обработкой, склонны делать такие крупные инвестиции только при приобретении новых линий. Даже если общий вес пленки в фунтах и не увеличивается, количество поддонов, которые упаковывают в стретч пленку, по-прежнему стабильно увеличивается. Сегодняшняя пленка не только тоньше, она еще и лучше растягивается. В 1985 г. для обертывания стандартного поддона требовалось 12 унций пленки. Эта цифра снизилась до пяти унций в 1995 г., и до четырех унций в 2000 г., а это дает трехкратный рост в единицах, упакованных с использованием одного и того же фунта пленки. Pinnacle (единственная компания-производитель стретч-пленки, которая предоставила конкретную информацию об эксплуатационных характеристикахa для данной статьи) сообщает, что ее семислойная пленка Apex с толщиной 63 единицы дает от 360% до 370% окончательного растяжения на стандартном испытательном устройстве от компании Highlight Industries, производителя установок для упаковки в стретч-пленку. А это означает, что еще имеется запас для дальнейшего уменьшения толщины, особенно, для пленок с большим числом слоев. “Мы проводим испытания пленки, и обнаруживаем, что у большинства уровень окончательного растяжения свыше 350%, но средняя величина, которую реально применяли для упаковки поддонов, составляет, вероятно, лишь от 165% до 180%”, - говорит Курт Рименшнайдер, президент Highlight Industries. “Во многих случаях на сегодняшний день растягивающиеся пленки много лучше, чем оборудование для упаковки в такую пленку”. В пленку, которая в настоящее время имеется на рынке, можно упаковать намного больше поддонов, чем реально упаковывается, что потенциально только увеличивает избыток производственных мощностей. 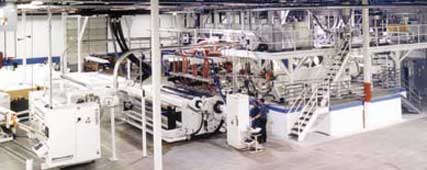
Pinnacle Films производит только семислойные высокопроизводительные стретч пленки с использованием mLLDPE. В прошлом году компания установила еще одну линию для производства семислойной пленки. О дальнейшем развитии в данном направлении сообщалось компанией Pliant на конференции Flexpo 2002, которая проходила в сентябре в Хьюстоне (спонсором была Chemical Market Resources из Хьюстона). Pliant сообщила, что она произвела в рамках исследовательской и проектной деятельности однослойную зкструзионно-раздувную пленку на 1 мил с растягиванием до 500% для того, чтобы осуществить оценку трех различных mLLDPE. Почему все больше слоев? Пленки с большим количеством слоев создаются только при производстве литой стретч-пленки для машинной упаковки. Экструзионно-раздувная стретч пленка для ручной упаковки производится с одним или тремя слоями из смесей гексен/октеновых LLDPE с использованием дорогостоящих прилипающих добавок, которые не используются при производстве литых пленок. Пленки с большим количеством слоев, как правило, не содержат большего количества различных материалов. Вместо этого создаются дополнительные слои за счет расщепления в фидблоке одного потока смолы на тонкие отрезки, которые укладываются стопками или же перемежаются со слоями потока другой смолы. Эта технологии обычно используется для экструзии листа для получения более однородного распределения смолы. “Соэкструзия тонких чередующихся слоев может повысить устойчивость к образованию проколов”, - говорит Оливер из компании Cloeren. “Экструзия более тонких металлоценовых смол на самом деле делает их более устойчивыми к расщеплению: это так же, как со стеклом, если оно достаточно тонкое, то оно гибкое”. “Девятислойная пленка напоминает многослойную фанеру”, - говорит Найлен из компании Sigma. “При использовании девяти слоев вместо пяти мы получаем более высокие параметры предварительного натяжения, устойчивости к прокалыванию, а также устойчивости к истиранию”. Чередование тонких слоев mLLDPE также позволяет шире использовать разнообразные или бутеновые LLDPE и уменьшить количество необходимого mLLDPE. В семислойной пленке с тремя слоями из mLLDPE содержание металлоцена может уменьшиться до 33% по сравнению с 40% mLLDPE, которые наносятся на два слоя типичной пятислойной растягивающейся пленки. 
