1.3 Схема процесса производства плит пенополистирольных. 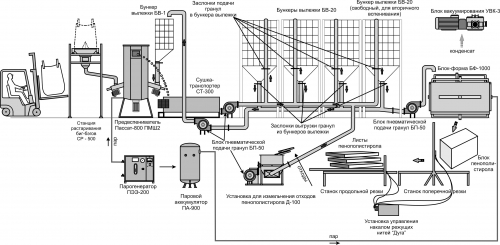
Рис.3 1.4Описание схемы процесса производства пенополистирольных плит. 1.На складе сырья осуществляется входной контроль исходного материала: полистирола ПСВ-С. 2.Гранулы полистирола ПСВ-С со склада сырья загружают в предвспениватель «Пассат 800ПМШ2», где они при подаче небольшого количества пара вспениваются (надуваются), превращаясь в маленькие шарики белого цвета. Контроль режима тепловой обработки. Проверка насыпной плотности вспененного полистирола. 2.Вспененные гранулы подаются пневмотранспортом в сушку-транспортер СТ-300 для предварительной сушки и затем с помощью блока пневматической подачи гранул БП 50 в бункер вылежки. Контроль температуры в сушке-транспортере и остаточной влажности вспененных гранул полистирола ПСВ-С. 3.В бункерах вылежки происходит дополнительное подсушивание и стабилизация давления внутри гранул. Для окончательной стабилизации внутреннего разряжения и достижения показателей остаточной влажности на уровне 0,5-1 % вспененным гранулам полистирола ПСВ-С необходима выдержка материала в бункерах вылежки. Контроль времени вылежки, остаточной влажности вспененных гранул полистирола ПСВ-С и температуры в производственном помещении. 4. При необходимости получения марок пенополистирола с более низкой плотностью (от 6 до 10 кг/м3) применяется вторичное вспенивание вспененных гранул полистирола ПСВ-С. Для этого из бункера вылежки БВ-20 подаются вспененные гранулы полистирола ПСВ-С для вторичного вспенивания в бункер вылежки БВ-1, расположенный около предвспенивателя, затем через дополнительный шнековый питатель в предвспениватель «Пассат-800ПМШ2», где происходит дополнительное вспенивание гранул до плотности 6 -10 кг/м3 с последующей транспортировкой их с помощью пневмотранспорта через сушку-транспортер в отдельный свободный бункер вылежки для гранул, прошедших двухстадийное вспенивание. 5.После вылеживания в бункере вылежки вспененные гранулы полистирола ПСВ-С пневмотранспортом подаются в предварительно прогретую блок-форму БФ-1000, из которой откачали конденсат. Блок-форму загружают вспененными гранулами полистирола до верха и герметично закрывают. Для оптимального режима формовки блока пенополистирола пар в полости формы подается последовательно: сначала под максимальным давлением (5,5 атм) пар подается в передний борт и заднюю стенку блок-формы. Под действием теплового удара происходит «спекание» основного массива блока и его центральной части, затем пар подается в верхнюю крышку и днище блок-формы, происходит формирование верхней и нижней части блока. На третьем этапе пар подается в торцовые стенки блок-формы – спекаются торцы блока пенополистирола. Процесс закончен. Сформованный блок пенополистирола необходимо охладить, поэтому подключают блок вакуумирования УВК-3, откачивают из полостей пар и конденсат, закачивают воздух, стабилизируют внутреннее давление внутри камеры и выравнивают в соответствии с давлением снаружи блок-формы. Контроль подачи вспененных гранул полистирола ПСВ-С. Контроль режима тепловой обработки. Контроль массы блока пенополистирола. 6. Борта блок-формы открываются, извлекают готовый блок пенополистирола, взвешивают и удаляют из рабочей зоны для охлаждения. Охлажденный блок пенополистирола транспортируется на склад вылежки и сушки блоков. Резка влажного блока не допускается, т.к. срез блока будет рваным и неровным. Контроль времени хранения блоков пенополистирола и температуры в производственном помещении. 7. Сухой блок пенополистирола режется на резательном столе. Толщину плиты пенополистирольной можно регулировать от 0 до 500мм. Контроль режимов резки блока пенополистирола. 8.Готовую продукцию принимает служба технического контроля. 9.Плиты пенополистирольные, принятые службой технического контроля, маркируют, упаковывают и транспортируют на склад готовой продукции. Источник: Строймеханика
|