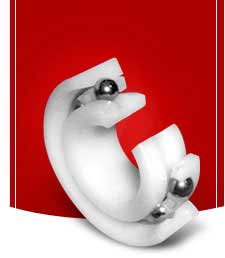 ПЭЭК относятся к суперконструкционным полимерам, температура изгиба которых превышает 200 оС [1]. У ПЭЭК эта температура достигает 250 - 320 оС. Однако ПЭЭК, выпускаемые различными фирмами, имеют неодинаковые физико-механические показатели. Так, температура изгиба ПЭЭК марки "Виктрекс" составляет 160 оС, а ПЭЭК, армированного углеволокном (30%), - 315 оС; температура возможного длительно использования как гомополимера, так и полимера, содержащего 30% углеволокна, достигает 240 оС [1]. Известно, что ПЭЭК являются кристаллическими полимерами, поэтому была подробно исследована кинетика кристаллизации композиций на основе ПЭЭК с содержанием углеродного волокна 11-70% [2 - 8]. В основном процесс кристаллизации изучали методами дифференциально-сканирующей калориметрии, поляризационной микроскопии и дифракции рентгеновских лучей. Установлено [2], что с увеличением содержания углеволокна кристаллизация ПЭЭК протекает при меньшей степени переохлаждения. Это свидетельствует о том, что волокна выступают в качестве зародышей кристаллизации; в присутствии углеволокна снижается энергия активации процесса кристаллизации и степень кристалличности [7, 8]. На поверхности углеродного волокна образуется транскристаллическая структура ПЭЭК, а с увеличением продолжительности нагрева образцов уменьшается количество сферолитов в полимерной матрице и возрастает содержание таких структур. Полагают [2], что при нагреве протекают конкурирующие процессы зародышеобразования кристаллитов в объеме полимерной матрицы и на поверхности наполнителя. Скорость охлаждения образцов не оказывает влияния на этот процесс. Транскристаллическая структура ПЭЭК обеспечивает повышение прочности композиционного материала. Анализ структуры поверхности разрушения угленаполненных композиций на основе ПЭЭК показал [9], что процесс разрушения включает две стадии - медленную (стабильную) и быструю (нестабильную), а образующиеся при этом поверхности разрушения имеют различную структуру. Энергия разрушения полимерного связующего составляет 44%, а углеволокна - 10% от общей энергии разрушения. Образцы таких композиций, охлажденные с высокой скоростью, обладают большей молекулярной подвижностью в застеклованном состоянии [10]. Физико-механические характеристики композиции на основе ПЭЭК с углеволокном так же, как и гомополимера, определяются степенью кристалличности [11]. Свойства композиций при разрыве и сжатии чувствительны к их предыстории, а прочность при сдвиге, модуль упругости при растяжении и ударная прочность зависят только от степени кристалличности. В то же время на прочность при разрыве таких композиций при температуре 60 - 93 оС не влияют степень кристалличности и содержание влаги в образцах [12]. Теплофизические свойства угленаполненных композиций на основе ПЭЭК определяются тепловым режимом переработки [13]. На процесс кристаллизации композитов оказывают влияние условия плавления. Кристаллизация протекает с большей скоростью при 230 оС, при этом образуется микросферолитная структура, обеспечивающая оптимальные физико-механические показатели композиций. Образцы ПЭЭК, армированные стекловолокном (20 и 30%) или углеволокном (30%), имеют ярко выраженную слоистую структуру [14]. Существенное влияние на физико-механические характеристики композиций оказывают особенности их микроструктуры. При введении в матрицу ПЭЭК 20 и 30% стекловолокна или 30% углеволокна несколько повышаются прочность и трещиностойкость композиционного материала по сравнению с соответствующими показателями чистой матрицы [15]. При исследовании процесса плавления и релаксационных