В ходе исследований обнаружена грибковая природа загрязнений. Сегодня наши петербургские авторы дают рекомендации по режиму эксплуатации имеющихся изоляторов, а также по разработке устойчивых к грибковому поражению материалов защитного покрытия и по микроскопическому контролю качества поверхности изготавливаемых изоляторов. 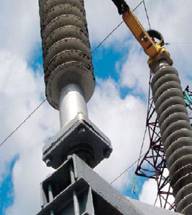
Рис. 1 Опорные полимерные изоляторы типа ИОСПК 10-110/480- II-УХЛ1 в составе разъединителя горизонтально поворотного типа. Видны загрязненные и чистые ребра Высоковольтная полимерная изоляция в настоящее время интенсивно внедряется в энергосистемы практически всех стран мира. В России применение полимерных изоляторов получило важное специфическое направление, связанное с использованием опорных изоляторов всех классов напряжения до 220 кВ включительно. Причиной этого являются сложные климатические (главным образом, температурные) условия, вызывающие разрушение традиционно использовавшихся фарфоровых изоляторов, что уже привело к многочисленным авариям на действующих подстанциях. Применение полимерных изоляторов вместо фарфоровых позволяет повысить надежность подстанций, однако требует учета специфических свойств полимерных материалов, проявляющихся при длительной эксплуатации. Изготовленные из полимерных материалов защитные оболочки опорных изоляторов обладают высокой химической стойкостью, широким температурным диапазоном и, что очень важно, высокой гидрофобностью. С другой стороны, в зависимости от большого числа различных факторов однотипные изоляторы компаний-производителей существенно различаются по качеству. Причем определить действительное состояние изделия можно лишь в результате испытаний, нередко требующих значительных средств и сложного оборудования. Более того, к снижению качества изоляторов могут привести нарушения технологического режима, обнаружить которые в готовом изделии существующими средствами крайне затруднительно, а стандартизированными испытательными процедурами просто невозможно. В качестве примера можно указать на аномально высокую загрязняемость опорных полимерных изоляторов в некоторых районах Южной Карелии. Карельский перешеек и Южная Карелия – это территория к северу от Санкт-Петербурга, ограниченная Финским заливом Балтийского моря и Ладожским озером. Здесь расположен ряд населенных пунктов, а также промышленные предприятия по заготовке леса и добыче гранита. Энергоснабжение этих объектов осуществляется по воздушным линиям электропередачи 110 кВ и распределительным сетям 35 и 10 кВ с помощью ряда понижающих подстанций. Начиная с 2002 года некоторые из этих подстанций были снабжены опорными полимерными изоляторами (ОПИ) 35 и 110 кВ, выполняющими функции шинных опор, а также опорно-поворотных элементов в разъединителях горизонтально-поворотного типа РНД и РНДЗ (рис. 1). В общей сложности в настоящее время на пяти обследованных в ходе выполнения настоящей работы подстанциях системы ОАО «Карелэнерго» установлены более 300 ОПИ, причем замена традиционных фарфоровых изоляторов на полимерные происходила ежегодно практически одинаковыми партиями. В эксплуатации находятся ОПИ четырех различных российских производителей. Часть ОПИ изготовлена методом пореберной сборки, а другая часть – методом отливки. Защитная оболочка ОПИ светло-серого и синего цвета изготовлена из кремнийорганической резины высокотемпературной вулканизации (HTV). АНОМАЛЬНЫЕ ЗАГРЯЗНЕНИЯ ОПИ В процессе эксплуатации было замечено, что с течением времени установленные ОПИ покрываются загрязнениями, состоящими из отдельных пятен черного цвета диаметром до 20 мм. На рис. 1 видны только нижние поверхности ребер, однако загрязнения в равной степени покрывают и верхнюю поверхность, концентрируясь на внешней периферии ребер. Вертикальные цилиндрические поверхности загрязнены в несколько меньшей степени. Постепенно увеличиваясь в размерах, на некоторых ОПИ за пять лет эксплуатации пятна загрязнений покрыли поверхность полимерной защитной оболочки сплошным слоем, что вызвало необходимость специальных работ по очистке этих изоляторов. Наличие и концентрация загрязнений не связаны с ориентацией поверхности относительно внешнего электрического поля или относительно розы ветров, не зависят от расположенных рядом предметов или области преимущественной освещенности. Поскольку аналогичные процессы возникновения пятен имеют место на всех ОПИ в различной