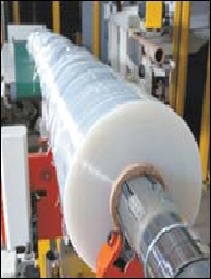
Компании, занимающиеся обработкой стретч пленок, привыкли к расширению рынка вдвое каждые пять лет. В период между 1985 г. и 1990 г. спрос вырос с 250 миллионов фунтов в год до 500 миллионов фунтов, а за период с 1990 г. до 1995 г. рынок взлетел до 1 миллиарда фунтов. Еще каких-нибудь пять лет тому назад, когда рынок наводнили пятислойные стретч пленки, спрос на смолу продолжал расти в двухзначном выражении. Но на протяжении последних нескольких лет спрос на смолы для стретч пленки затормозился на 1.4 миллиарда фунтов. Стретч пленка это на 65% - 70% литая пленка, в основном, для механизированного обертывания, и на 30% - 35% экструзионно-раздувная пленка, в основном, для ручного обертывания товаров и нескольких специальных пленок с высокой устойчивостью к прокалыванию. Конкуренция в этом секторе производства пленок стала борьбой за долю рынка не на жизнь, а на смерть. Прибыль обработчиков зачастую составляет всего несколько десятых или сотых цента за фунт, а количество новых установок свелось всего к паре новых машин в год. Единственными североамериканскими компаниями-обработчиками, которые, по-видимому, развиваются и делают инвестиции, являются компании, которые производят новые пленки с большим числом слоев. Когда в середине девяностых появились пятислойные стретч пленки, они заменили множество одно- и трехслойных пленок, созданных из гексен и/или октен LLDPE. Для этого потребовался четвертый экструдер и пятислойный фидблок, который позволял использовать менее дорогой бутен LLDPE, армированный тонкими слоями подложки из бывшего тогда новинкой металлоценового LLDPE. Типичной пятислойной структурой могла быть следующая: A-B-C-B-A с 10% поверхностными покрытиями из гексен LLDPE, 20% подповерхностными покрытиями из mLLDPE, и 40% ядром из бутенового LLDPE. 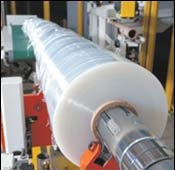 Производство более тонкой пленки без изменения параметров и сложные структуры позволяют сегодняшнему рынку стретч пленки развиваться дальше. Новейшая линия семислойной пленки компании Pliant дает 9,000 футов стретч пленки с толщиной 51 по сравнению со всего лишь 5000 футов традиционной пленки с толщиной 80. По мере того, как увеличивалось количество слоев, установки для производства стретч пленки становились все больше, а производительность все выше. Стандартом пять лет назад были пять 20-дюймовых рулона и три слоя. А теперь это шесть рулонов и пять слоев. На долю пятислойной стретч пленки теперь приходится 40% от всего количества растягивающейся пленки, производимой в Северной Америке, использование металлоценовой смолы выросло с нуля в 1995 г. до 12% от всего LLDPE, который используется для изготовления стретч пленки. Но mLLDPE довольно дорог, поэтому обработчики перешли на изготовление семислойных и девятислойных пленок, преимущественно для того, чтобы сделать возможным применение большего количества смол или бутен LLDPE и меньшего mLLDPE—а также, чтобы в некоторых случаях создавать пленки с более высокими эксплуатационными характеристиками. Например, все производители семислойной растягивающейся пленки говорят, что они могут заменить более толстые пленки с меньшим количеством слоев, не принося при этом в жертву удержание груза. На протяжении последних нескольких лет все линии для производства литой стретч пленки, установленные в Северной Америке, были предназначены для изготовления пятислойной или более многослойной пленки. Они устанавливали все новые рекорды по количеству слоев: сначала семь, затем девять. В настоящее время обработчики и производители установок говорят уже об 11, 14, и даже 70 слоях. “Мы освоили промышленное производство для технологии с микрослойным фидблоком для получения барьерных свойств, но одним из применений может также быть и растягивающаяся пленка. Мы можем производить слои толщиной в ангстрем [1 ангстрем = 0.0001 микрон] или с десятыми долями процента от толщины пленки”, - говорит Гэри Оливер, старший научный сотрудник компании Cloeren Inc. “Разработчики заинтересованы, но испытаний пока никто не проводит”. Все больше и больше слоев Большинство новых линий, производящих пленки с большим числом слоев, было приобретено новыми игроками рынка стретч пленки, что в результате привело к перераспределению долей рынка. Chaparral Films из Морисвилля, Техас, была первой компанией, которая начала производить пятислойную стретч пленку в 1994 г., и, по имеющимся данным, была первой, кто начал производить семислойную в 1996 г., хотя об этом никогда не сообщалось официально. По сведениям источников из компании Cloeren, которая создавала головки экструдеров и фидблоки, а также была инвестором, Chaparral производила и большее количество слоев на экспериментальной основе. (ITW Stretch Packaging Systems из Гленвью, Иллинойс, купила Chaparral в 1996 г., но она производит только пятислойные пленки.) 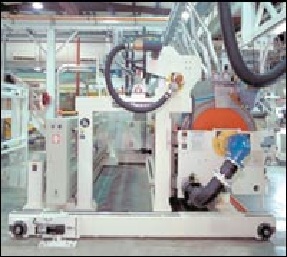 Для производства семислойной пленки с высоким содержанием mLLDPE с высокой производительностью необходимы охлаждающиеся вальцы самого крупного в Северной Америке диаметра. Poly Rafia из Атлакомулко, Мексика, была еще одной компанией, которая в 1996 г. начала производить семислойную пленку, а в 2001 г. добавила к имеющейся и вторую линию. Когда компании Quintec Films Corp. из Шелбивилля, Теннесси, и Pinnacle Films Inc. из Шарлотта, Северная Каролина, начали промышленное производство осенью 1998 г., обе эти компании стали производить только семислойную пленку. Quintec получила Патент США #6,265,055 в июле 2001 г. на производство стретч пленки “с двумя внешними слоями и, по крайней мере, пятью внутренними слоями”. “При наличии достаточного количества экструдеров и слоев Вы сможете производить рентабельную высокопроизводительную пленку с металлоценами. Мы увидели такую рыночную возможность”, - говорит Уильям Райс, президент Pinnacle, в которой в апреле прошлого года была установлена вторая линия для производства семислойной пленки. “Большинство старых давно работающих на рынке игроков не может себе позволить добавлять новые высокотехнологичные мощности. Они не делают повторных инвестиций в линии по производству семислойной пленки”. Тем не менее, две компании, давно работающие на рынке обработки, с тех пор увеличили мощности по производству семислойной стретч пленки: Pliant Corp. из Шаумбурга, Иллинойс, и AEP Industries Inc. из С. Хекенсека, Нью Джерси. |