свойств ПЭЭК и стеклонаполненных композиций на его основе установлено [16], что в случае кристаллизации при отжиге предварительно закаленных образцов их температура стеклования (tc) возрастает на 7 оС по сравнению с tc образцов, закристаллизованных непосредственно из расплава, и на 17 оС по сравнению с tc закаленных образцов. Наиболее распространенным методом переработки армированных волокнами композиций на основе ПЭЭК является литье под давлением [17 - 20]. Из этих композиций изготавливают [17] снарядные стабилизаторы и крыльчатки насосов, применяемых в химической промышленности, которые обладают высокой коррозионной стойкостью при повышенной температуре [20]. Срок службы таких композиций составляет 18 месяцев, тогда как у композиций на основе эпоксидной смолы и стекловолокна, используемых в настоящее время, он не превышает 2 мес. С применением в качестве наполнителей различных проводящих волокон (графитовые волокна, недеформируемые стальные волокна, чешуйки никеля и покрытие из никеля) получают [18] высокопроводящие композиции достаточно низкой стоимости. При исследовании процесса развития усталостных трещин в свежеприготовленных и отожженных (в течение 5 сут) при 150 оС (вблизи tc) и при 325 оС (вблизи температуры плавления - tпл) образцах установлено [19], что из-за резкого охлаждения структура наружных слоев образцов существенно отличается от структуры сердцевины. Отжиг композиций, особенно при повышенной температуре, способствует выравниванию характеристик слоев. Образцы, армированные стекловолокном, ведут себя аналогично неармированному ПЭЭК, тогда как при армировании образцов углеволокном развитие усталостных трещин заметно замедляется. Вероятно, это объясняется большей прочностью связи волокна с полимерной матрицей. Разработан способ изготовления композиционных материалов на основе ПЭЭК и углеродных волокон [21], позволяющий расположить волокна матрицы вокруг армирующих углеволокон и, контролируя объемное содержание связующего, получать трехмерную оплеточную конструкцию, обладающую повышенной стойкостью к ударным воздействиям. В таких материалах степень кристалличности матрицы ПЭЭК достигает 40%, что повышает уровень адгезионного взаимодействия между углеродным волокном и полимерной матрицей и обеспечивает высокую стойкость материала к ударным воздействиям. Для получения композиционных материалов на основе графитонаполненного ПЭЭК пригодны также методы вибрационной, индукционной, контактной сварки, склеивания и клепки [22, 23]. Выбор метода соединения полимерной матрицы и наполнителя зависит от назначения композиционного материала. Склеивание является наиболее простым методом, однако он требует специальной подготовки поверхности и не обеспечивает высокой прочности связи. Наибольшая прочность соединения достигается при вибрационной сварке, но ее не рекомендуется использовать при изготовлении крупногабаритных деталей и угловых стыков. Технология контактной сварки недостаточно разработана и поэтому применяется, как правило, для узких длинных стыков и при малой поверхности сварки. Методом сухого смешения порошкообразного ПЭЭК и никеля (10 объемн. %) получают [24, 25] материалы с повышенной прочностью, проявляющие более низкий модуль упругости по сравнению с ненаполненным полимером. Основными недостатками угленаполненных термопластов, в том числе ПЭЭК, являются их сравнительно низкие ударная вязкость при расслоении и стойкость у ударным воздействиям в направлении, перпендикулярном плоскости материала [26]. Армирующие волокна в значительной степени препятствуют развитию пластической деформации в полимерной матрице. Разрушение термопластичных