Вот только не учитывают такие «горе-трубники», что есть испытания, которые выявят использование базовой марки при производстве трубы и, вместе с тем, результаты которых однозначно свидетельствуют об эксплуатационных характеристиках трубы. К ним относятся: стойкость к газовым составляющим (СГС); – термостабильность; – стойкость к быстрому распространению трещин. С целью определения поведения труб во время этих испытаний, изготовленных из базовой марки полиэтилена путем введения суперконцентрата сажи непосредственно в экструдер, на ООО «Рубежанский трубный завод» был проведен эксперимент. 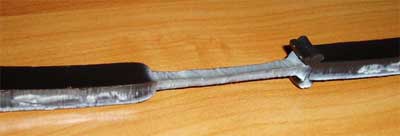
Были выпущены опытные партии труб стандартным размерным отношением SDR 11 диаметром 32 мм и SDR 17,6 диаметром 225 мм из полиэтилена 7700М с введением при экструзии суперконцентрата черного цвета с содержанием технического углерода на уровне 40 %. Количество суперконцентрата было подобрано таким образом, чтобы обеспечить содержание сажи в трубе в пределах 2,1–2,2 %. Трубы производились на современных экструзионных линиях с точным дозированием исходного полиэтилена и красителя. Хотим сразу успокоить клиентов РТЗ, партии трубы произведены исключительно в экспериментальных целях и к реализации не допускаются (после проведения необходимых испытаний были утилизированы). Испытания трубы были проведены в заводской испытательной лаборатории, аккредитованной на проведение всех указанных испытаний (напомним, лаборатория ООО «РТЗ» — одна из немногих отечественных лабораторий, где определяются СГС и термостабильность, а также – единственная, проводящая испытания на стойкость к быстрому распространению трещин). Стойкость к газовым составляющим Этот параметр описывает стойкость полиэтиленовой трубы к газовому конденсату, который содержится в некотором количестве в транспортируемом газе и является скорее характеристикой полимерной композиции (полиэтиленовой матрицы с введенными в нее добавками), используемой в производстве труб, чем характеристикой самой трубы. А потому особенно важно, чтобы при производстве трубы использовалась предварительно окрашенная композиция, полученная в заводских условиях, с введенными в нее добавками и стабилизаторами, способ распределения которых жестко регламентирован техническими условиями производства полиэтилена. Испытания проводились согласно п.8.8 ДСТУ Б В.2.7-73 с учетом международных норм по приложению B ISO 4437, а также EN 721. Для испытаний труба диаметром 32 мм была заполнена синтетическим конденсатом, состоящим из смеси 50 % (по массе) н-декана (99 %) и 50 % 1-3-5 триметилбензола. После выдержки трубы в течение 1500 ч при 23 °С образцы были помещены в водную среду с температурой 80 °С, где были подвергнуты постоянному внутреннему давлению 0,443 МПа (что соответствует начальному напряжению в стенке 2 МПа). По отечественным нормам (п. 7, табл. 2 ДСТУ Б В.2.7-73) образцы должны были выдержать 30 ч, тогда как в Европе (табл.1 ISO 4437) требования мягче – 20 ч. Разрушение образцов наблюдалось по истечении 12, 15 и 19 часов соответственно. Расхождение в результатах испытаний объясняется неравномерностью свойств выпускаемой полиэтиленовой трубы при введении красителя непосредственно в горловину экструдера. Термостабильность (индукционный период окисления) Термостабильность – одно из важнейших свойств, как полиэтиленовой композиции, так и самой трубы. Ни для кого не секрет, что с течением времени полиэтилен (в том числе полиэтилен стенки трубы) подвергается термоокислительной деструкции, что безусловно в конечном счете сказывается на его прочностных свойствах. Это явление особенно выражено на внутренней поверхности трубы, где необходимые стабилизаторы со временем «вымываются» течением жидкости или газа. Потому очень важную роль играют не только содержание и гомогенность распределения, но и также тип (марка) как термо-, так и светостабилизаторов (в частности, сажи). Испытания были проведены согласно п. 8.9 ДСТУ Б В.2.7-73 с учетом международных норм ISO 10837, EN 728. В работе был использован низкотемпературный дифференциальный термоанализатор НДТА-1. Навеска образца трубы (фрагмент тонкой стружки, срезанной с ее торца) в количестве 15 мг была помещена в камеру прибора, где нагревалась со скоростью 20 °С/мин в токе азота до температуры 200 °С. По истечении 5 минут газ-носитель был переключен на кислород, этот момент был зафиксирован как «начало эксперимента». Интервал времени, определенный с «начала эксперимента» до начала экзотермического пика и был принят в качестве индукционного периода окисления.
|