степени, наблюдения не позволили также связать загрязняемость ОПИ с какой-либо из фирм-изготовителей. Наиболее действенным установленным эксплуатационным фактором, оказывающим влияние на загрязняемость ОПИ, является длительность эксплуатации: чем она больше, тем сильнее увеличиваются размеры, плотность почернения и концентрация пятен загрязнений. Кроме того, была отмечена зависимость интенсивности загрязнений ОПИ от расстояния до места проведения карьерных (в том числе взрывных) работ на горно-добывающем предприятии по добыче гранита: наибольшее число сильно загрязненных изоляторов и наибольшая степень загрязнения наблюдаются на подстанции № 93 «Карьерная», расположенной на расстоянии 1,5–2 км от места проведения работ. На подстанции «Лахденпохья», расположенной на расстоянии более 30 км от места горных разработок, уровень загрязняемости ОПИ в целом заметно ниже. Важно заметить, что на ряде изоляторов отмечено существенное различие загрязняемости ребер: наряду с ребрами, покрытыми пятнами загрязнений, имеются ребра, практически свободные от загрязнений (рис. 1). Во всех случаях это различие наблюдалось исключительно на изоляторах, изготовленных по методу пореберной сборки, эксплуатируемых в течение наиболее длительного времени (выпуск 2002 г., эксплуатация с 2003 г.). На изоляторах, изготовленных методом литья, такого не наблюдается. При этом плотность загрязнений на ребрах соответствует общей отмеченной выше тенденции к усилению загрязняемости при увеличении длительности эксплуатации, в то время как чистые ребра явно выпадают из этой зависимости, сохраняя свое исходное чистое состояние значительно лучше, чем другие изоляторы, установленные позже. Загрязнения в виде пятен также крайне незначительны (практически отсутствуют) на поверхности размещенных рядом фарфоровых опорных изоляторов, несмотря на то, что в эксплуатации они находились намного дольше (10–15 лет). В целом общий уровень загрязняемости фарфоровых опорных изоляторов значительно ниже, чем у полимерных. Несмотря на наличие загрязнений, поверхность ОПИ в полной мере сохраняет гидрофобность: вода концентрируется на ней в виде обособленных капель, в то время как на фарфоровых изоляторах образует ровную пленку. Гидрофобность поверхности ОПИ была полностью восстановлена даже после испытаний на трекингоэрозионную стойкость, связанных с длительным воздействием электрической дуги. При этом высокой гидрофобностью обладает не только собственно поверхность полимерного материала, но и возникшие на ней загрязнения, что является проявлением известного свойства силиконовой резины передавать гидрофобность. Это объясняется сложной молекулярной структурой материала, в составе которого присутствуют, наряду с прочной полимерной решеткой, легкие, не связанные с ней молекулы. Они, обладая способностью к диффузии, перемещаются внутри защитного слоя, выходят на поверхность и обволакивают находящиеся на ней частицы. Таким образом, наблюдаемые в данном случае загрязнения оказываются гидрофобными в такой же степени, как чистая поверхность материала защитной оболочки. При испытаниях на трекингоэрозионную стойкость в соответствии с ГОСТ 27473-87 по классу 4,5 кВ, образцы материала защитного покрытия были подвергнуты интенсивному воздействию частичными дужками, причем показали высокую стойкость. Разрушения поверхности имеют явно выраженный эрозионный характер без образования проводящего трека и минимальные масштабы. Следы эрозии на поверхности имеют форму канавки глубиной не более 0,3 мм и шириной 1,5–2,5 мм. В ходе испытаний эксплуатационные загрязнения в местах стекания потока электролита были частично смыты, при этом обнажилась гладкая чистая поверхность образца, а загрязнения сохранились только в отдельных точках и диаметром не более 100 мкм. Во время испытаний и по полученным результатам не было указаний на фиксацию поверхностных разрядов на следах эксплуатационных загрязнений. Результаты испытаний показали, что материал покрытия удовлетворяет предъявляемым нормативным требованиям независимо от отсутствия или наличия загрязнений. Сохранение высокого эксплуатационного качества поверхности ОПИ подтверждается отсутствием информации о повышенной интенсивности перекрытий загрязненных изоляторов, поскольку единственным указанием на их отличие от «чистых» изоляторов служит факт появления загрязнений, но не повышенная аварийность, связанная с перекрытиями.
|