Высокопроизводительные семислойные пленки могут растягиваться значительно больше того растяжения, которое им может обеспечить большинство упаковочных установок, даже при таком грузе с выступающими углами. (Фото: Highlight Industries) Хотя имеются хорошие аргументы в пользу создания в фид-блоке множества слоев из одного потока смолы, существуют также и аргументы в пользу использования большего количества экструдеров. “Соэкструдирование слоев из одной смолы с помощью двух экструдеров повышает пропускную способность линии, но не оказывает никакого воздействия на свойства пленки”, - поясняет Оливер. “Линия с высокой производительностью с двумя экструдерами на 4.5 дюйма вместо одного экструдера на 6 дюймов также дает гибкость для производства сложных или простых продуктов, также значительно проще управлять температурным режимом при наличии экструдера на 4.5 дюйма, чем при экструдере на 6 дюймов”. Семислойные стретч пленки компании Pliant можно производить с использованием трех, четырех, пяти или шести экструдеров. На первой линии компании в Льюисбурге, Теннессии, имеется пять экструдеров и небольшая шестая установка, которая производит экструзию боковой кромки из отходов обрезки. Новейшая установка Pliant для производства семислойной пленки, которую установили три месяца тому назад, снабжена четырьмя экструдерами. Наличие вставки заранее определенного размера для фидблока позволяет производить семь слоев из трех или четырех различных полимеров. В установке также используются охлаждающие вальцы, которые считаются самыми большими в Северной Америке для производства литой растягивающейся пленки. По сообщениям Pliant, большие вальцы быстрее охлаждают пленку, еще больше увеличивают устойчивость к прокалыванию и прилипание. Первая высокопроизводительная семислойная пленка Pliant, названная R-122, была представлена в 2001 г., но ее промышленное производство началось в полном объеме только в 2002 г. Она была разработана для повышения прочности и снижения уровня шума пятислойной пленки компании Pliant OPTX. R-122 высококлассный продукт с наибольшим для продукции Pliant содержанием mLLDPE (более 50%), который позволяет осуществлять уменьшение толщины, а также получать высокие соотношения предварительного натяжения. Тем не менее, это одна из наиболее хорошо продающихся стретч пленок от Pliant среди марок с толщиной 51 и 63 единицы. Тонкость R-122 дает потребителям больше полезной длины на ту же самую массу рулона: 9000 футов для рулона пленки R-122 с толщиной 51 единица и 7250 футов для рулона пленки R-122 с толщиной 63 единицы, в то время как в стандартном рулоне с толщиной 80 единиц только 5000 футов. В Pliant говорят, что пленки с толщиной 51 и 63 единицы могут иметь грузы на поддоне C (неупакованные в коробки грузы нерегулярной формы с большим количеством выступов), и все же превосходить по эксплуатационным характеристикам некоторые из наиболее прочных пленок с толщиной 70 и 80 единиц, имеющихся на рынке. Разработка R-122 заняла более года, поскольку первоначальная скорость производства была слишком низкой, чтобы рассматривать ее как достаточную для запуска в промышленное производство. Это отрицательно влияло на пропускную способность, и обработка была более сложной при более высоком содержании mLLDPE, поэтому в Pliant изменили технологию и рецептуру смолы.
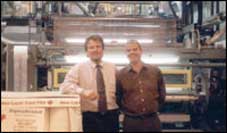
При работе первой в мире линии для производства девятислойной стретч пленки на Sigma Stretch Films не используется mLLDPE. Дополнительное количество слоев позволяет получать промышленную пленку с меньшими затратами. При изготовлении высококлассной стретч-пленки Apex компании Pinnacle, которая была представлена на рынок в 2000 г., также используются семь слоев и mLLDPE для получения малой толщины. “Мы можем заменить стандартную стретч пленку с толщиной 80 единиц пленкой с толщиной 63 единицы. А для небольших грузов мы можем довести толщину до 55 единиц”, - говорит Райс из компании Pinnacle.