армированных композиций при изгибе первоначально носит хрупкий характер и наблюдается, как правило, в слоях, подвергающихся сжатию, что объясняется вспучиванием слоев пластичного материала. Дальнейшее расслоение композиций обусловлено сдвиговыми напряжениями, а не растяжением. Изменяя тип волокна, можно варьировать свойства композиций на основе ПЭЭК [27]. Высокими физико-механическими показателями обладает ПЭЭК, армированный высокопрочными углеродными волокнами (60 объемн. %), в котором практически отсутствуют поры. Наиболее эффективными наполнителями для ПЭЭК являются высокомодульные углеродные волокна [28], а их оптимальное содержание, обеспечивающее максимальную прочность при разрыве композиций, составляет 40%. Модуль упругости при растяжении таких композиций монотонно возрастает с увеличением содержания волокон. Композиции, полученные методом пултрузии, обладают лучшими физико-механическими свойствами по сравнению с экструдированными образцами. Подробно исследованы трибологические характеристики стекло- и угленаполненных композиций на основе ПЭЭК [29 - 31]. Установлено, что с увеличением количества волокна в композиции скорость износа материала снижается [29] за счет повышения его жесткости. Скорость усталостного износа ПЭЭК, армированного стекловолокном, выше, чем полимера с углеродным волокном. Это обусловлено низкой теплопроводностью стекловолокна. Коэффициент трения при усталостном износе композиций со стекловолокном повышается при увеличении содержания стекловолокна, тогда как у композиций с углеродным волокном он в этих условиях снижается, что объясняется возрастанием вклада углеволокна, имеющего низкий коэффициент трения. Износостойкость угленаполненных ПЭЭК можно повысить путем введения в них 2% силоксановых добавок, обеспечивающих эффект самосмазывания трущихся поверхностей в зоне контакта [32]. При оценке химической стойкости угле- и стеклонаполненных ПЭЭК [33, 34] в таких средах, как этиленгликоль, газолин, трихлорэтилен, машинное масло, авиационное топливо, гидравлическая жидкость, противообледенительный состав и вода, установлено, что угленаполненные полимеры сохраняют высокую механическую прочность после длительной выдержке в агрессивных средах [34]. При температуре до 142 оС и времени выдержки до 7 сут наибольшей химической стойкостью обладают ПЭЭК с содержанием стекловолокна 30%. Исследование химической люминесценции ПЭЭК, армированного углеволокном, в течение 5 - 44 ч в атмосфере кислорода при 110 оС показало [35], что для ПЭЭК спектральное распределение практически постоянно. Полимерные композиционные материалы имеют более низкую температуру эксплуатации по сравнению с металлическими, керамическими и стеклонаполненными керамическими материалами, но обладают более высокой ударной прочностью [36]. Это, в частности, позволяет использовать угленаполненные ПЭЭК для изготовления хвостовой плоскости самолетов [37], конструкций для авиакосмической техники [34]. Возможность применения таких композиций в авиационной промышленности определяется [38] свойствами полимерной матрицы, природой взаимодействия волокна с матрицей и микроструктурой образцов. Композиционные материалы характеризуются статистическим распределением волокон. Степень кристалличности полимерной фазы составляет 35%, а в ее структуре присутствуют сферолиты диаметром 2 мкм. Размер сферолитов влияет на физико-механические свойства композиций. К недостаткам ПЭЭК относятся высокая стоимость, низкая текучесть и недостаточно высокая tc [39]. Поэтому их сплавляют с другими полимерами [40, 41]. Так, при введении 50% полиэфиримида (ПЭИ) в ПЭЭК его tc возрастает до 180 оС [39], при этом степень кристалличности полимера не изменяется. Сплавлением ПЭЭК и полиэфиркетона (ПЭК) получают материалы с заданными значениями tпл и tc [39, 42], которые зависят от количества кетонных и эфирных групп в полимере. Смеси ПЭЭК с ПЭК, приготовленные соосаждением из 1%-ных растворов в дихлоруксусной кислоте, кристаллизуются [42] раздельно в условиях, близких к равновесным. Аналогичное явление наблюдается при охлаждении смесей из расплава, Однако быстрая закалка расплавов может обеспечивать частичную сокристаллизацию компонентов смесей. Смеси этих полимеров имеют одну tc, но из-за малой разницы в значениях tc гомополимеров (10 оС) невозможно сделать однозначный вывод о их совместимости. ПЭЭК на основе фенолфталеина совместим с полигидроксиэфиром диана и полисульфоном, о чем свидетельствует наличие одной tc у смеси этих полимеров, полученной методом полива из общего раствора в хлороформе [43]. Композиции на основе смеси ПЭЭК и полиэфирсульфона (ПЭС) обладают [44] хорошими физико-механическими свойствами, характерными для ПЭС при температуре до 200 оС, в сочетании с низкой воспламеняемостью, малым дымовыделением, высокой прочностью и коррозионной стойкостью ПЭЭК, применяемого при температуре до 300 оС. Оба компонента композиции стойки к действию рентгеновского, - и -излучения. Из таких композиций изготавливают штекеры, разъемы, платы, сердечники и другие изделия для электротехники, а из армированного стекловолокном материала литьем под давлением получают изоляторы для мощных теристоров и диодов. Исследовано [45] влияние способа получения на термические и вязкоупругие свойства композиций на основе смеси ПЭЭК и ПЭС. По первому способу смесь приготавливали на стадии синтеза компонентов с последующим выделением и прессованием композиции при 300 оС. Второй способ заключался в переработке на литьевой машине при 350 оС смеси порошкообразных ПЭЭК и ПЭС. По первому способу получали однофазную композицию, по второму - двухфазную. Температура начала резкого снижения динамического модуля упругости в первом случае на 70 оС выше, чем во втором. Температура прессования первой композиции составляет 300 оС, что на 80 оС ниже, чем чистого ПЭЭК. Однако при отжиге или переработке первой композиции при температуре выше tпл ПЭЭК (340 оС) наблюдается фазовое разделение смеси. Это может быть связано с тем, что в первой композиции, перерабатываемой при температуре 300 оС, макромолекулы ПЭЭК в смеси с молекулами ПЭС не обладают подвижностью, необходимой для фазового разделения, вследствие чего предотвращается расслоение системы. При выдержке в вакууме потеря массы композиций на основе смеси угленаполненных ПЭЭК и полифениленсульфида (ПФС) составляет < 0.1% [46], а количество выделяющихся летучих веществ - < 0.01%, что соответствует требованиям космической техники. Степень равновесного влагопоглощения образцов при 71 оС значительно меньше, чем эпоксидных углепластиков, и составляет 0.15% для ПЭЭК и 0.2% для ПФС. Композиции отличаются также высокой демпфирующей способностью и стойкостью к циклическому воздействию температур в интервале от -157 до 121 оС. Указанные композиции обладают более высокими физико-механическими показателями благодаря повышенной адгезионной прочности на границе раздела фаз. Эти композиции используют для изготовления космических параболических антенн и трубчатых конструкций. ПЭЭК, армированные различными наполнителями, применяют для получения слоистых композиционных материалов [47 - 56]. В многослойные композиции на основе ПЭЭК могут быть введены и другие полимеры, в частности ПЭС [49]. Оптимальный режим переработки однонаправленных слоистых