МИР После рекордного 2004 г. [1] и сравнительного скромного 2005 г. [2] темпы роста производства химических волокон и нитей в 2006 г. занимает среднее между предыдущими годами положение [3,14] иллюстрируемое табл.1. Таблица 1. Мировое производство текстильных волокон в 2006 г. Вид волокна | 2006, млн. т | 2006/2005, ±% | Хлопок | 26,3 | +4,5 | Шерсть | 1,3 | - | Химические волокна и нити, в т.ч. | 41,2 | +6,4 | Синтетические, в т.ч.: | 37,8 | +6,4 | Полиэфирные | 27,7 | +8,4 | Полиамидные | 4,1 | +2,4 | Полипропиленовые1) | 3,1 | +2,5 | Полиакрилонитрильные | 2,5 | -3,0 | Целлюлозные | 3,4 | +5,9 | Другие волокна | 6,3 | н/д | Итого | 74,7 | +5,1 |
Примечание: 1) исключая пленочные нити За исключением полиакрилонитрильных (ПАН) в 2006г. по сравнению с 2005 г. возросли объемы выпуска всех видов крупнотоннажных химических волокон (табл.1), в т.ч. целлюлозных на 5,9% до 3,4 млн.т и синтетических на 6,4% до 37,8 млн.т. Химические волокна удерживают передовые позиции на мировом рынке, где их доля в 2006 г. оценивается 54,8%, на хлопок, шерсть и шелк падает 37,4%. При численности планеты 6,57 млрд. человек на душу населения приходится 10,5 кг текстильного сырья. Среди гигантов современной нефтехимии (Китай и США) ситуация с производством химических волокон в 2006 г. диаметрально противоположная. В Китае и сегодня идет наращивание выпуска этой продукции сверхвысокими темпами (табл.2). В марте 2007 г. там было произведено свыше 500 тыс.т синтетических волокон, что на 10% больше по сравнению с предыдущим месяцем, но на 3% ниже, чем за март 2006 г. [4]. Объем продаж химических волокон в стране за март составил 520 тыс.т, что на 24% больше по сравнению с февралем текущего года, но по сравнению с мартом предыдущего года снизился на 3%. В марте запасы волокон на китайских складах по сравнению с февралем сократились на 14% и на 15% - в сравнении с показателями за март прошлого года. Темпы сбыта продукции в марте 2007 г. оказались на 12% выше, чем в феврале, но немного упали относительно марта 2006 г. Из 50ти крупнейших производителей химических волокон в Китае 29 приходится на полиэфирные (ПЭФ), 8 – вискозные, 5 – полиамидные (ПА), 4- поливинилспиртовые (винилон), 2- ПАН и 2 – спандекс. Что касается США, то здесь в последние годы прослеживается обратная картина – в 2006 г. производство синтетических волокон упало по сравнению с 2005 г. по всем основным видам (табл.2), в т.ч. и по коэффициенту загрузки мощностей (табл.3). Таблица 2. Мировое производство химических волокон в 2006г. по регионам. Страны | Синтетические волокна и нити | Целлюлозные 3) | Полиэфирные | Полиамидные 1) | Полиакрилонитрильные2) | Комплексные нити | Штапельное волокно | млн.тонн | ±% | млн.тонн | ±% | млн.тонн | ±% | млн.тонн | ±% | млн.тонн | ±% | Китай | 9,6 | +15 | 6,0 | +15 | 0,9 | +17 | 0,8 | +7 | 1,46 | +20 | Тайвань | 1,2 | -6 | 0,6 | -13 | 0,4 | 0 | 0,2 | +11 | 0,13 | +14 | Индия | 1,2 | +12 | 0,7 | +19 | 0,1 | +5 | 0,1 | -5 | 0,30 | +2 | Ю. Корея | 0,7 | -15 | 0,5 | -1 | 0,2 | -6 | 0,1 | -49 | 0,01 | 0 | Япония | 0,3 | -4 | 0,2 | 0 | 0,1 | -6 | 0,2 | -6 | 0,07 | -2 | ASEAH | 1,3 | -1 | 0,9 | -5 | 0,1 | +6 | 0,1 | +4 | 0,33 | +2 | США | 0,4 | -9 | 0,8 | -8 | 1,1 | -2 | - | -94 | 0,03 | -42 | Западная Европа | - | - | - | - | 0,5 | -1 | 0,7 | 0 | 0,45 | +6 | Остальные | (Исходя из разницы в объемах, приведенными в таблицах 1 и2) | Всего | 15,9 | +7 | 11,3 | +6 | 3,9 | +2 | 2,5 | -5 | 2,88 | +10 |