Линия для производства семислойной стретч пленки компании Black Clawson в Квинтеке работает с пятью экструдерами и фидблоком Ultraflow от Extrusion Dies Industries с золотником переключателя для изменения последовательности слоев. В Black Clawson говорят, что типичная структура из семи слоев может включать: 5% - 15% поверхностный прилипающий слой, 5% - 10% подповерхностный рабочий слой, 15% - 20% внутренний рабочий/подпиточный слой, 40% - 50% основное/подпиточное ядро, 5% - 10% внутренний рабочий/подпиточный слой, 5% - 10% подповерхностный рабочий слой, и 2% - 15% поверхностный прилипающий слой. Не всегда при производстве пленок с большим количеством слоев используют mLLDPE. Sigma их не использует в своих девятислойных пленках, отмечая, что предел прочности при раздирании в поперечном направлении ниже при наличии mLLDPE, чем при использовании обычных гексен/октеновых смесей. AmTopp также не планирует использовать mLLDPE при производстве своих девятислойных пленок. AEP Industries также старается обойтись без mLLDPE. AEP переоборудовала свою существующую линию с четырьмя экструдерами, и добавила фидблок для производства семислойной пленки. Первым семислойным продуктом стал EXRW (Excaliber Roll Wrap)—пленка большого размера на 3 мил для упаковки рулонов бумаги, новый рынок для односторонних липких упаковок. Защита гигантских рулонов бумаги требует жесткости поверхности, но небольшого растяжения. Новейшие пяти- и семислойные пленки от AEP EXP (Excaliber Plus), представляют собой высокопрочные пленки, предназначенные для изменения толщины на высокоскоростных автоматизированных установках для обертывания в стретч пленку. Как отмечает Майкл Хилдрет, технический менеджер АЕР, пленкой EXP можно оборачивать при скоростях до 60 оборотов в минуту, в то время как типичной скоростью для машинного обертывания являются 20 оборотов в минуту, а 30 оборотов в минуту считаются высокой скоростью. 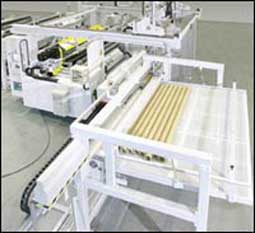
Автоматизированные загрузка ядра, выгрузка рулона и упаковка в коробки более распространены в Европе, где стоимость труда выше. (Фото: SML) При использовании своей линии для производства девятислойной пленки Sigma сосредоточила усилия на менее дорогих промышленных пленках. Ее система Battenfeld Gloucester использует четыре экструдера, а также готовку экструдера и фидблок от Cloeren. Подповерхностный слой B, ядерный C, и подповерхностный D расщепляются на чередующиеся слои: A-B-C-B-C-D-C-D-A.
Непрерывные и с высокой производительностью Непрерывная эксплуатация и высокая производительность безотказной работы имеют решающее значение для увеличения прибыли при производстве растягивающейся пленки. Онлайновая регулировка ширины в сочетании с изменениями путей потоков в фидблоке очень существенны для изменения последовательности слоев в процессе обработки. Линии по производству растягивающейся пленки работают со все более высокой скоростью для преодоления конкуренции. “Некоторые производители могут работать при 1700 - 1800 футах в минуту и 4100 фунтах в час”, - говорит Роберт Мёллер, менеджер по продукции для экструзионных систем компании Black Clawson. В свою очередь более высокая производительность требует и более быстрого наматывания, и более высокого уровня автоматизации. Последние намоточные установки для растягивающейся пленки работают при скорости до 1400 футов в минуту по сравнению с примерно 600 футами в минуту, которые дают обычные намоточные установки для растягивающейся пленки. Новейшие намоточные установки производят комплект от шести до десяти рулонов ручного обертывания каждые 50 - 60 секунд, и такое же количество для машинного обертывания (с большими диаметрами) каждые три-пять минут в зависимости от толщины. При таких молниеносных скоростях необходимы автоматизированное извлечение рулонов и заправка стержней. По крайней мере, три компании из США инвестировали средства в полностью автоматизированную загрузку коробок с экструзионно-раздувной пленкой для ручного обертывания. Компания AEP была первой в начале девяностых, за ней последовало предприятие в Дэнвилле, Виргиния, компании Intertape Polymer Group, и, по крайней мере, одно предприятие базирующейся в Миннеаполисе компании Tyco Plastics. При машинном обертывании, при котором скорость ниже, обычно используют частичную автоматизацию. Полностью автоматизированная загрузка коробок более распространена в Европе, где стоимость рабочей силы выше. В начале девяностых линии для производства растягивающихся пленок также стали шире для увеличения пропускной способности. Для того, чтобы уменьшить образование шейки из-за очень широких головок экструдера, обработчики используют вакуумную камеру с двумя отделениями, а также крепления краев для того, чтобы удерживать