композиционных материалов на основе ПЭЭК следующий [52]: температура формования - 370 оС, время формования расплава - >5 мин, давление формования - 0.4 - 4.2 МПа. Сравнение усталостных свойств многослойных композиционных угленаполненных (54 объемн. %) пластиков на основе ПЭЭК и эпоксидных смол в зависимости от температуры и влажности среды показало [47], что более высокая вязкость при разрушении ПЭЭК и его повышенная адгезия к углеродному волокну обеспечивают получение композиционных материалов с большей энергией разрушения, влияющей на их усталостные характеристики. Более вязкая матрица ПЭЭК, чем эпоксидной смолы, предотвращает развитие локальных процессов разрушения углеродных волокон и повышает их усталостную выносливость. Критическая скорость высвобождения энергии деформирования при расслоении однонаправленных углепластиков на основе ПЭЭК в 10 и больше раз превышает соответствующий показатель аналогичных материалов на основе термореактивных связующих [55]. Усталостные свойства слоистых угленаполненных композиций на основе ПЭЭК не зависят [51] от числа слоев и толщины образца, а также от типа испытательной машины и характера нагружения. В общем случае чем выше частоты циклического нагружения, тем ниже усталостная выносливость материала, т.е. чем больше роль матрицы ПЭЭК, тем сильнее зависимость усталостных свойств слоистых композиционных материалов от частоты нагружения. При частоте нагружения >0.5 Гц саморазогрев материала существенно искажает экспериментальные данные. Разработан способ получения трехмерных слоистых композиционных материалов на основе угленаполненных ПЭЭК [53], отличающийся от традиционных способов тем, что предварительно уложенные слоями углеродные и полимерные волокна прошиваются Z-образным швом, обеспечивающим связь слоев по всем трем направлениям. Такие композиционные материалы значительно превосходят по стойкости к ударным воздействиям традиционные слоистые композиционные материалы на основе ПЭЭК. Другой нетрадиционный метод получения слоистых однонаправленных композиционных материалов на основе угленаполненного ПЭЭК [54] предусматривает использование непрерывной точечной сварки. Этим методом можно изготавливать материалы, не уступающие по физико-механическим свойствам материалам, получаемым традиционным способом, однако в них возможно образование дефектов в виде полостей и включений, а также наличие локальных нарушений структуры и остаточных напряжений. Существенным недостатком изделий из ПЭЭК является высокий коэффициент трения [57]. Для его снижения в композиции на основе ПЭЭК вводят полиэтилентерефталат, при этом трибологические свойства обоих полимеров улучшаются. Работоспособность указанных композиций при трении под нагрузкой сохраняется, однако их износостойкость несколько снижается. Оптимальный состав композиционных материалов определяется их назначением и зависит от технологии получения материала, качества исходных полимеров и внешних условий. Оптимальное массовое соотношение ПЭЭК:ПЭТФ при изготовлении контактных узлов из композиций на металлической подложке, работающих без смазки, составляет 90:10. В состав другого композиционного фрикционного материала, используемого в производстве подшипников, входит 60-90% ПЭЭК, 7.5% политетрафторэтилена (ПТФЭ), 2.5% графитового порошка и 10% бронзы [58]. Детали подшипников из такого материала отличаются высокой усталостной выносливостью, низким коэффициентом трения и малой степенью износа при испытаниях на стендовом оборудовании. С увеличением длины волокон (стеклянных и углеродных) в композициях на основе смеси ПЭЭК и ПЭТФ возрастает их прочность и жесткость [59], однако