Примечание: 1 – комплексные нити и штапельное волокно; 2 – штапельное волокно; 3 – комплексные нити и штапельное волокно (кроме ацетатного жгутика). Как ни странно, наиболее очевидный спад заметен у ПЭФ волокон и нитей (табл.2 и3), которые, в свою очередь, в мире развиваются самыми высокими темпами (табл.1). Таблица 3. Состояние производства синтетических волокон в США за 2006 г. Наименование волокна | Производство | Коэффициент загрузки мощности, % | 2006г., тыс.т | 2006/2005г.г.,±% | 2000 г. | 2005 г. | 2006 г. | Полиэфирные: | 1245 | -9,8 | 81,1 | 76,1 | 73,6 | Штапельное волокно | 837 | -9,1 | 91,3 | 91,1 | 83,9 | Текстильная нить | 255 | -13,1 | 64,2 | 55,3 | 56,1 | Техническая нить | 153 | -8,8 | 87,8 | 82,0 | 80,7 | Полиамидные: | 1037 | -5,3 | 82,1 | 85,0 | 85,1 | Штапельное волокно | 250 | -9,5 | 82,9 | 69,8 | 74,0 | Ковровый жгутик BCF | 665 | -3,8 | 92,6 | 90,5 | 87,4 | Техническая нить (корд) | 71 | -7,6 | 80,7 | 96,2 | 91,6 | Текстильная нить | 51 | -1,9 | 72,2 | 83,4 | 87,5 | Полиакрилонитрильное | н/д | н/д | 69,1 | 47,5 | 70,0 | Полипропиленовые: | 1039 | н/д | 83,0 | 79,0 | 75,4 | Комплексные нити1) | 1018 | -6,7 | 73,0 | 80,1 | 75,7 | Штапельное волокно | 291 | -8,6 | 92,1 | 77,9 | 75,0 | Итого | 3593 | -8,1 | 80,7 | 76,9 | 73,2 |
Примечание: 1) включая мононити, пленочные нити и спанбонд. Если к этому добавить довольно сложную обстановку со сбором и реализацией хлопка в США, то состояние дел с собственным текстильным сырьем далеко от благополучного (табл.3). Очевидная причина – в активном импорте дешевых текстильных товаров и сырья для них из других стран, в первую очередь из Китая и Мексики. И как следствие, снижение из года в год загрузки собственных мощностей по большинству видов синтетических волокон и нитей (табл.3).
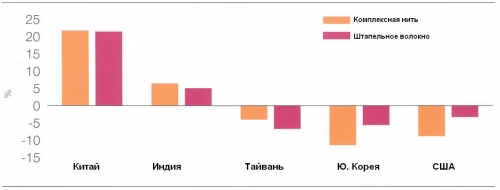
Рис.1. Среднегодовые темпы роста полиэфирных волокон и нитей по регионам с 2000 по 2006 гг. По прежнему лидером среди всех видов текстильного сырья остаются полиэфирные волокна, прирост которых в цитируемый период составил 8,4% до 27,7 млн.т, в т.ч. по штапельному волокну и жгуту на 7,9% до 11,7 млн.т и комплексным, включая текстильные и технические нити, на 88,8% до 16,0 млн.т (табл. 1). Самые высокие темпы производства наблюдаются в Азии, особенно в Китае, Индии и Вьетнаме (табл.2), а в Европе и Америке, наоборот, происходит спад, оцениваемый в среднем ок.7% и прекрасно иллюстрируемый компанией “Oerlikon”(Швейцария) с помощью рис.1 [15]. Стержневым вопросом в сфере производства полиэфиров, будь-то волокна или бутыли, остается проблема обеспечения исходным сырьем, где к главным «фигурантам» параксилолу (ПК), терефталевой кислоте (ТФК) и моноэтиленгликолю (МЭГ) добавился острый дефицит изофталевой кислоты (ИФК), используемой преимущественно при получении пищевого полиэтилентерефталата (ПЭТ) для бутылок и низкоплавких полиэфиров. В Азии, например, несмотря на значительные инвестиции в производство смеси ксилолов и ПК, спрос на них опережает действующие мощности данного региона [5]. При этом основное бремя инвестирования здесь ложится на страны Азии (в первую очередь Китай) и Ближнего Востока, поскольку западные компании сомневаются, что подобные инвестиции дадут нужный экономический эффект. На 2009 г. запланированы более чем достаточные инвестиции, но в период 2006-2008 г.г. предложение на региональном рынке будет отставать от спроса на смеси ксилолов и ПК, который будет расти в среднем на 2,2 и 1,6 млн.