пленку при контакте с охлаждающими вальцами. Намоточные установки также стали шире. Когда Black Clawson создает вальцы намоточных установок шире 120 дюймов, она использует центральный стержень из двух частей с центральной опорой. Это позволяет одной намоточной установке с трехдюймовыми стержнями наматывать широкое полотно на высокоскоростных линиях. С другой стороны, последние намоточные установки от Battenfeld Gloucester и Egan Div компании Davis-Standard сконструированы как двойные намоточные установки, каждая с более короткими стержнями, которые, как сообщается, обладают большей стабильность, хотя затраты на оборудование и материально-техническое обслуживание с ними выше. Экструзионно-раздувная стретч пленка При производстве экструзионно-раздувной стретч пленки до сих пор не использовались ни mLLDPE, ни большое количество слоев, хотя разработки в области ориентации могли бы создать возможности для использования большего количества слоев и повышения эксплуатационных характеристик. Осенью прошлого года компания Battenfeld Gloucester представила входящее в состав линии устройство для ориентации MD, которое растягивает пленку на 200% - 300%. Производительность при производстве экструзионно-раздувной стретч пленки обычно ограничена необходимостью охлаждения, но эта разработка позволяет экструдеру перекачивать то же количество фунтов в час при производстве в два, а то и в три раза большей длины (в футах в час) стретч пленки. В экспериментальной установке для MDO компании Gloucester используется обертывание в виде буквы S двумя вальцами предварительного нагревания, по одному для нагревания каждой из сторон пленки. В установке также имеются обертывание в виде буквы S двумя каучуковыми тянущими вальцами, которые вращаются в три-четыре раза быстрее, чем вальцы предварительного нагревания для растягивания пленки. Два нагретых вальца для отжига восстанавливают часть растягивания. И, наконец, два охлаждающих вальца запирают остаточное растягивание. Производство ориентированной монослойной пленки находится под вопросом из-за того воздействия, которое могут оказывать высокие уровни предварительного растягивания, вызывающие помутнение из-за миграции добавок на поверхность пленки. Для того, чтобы охарактеризовать это воздействие, которое хорошо объяснимо в случае с многослойной пленкой с прилипающим поверхностным слоем, в настоящее время проводятся исследования. Упаковка силоса в стретч пленку и крупные кубы мусора являются относительно новыми нишами для использования экструзионно-раздувной стретч пленки, разработанной компаниями AEP, Tyco, и Sigma на протяжении последних трех лет. Для силосования предпочтительнее использование трехслойной пленки для предотвращения разложения, а биаксиальное растягивание придает пленке большую устойчивость к прокалыванию стебельками сена. Антикоррозийная растягивающаяся упаковка, которая называется VCI (парообразный ингибитор коррозии), является продуктом для новой ниши рынка, и используется для защиты железных прутьев и прочих металлических продуктов от ржавчины. VCI трудно производить, поскольку добавка ингибитора коррозийная. Производство более тонкой пленки без изменения параметров и сложные структуры позволяют сегодняшнему рынку стретч пленки развиваться дальше. Новейшая линия семислойной пленки компании Pliant дает 9,000 футов стретч пленки с толщиной 51 по сравнению со всего лишь 5000 футов традиционной пленки с толщиной 80. Для производства семислойной пленки с высоким содержанием mLLDPE с высокой производительностью необходимы охлаждающиеся вальцы самого крупного в Северной Америке диаметра. (Фото: Pliant) Pinnacle Films производит только семислойные высокопроизводительные стретч пленки с использованием mLLDPE. В прошлом году компания установила еще одну линию для производства семислойной пленки. Высокопроизводительные семислойные пленки могут растягиваться значительно больше того растяжения, которое им может обеспечить большинство упаковочных установок, даже при таком грузе с выступающими углами. (Фото: Highlight Industries) При работе первой в мире линии для производства девятислойной стретч пленки на Sigma Stretch Films не используется mLLDPE. Дополнительное количество слоев позволяет получать промышленную пленку с меньшими затратами. Автоматизированные загрузка ядра, выгрузка рулона и упаковка в коробки более распространены в Европе, где стоимость труда выше. Йен Х. Шут, старший редактор Источник: Plastics Technology Подробнее с анализом рынка конкретных видов пленок – оценкой спроса, географией размещения производство, анализом конкурентной среды. Возможностями замещения импортных поставок, - можно познакомиться в отчете Академии Конъюнктуры Промышленных Рынков «Рынок полимерных пленок в России» |