для таких композиций характерна анизотропия свойств. Для предотвращения ухудшения свойств композиций вследствие отслаивания волокон от полимерной матрицы при смачивании водой применяют специальные замасливатели. Введение на 100 масс. ч. ПЭЭК 50-250 масс. ч. специальных фенолоформальдегидных смол позволяет получать композиции с хорошими трибологическими свойствами, при этом их прочность существенно не снижается [60]. По физико-механическим характеристикам наполненные композиции на основе ПЭЭК превосходят аналогичные традиционные композиции на основе эпоксидных смол, ПЭС, полиамида марки ПА-6 и ПЭИ [61-65], однако переработка композиций на основе ПЭЭК затруднена [62] вследствие кристаллической структуры полимерной матрицы. Испытания на стойкость к ударным воздействиям угленаполненных композиций на основе ПЭЭК и эпоксидных смол показали [65], что при низко скорости нагружения большей ударной прочностью обладают композиции на основе ПЭЭК. Эти композиции отличаются и большей остаточной прочностью при ударном сжатии. Для повышения физико-механических характеристик слоистых композиционных материалов на основе ПЭЭК слои на внешней поверхности пластиков располагают под углом друг к другу. Такой же эффект достигается и в случае кольцевых образцов. Прочность при сжатии однонаправленных слоистых композиций на основе ПЭЭК выше, чем аналогичных композиций на основе ПЭС, и составляет 1400 и 615 МПа соответственно [64]. Значения данного показателя для композиций на основе ПЭЭК и эпоксидных смол близки. Сравнительное исследование свойств угленаполненных композиций на основе ПЭЭК и эпоксидных смол для оценки возможности их эксплуатации в околоземном и дальнем космическом пространстве показало [63], что композиции на основе ПЭЭК более стойки к облучению протонами, электронами и УФ-лучами, а также к циклическому воздействию температур в интервале от -156 до 180 оС и термоудару при температуре жидкого азота и гелия. Потеря массы этих композиций при выдержке в вакууме не превышает 0.02%, тогда как у эпоксидных композиций она составляет 0.35 - 0.9%. Стойкость к действию кислорода воздуха композиций на основе ПЭЭК несколько выше, чем эпоксидных композиций. В последнее время разработаны новые аналоги ПЭЭК. Так, в качестве термопластичного связующего для получения композиционных материалов предложено [66] использовать полиэфирдикетон с tс = 180 оС. Угленаполненные (60%) композиции на основе этого полимера обладают высокими физико-механическими характеристиками при 23 и 93 оС: их прочность при изгибе при этих температурах достигает 1620 и 1394 МПа, при сдвиге - 117 и 97 МПа соответственно, при сжатии - 1393 МПа, т.е. данные показатели не ниже, чем у композиций на основе ПЭЭК и эпоксидных смол. Указанные преимущества композиций на основе полиэфирдикетона в сочетании с их хорошими технологическими свойствами и высокой стойкостью к ударным воздействиям позволяют рекомендовать эти полимеры для применения взамен традиционных эпоксидных смол. Следует отметить, что, несмотря на ценный комплекс физико-механических характеристик ПЭЭК и композиций на его основе, возможно их дальнейшее улучшение. Так, для модифицирования ПЭЭК в него вводят элементарную серу в количестве 0.25 - 2% [67]. Такие композиции до начала старения кристаллизуются быстрее, чем немодифицированные композиции. Это объясняется уменьшением молекулярной массы полимера из-за разрыва цепей и увеличением числа зародышей кристаллизации в присутствии серы. Процесс сшивания, протекающий при тепловом старении образцов, повышает вязкость полимера, вследствие чего скорость кристаллизации модифицированного ПЭЭК снижается