т в год соответственно, а это создает финансовые трудности при создании новых мощностей в будущем. В ближайшее время Китай будет полностью обеспечивать себя очищенной ТФК и сократит объемы ее импорта. С другой стороны, это приведет к увеличению импорта ПК, даже с учетом реинвестирования в расширение его мощностей. Самостоятельное обеспечение Китая очищенной ТФК вызовет сокращение экспортного потенциала других стран и таким образом снизит их потребности в сырьевом ПК и смеси ксилолов. Компания “Liaoyang Petrochemical” расширила производство ТФК на заводе в городе Ляоян (провинция Ляонин, Китай) до 800 тыс.т в год. В долгосрочной перспективе в связи с ростом внутреннего потребления ТФК и ограниченным инвестированием в производство ПК, Европа станет чистым импортером ПК, а Ближний Восток вытеснит США в качестве основного его поставщика на мировой рынок. Английская компания “British Petroleum (ВР )” будет увеличивать на своем заводе в г. Геель (Бельгия) мощности по ТФК на 350 тыс.т до 1,4 млн.т/год. Проект предусматривает значительное повышение производительности двух работающих установок и внедрение новой технологии получения очищенной ТФК, успешно уже опробированной ВР на китайском заводе в г. Чжухай с единичной мощностью линии 900 тыс.т/год. Центр мирового производства МЭГ все больше смещается в ближневосточный регион. Благодаря реализации проектов компаний “Sabic”, “Jubail United Petrochemicals” (Саудовская Аравия) и “National Petrochemical” (Иран) в 2007 г. только на Ближнем Востоке мощности по производству МЭГ возрастут в среднем на 1,5 млн.т/год [6]. В 2006 г. в этом регионе, имеющим суммарные мощности по МЭГ ок. 4,8 млн.т в год, 87,1% их расположено в Саудовской Аравии, 10,6% в Кувейте и 2,3% в Иране. В период с 2006 по 2010 г.г. в Саудовской Аравии и Иране будут введены дополнительные мощности в объеме соответственно 4,0 и 2,9 млн.т./год. К 2009 г. ожидаются серьезные изменения в структуре мирового производства и потребления МЭГ. Северная Америка и Западная Европа собираются сокращать собственное производство и часть потребностей удовлетворять за счет импорта. Азиатский регион, в т.ч. Китай, по прежнему в значительной степени будет зависеть от импорта, который достигнет 6,5-6,6 млн.т/год. Ближний Восток станет крупнейшим нетто-экспортером МЭГ, способным практически полностью удовлетворить запросы остального мира. Среди стран-экспортеров лидирующие позиции к 2010 г. займут (в млн.т/год) Саудовская Аравия (6,7), Иран (1,4) и Кувейт (1,1). В 2006 г. Китай экспортировал в США ПЭФ волокон на сумму почти 111 млн.долл. против 30 млн.долл. в 2004 г. Активный импорт из Китая дешевого ПЭФ волокна , предназначенного для изготовления лыжных костюмов, подушек, спальных мешков и т.п., наносит серьезный ущерб американским производителям. Это вынудило Министерство торговли США издать указ о введении антидемпинговых пошлин размером до 44% на импорт китайского волокна. Постепенно вектор экспорта ПЭФ волокон и нитей из Китая поворачивается в сторону России и стран СНГ , особенно в части продаж технических нитей, ставя тем самым очевидные преграды для реализации продукции ОАО «Могилевхимволокно» (республика Беларусь). В частности, мощности по ПЭФ обычной технической и HMLS (для шинного корда) в Китае в 2007г. достигнут 400 тыс.