по сравнению со скоростью кристаллизации контрольного образца. Подтверждена [68] возможность поперечного сшивания ПЭЭК с помощью элементарной серы. В отличие от обычных способов структурирования, осуществляемых только в расплаве ПЭЭК при температуре 450 оС, данный метод позволяет проводить процесс при любой температуре в интервале между tс и tпл полимера. Структурирование подтверждается [69] повышением tс, смещением максимума на кривой зависимости тангенса угла механических потерь от температуры, а также снижением деформации ползучести при температуре выше tс. Возможно структурирование полимера как в твердом состоянии, так и в расплаве [69]. Скорость процесса зависит от температуры отжига. При структурировании улучшаются физико-механические характеристики ПЭЭК, однако его степень кристалличности при этом не изменяется и составляет 40% [68]. Разработан [70] метод модифицирования композиционных материалов на основе фенолфталеинового ПЭЭК и аттапульгита, заключающийся в ацетилировании бутиральдегидом или бензальдегидом поверхности наполнителя (аттапульгита). При этом возрастают прочность и относительное удлинение при разрыве, а также модуль упругости при растяжении материалов, причем в большей степени при использовании бензальдегида. Кроме того, при модифицировании существенно повышается адгезия материалов, очевидно в связи с улучшением совместимости на границе раздела фаз. Для снижения стоимости изделий из угле- и стеклонаполненных ПЭЭК и других термопластов предложено [71] несколько способов ремонта в полевых условиях конструкционных материалов на основе указанных полимеров, в том числе магнитная тепловая индукция, склеивание, ультразвуковая сварка, сварка трением (или вибрацией), сварка в инертном газе. Эти способы позволяют расширить применение полимерных композиционных материалов в авиационной и космической технике. Литература 1. Chem/ Ind. Jap., 1988, v. 39, No 12, p.1044. 2. Lee G., Parter R.S. Polymer Engng. Sci, 1986, v. 26, No 9, p. 633. 3. Small R.W.H. Europ. Polymer J., 1986, v. 22, No 9, p. 699. 4. Wakelyn N.T.-G. Polymer Sci. Polymer Chem. End., 1986, v. 24, No 9, p. 2101. 5. Cebe P. Polymer Comp., 1888, v. 9, No 4, p. 271. 6. Mingbi Q. e.a. Thermochim. Acta, 1988, v. 134, p. 223. 7. Mingbi Q. e.a. Acta Polymer Sin., 1989, No 3, p. 257. 8. Wang W. e.a. Acta Polymer Sin., 1989, No 3, p. 337. 9. Crick R.A. e.a. J. Mat Sci., 1987, v. 22, Mo 6, p. 2094. 10. Tung C.M., Dynes P.G. J. Appl. Polymer Sci., 1987, v. 33, No 2, p. 505. 11. Talbott M.F. e.a. J. Comp. Mat., 1987, v. 21, No 11, p. 1057. 12. Wang Q., Springer G., J. Comp. Mat., 1989, v. 23, No 5, p. 434. 13. Shukla G.G., Sichina W.G. Antec. 84 Plast. World Econ. 42nd Techn. Conf. and Exhib. New Orleans, 1984. Conf. Proc. Brookfield, Conn., 1984. p. 265. 14. Karger-Kocsis G., Friedrich K. Plast. Rubb. Proc. Appl., 1987, v. 8, No 2, p. 91. 15. Friedrich K. e.a. Composites (Gr. Brit.), 1986, v. 17, No 3, p. 205. 16. Mijovic J., Gsell T.C. SAMPE QUART., 1990, v. 21, p. 42. 17. Chou Hsin Nan. 18 th Int. SAMPE Techn. Conf. Seattle, Wash., 1986. Covina, Calif. 1986, v. 18, p. 970. 18. Reilly I.I. e.a. Ibid, p.22. 19. Karger-Kocsis G. e.a. J. Polymer Engng., 1988, v. 8, No 3-4, p. 221. 20. Adv. Comp. Bull., 1990, april, p. 5. 21. Ko F. e.a. Mater - Pathway Future: 33rd Int. SAMPE. Symp. and Exhib. Anaheim, Calif., 1988. Covina, Calif. 1988, p. 899. 22. Maguire D.M. Sampe J., 1989, v. 25, No 1, p. 11. 23. Maffezzoli A.M. Sampe J., 1989, v. 25, No 1, p. 35. 24. Reilly I.I., Kamel I.Z. Polymer Engng. Sci, 1989, v. 29, No 20, p. 1446. 25. Reilly I.I., Kamel I.Z. Polymer Engng. Sci, 1989, v. 29, No 20, p. 1456. 