т, что примерно в 20 раз больше, чем ныне у упомянутого чуть выше белорусского предприятия. В декабре 2006 г. Европейская комиссия в Брюсселе включила дополнительно в список стран (Белоруссия, Китай, Ю. Корея и Саудовская Аравия), на которых распространяются антидемпинговые ограничения на импорт ПЭФ штапельного волокна в странах ЕЭС, Малайзию и Тайвань, установив для них размер ввозной пошлины соответственно 23,0 и 29,5% [3]. Суммарно эти налоги отражают 80% доходов от всех ПЭФ волокон, импортируемых в европейский союз. Причем эти волокна представляют в значительной степени сырье для нетканых материалов, составляющее 50% или более стоимости последних. Ощутимую экономическую и экологическую выгоду дает переработка вторичного (т.н. рециклинг) ПЭТ, получаемого чаще всего в виде хлопьев или гранул из отходов пластиковых бутылей. Как показывает мировая практика, 57% этого сырья повторно идет на изготовление волокон, 16% - листов, 15% - бутылок, 8% - липкой ленты и 4% - других товаров. По данным фирмы “MultiPet Cesellschaft fur PET Recyling” (г. Бернбург, Германия), перерабатывающей ежегодно 22 тыс.т отходов ПЭТ бутылок в виде хлопьев, полученный таким образом рециклят ПЭТ строго отвечает качеству стандартного полимера и аттестован по DIN/EN ISO 9001:2000 [3]. В нашем докладе [16] дана развернутая картина производства и потребления пищевого ПЭТ для бутылей в мировом, региональном и российском масштабах. Были рассмотрены практически все аспекты этой проблемы и ее пагубное влияние на развитие текстильного сектора, испытующего определенный дефицит в ПЭФ волокнах и нитях. К этому добавилась информация группы исследователей из «Национального института здоровья США» [17], которые пришли к выводу о том, что продукты в ПЭТ-упаковке способны оказывать негативное влияние на развитие репродуктивной системы мальчиков и вести к бесплодию. Американские ученые утверждают, что бутылки нельзя относить к диетической или хотя бы экологически чистой таре. Это же согласуется с данными российских экспертов, которые выявили, что при длительном хранении пива в такой таре происходят довольно большие изменения в его составе, сопровождаемые накоплением вредных и опасных для здоровья продуктов окисления. Может быть, приведенные факты остановят любителей быстрых доходов любой ценой в ОАО «Полиэф» (г. Благовещенск), ООО «Сенеж» (г. Солнечногорск), ООО «Алко-Нафта» (г. Калининград) и др., открыв путь для подъема крайне важного текстильного сырья – волокон и нитей из ПЭТ. Прирост мирового производства волокон из ПА, главным образом в виде комплексных технических (кордных) и текстильных нитей из ПА6 (типа капрон) и ПА 66 (типа найлон), в 2006 г. составил 2,4%, достигнув 4,1 млн.т. В то время как для всех виды готовой продукции на основе комплексных нитей имеет место рост производства, для штапельного волокна, наоборот, на протяжении длительного времени обнаруживается тенденция к его непрерывному снижению. Аналогично общей картине развития ПЭФ волокон, в западных странах сокращение выпуска ПА волокон оценивается примерно 2%. В противовес этому, Китай, Индия, Тайвань и Таиланд консолидировано увеличили свое производство на 11% по сравнению с 2005 г. Как видно из рис.2 [3], крупнейшим производителем технических (кордных) нитей в мире сегодня является Китай. Еще в 1990 г., когда на мировом рынке технического текстиля из ПА господствовали Северная Америка, Западная Европа и Япония, доля Китая здесь составляла всего 6% (главным образом ПА6). В 2005 г. доля Китая в мировом производстве этой продукции на основе ПА6 составила 45%, ПА66 – 20% и ПЭТ – 15%. К концу 2010 г.(рис.2) эти цифры соответственно возрастут: ПА6 до 60%, ПА66 и ПЭТ – до 25% каждая. В 2010 г. Китай будет обладать 1/3 мировых запасов сырья для выпуска синтетических нитей для шинного корда, резино-технических изделий и т.п. [3].