26. Stermstein S.S. e.a. Deform., Yield and Fracture Polymer. 6th Int. Conf. Cambridge, 1985. London, S.a., v. 15, p. 1. 27. Turner F.M. Cogswell F.N. 18 th Int. SAMPE Techn. Conf. Seattle, Wash., 1986. Covina, Calif. 1986, v. 18, p. 32. 28. Crosby J.M. e.a. 19 th Int. SAMPE Techn. Conf. Crystaly City, 1987. Covina, Calif. 1987, v. 19, p. 476. 29. Lhymn C. Adv. Polymer Techn., 1986, v. 6, No 2, p. 203. 30. Lhymn C. Wear, 1987, v. 114, No 2, p. 223. 31. Lhymn C. ASLE Trans., 1987, v. 30, No 3, p. 324. 32. Lhymn C., Lhymn I.O. Adv. Polymer. 1988, v. 8, No 4, p. 417. 33. Mach. Des., 1988, v. 60, No 5, p. 144. 34. Pritchard G., Kandles S.J. 16th Keinforced Plast. Congr. Blackpool, 1988. London, 1988, p. 73. 35. Fanter D.L. e.a. Polym. Mater. Sci. and Eng. Proc. ACS Div. Polym. Mater.: Sci. and Eng. New Jork, 1986. Washington, D.C., 1986, v. 54, p. 695. 36. Habcox N.L., Phillips D.C. Proc. 2nd Conf. Mater. End., London, 1985, p. 139. 37. Griffiths G.R. e.a. Mater - Pathway Future: 33rd Int. SAMPE. Symp. and Exhib. Anaheim, Calif., 1988. Covina, Calif. 1988, p. 308. 38. Cogswell F.N. 28th Nat. SAMPE. Symp. and Exhib. Anaheim, Calif., 1983. Azusa, Calif. 1983, v. 28, p. 528. 39. Tanaka Ch. High Polymer Jap., 1989, v. 38, No 9, p. 890. 40. Яп. заявка 60-44551. 41. Baeklund J. Rapp. Ingenjoersvetenskapsakal, 1986, No 302, p. 103. 42. Sham Chi e.a. Polymer, 1988, v. 29. No 6, p. 1016. 43. Guo Q. e.a. Polymer Bull., 1988, v. 29. No 6, p. 517. 44. Plastverarbeiter, 1987, Bd. 38, No 5, S. 46. 45. Wu Zhongwen e.a. Angew. Makrom. Chem., 1989, No 171, p. 119. 46. Silverman E.M., Jones R.J. Mater - Pathway Future: 33rd Int. SAMPE. Symp. and Exhib. Anaheim, Calif., 1988. Covina, Calif. 1988, p. 1418. 47. Dickson R.F. e.a. J. Mat. Sci, 1985, v. 20, No 1, p. 60. 48. Hartness J.T., Kim R.J. 28th Nat. SAMPE. Symp. and Exhib. Anaheim, Calif., 1983. Azusa, Calif. 1983, v. 28, p. 535. 49. Заявка ФРГ 3425960. 50. Cervenka A. Polymer Comp., 1988, v. 9, No 4, p. 263. 51. Curtis D.C. e.a. Composites (Gr. Brit.), 1988, v. 19, No 6, p. 446. 52. Jaconis J.M. Adv. Mat. Techn., 1987: 32nd Int. SAMPE. Symp. and Exhib. Anaheim, Calif., 1987. Covina, Calif. 1987, p. 104. 53. Majidi A.P. e.a. 19 th Int. SAMPE Techn. Conf. Crystaly City, 1987. Covina, Calif. 1987, v. 19, p. 576. 54. Grove S.M., Short D. Plast. Rubb. Proc. Appl., 1988, v. 10, No 1, p. 34. 55. Elsenussi A.K. Composites (Gr. Brit.), 1989, v. 20, No 3, p. 249. 56. Заявка ФРГ 3702929. 57. Briscol D.J. e.a. Wear, 1986, v. 108, No 4, p. 357. 58. Заявка Великобритании 2136439А. 59. Adaleman R.L. e.a. 13th Reinforced Plast. Congr. Brighton, 1982. London, 1982, p. 71. 60. Япю заявка 64-169655. 61.Isikava T. e.a. J. Soc. Comp. Mat., 1986, v. 12, No 1, p. 8. 62. Dreumel W.H.M. Composites, 1986, v. 26, No 3, p. 132. 63. Barnes J.A., Cogswell F.N. SAMPE Qurt., 1989, v. 20, No 3, p. 22. 64. Lee R.J. Composites, 1987, v. 18, No 1, p. 35. 65. Morton J., Godwin E.W. Compos. Struct., 1989, v. 13, No 1, p. 1. 66. Chang I.I. Mater - Pathway Future: 33rd Int. SAMPE. Symp. and Exhib. Anaheim, Calif., 1988. Covina, Calif. 1988, p. 194. 67. Chan C.-M., Venkatraman S. Polymer Sci., Polymer Phys., 1987, v. B25, No 8, p. 1665. 68. Venkatraman S., Chan C.-M. Am. Chem. Soc. Polymer Preps., 1986, v. 27, No 1, p. 305. 69. Chan C.-M., Venkatraman S. J. Appl. Polymer Sci., 1986, v. 32, No 7, p. 5933. 70. Qipeng Guo e.a. Europ. Polymer J., 1990, v. 26, No 3, p. 355. 71. Welder S.M. e.a. Mat Des., 1986, v. 7, No 3, p. 147.
А.Х. Шаов, А.М. Хараев, А.К. Микитаев, Г.С. Матвелашвили, З.С. Хасбулатова
Источник: «Пластические массы»
|