Рис.2. Мировое производство синтетических технических нитей (1) и доля в нем Китая (2). Мировое производство ПП волокон в 2006 г. возросло на 2,5% до 3,1 млн.т (исключая пленочные нити). Практически тот же, что и в 2005 г., уровень выпуска ПП штапельного волокна в мире обусловлен в значительной мере невысоким коэффициентом загрузки существующего оборудования. Напротив, объем комплексных нитей в этот же период увеличился на 5,5%. На рынке наблюдались скромные объемы продаж высокопрочных нитей повышенных титров. Рост выпуска ПП коврового жгутика типа BCF во многом обязан активной позиции его производителей в США, Турции и Среднем Востоке. В целом, в структуре потребления ПП изготовления из него волокон, нитей и аналогичной им продукции является одним из самых емких сегментов мирового рынка (более 30%) [7], а в России, например, ок. 8%. Нетканые материалы на основе ПП широко применяются в различных отраслях современного хозяйства – медицина, гигиена, строительство, геотекстиль, автомобилестроение, мебель и мн. др., обеспечивая высокие темпы ежегодного прироста от 5 до 8%. ПАН волокно – единственное из упомянутых в табл.1, где в 2006 г. отмечено падение производства на 2,5% до 2,5 млн.т. Доля от мирового выпуска этого волокна в Азии и Европе осталась по сравнению с 2005 г. без изменений – 59 и 34% соответственно. В то же время зафиксирован рост объемов ПАН волокна в Китае, Тайване и Таиланде, наблюдается активность в этой области на предприятиях Индии и Японии, снижение его производства в США и Ю. Корее. Китай сократил экспорт ПАН волокна из Западной Европы – внутренние потребности удовлетворяются за счет местных поставок. После повышенного спроса в ноябре-декабре 2006 г. американские прядильные фабрики в январе-феврале 2007 г. значительно сократили закупки по импорту ПАН волокна, что является нормальным для данного времени года из-за ослабевания спроса на свитера и аналогичные предметы одежды . Тем не менее, спрос на пряжу из ПАН со стороны производителей трикотажных изделий и обивочных тканей остается устойчивым [8]. Более оптимистичным выглядит спрос в Южной Америке, в частности Бразилии. В Зап. Европе производство ПАН волокна в 2006 г. уменьшилось на 4,9%, сокращение объемов внутренних заказов нашло отражение в некотором падении цен на ПАН жгут 3,3 дтекс (до 1,85 €/кг). Продолжает расти, хотя и не столь стремительно как в 2005 г., мировое производство высокоэластичной полиуретановой нити спандекс, достигнув в 2006 г. объема 340 тыс.тонн. Его рост был ограничен закрытием некоторых компаний и дефицитом сырья. Китай путем антидемпинговых мероприятий сократил вдвое (с 20,3 до 9,8 тыс.т) импорт спандекса из Японии, Сингапура, Ю. Кореи, США и Тайваня, тем самым увеличив приток местных производителей на внутренний и мировой рынки. Ведущие компании данной отрасли – “Hyosung” (Япония) и “Invista” (США) собираются очень активно участвовать в будущем развитии спандекса. Дополнительное увеличение мощности в Китае, Ю. Корее и Турции позволит “Hyosung” довести производительность своих установок в 2008г. до 87 тыс.т/год. В то же время Invista, инвестируя 500 млн. долл. США в производство спандекса, в августе 2006 г. запустила новую промышленную линию, а во II квартале 2007 г. запланировала пуск второй [15]. Волокна целлюлозного происхождения (вискозные, ацетатные и др.) в 2006 г. подтвердили тенденцию в части роста производства штапельного волокна и снижения его для текстильных нитей. Общий мировой итог впечатляет - прирост относительно 2005 г. на 5,9% до 3,4 млн.т/год (табл.1). Динамика развития вискозного штапельного волокна ясно показывает путь к подъему: в 2006г. он достиг заметной величины – 9,3% при объеме продукции 2,3 млн.т/год. Более 2/3 объема производства сосредоточено в Азии; в других регионах, кроме США и Японии (табл2), также отмечен подъем. Спрос на вискозное штапельное волокно увеличился не только для нетканых материалов (НМ), но и в связи с появлением особых ассортиментов этих волокон, прежде всего, окрашенных в массе, антибактерицидных, высокомодульных и др. “Tenzel” – целлюлозное волокно нового столетия – продолжало успешно расширять рынки сбыта, например, в сфере изготовления комфортной одежды для спорта и активного отдыха, повседневной одежды и домашнего текстиля. Убыточным становится бизнес в области вискозных текстильных нитей и лишь достаточно надежным выглядит рынок вискозного шинного корда, особенно в Зап. Европе, где прирост его стабилен, но не высок (1-2% в год). Ацетатные волокна, используемые при изготовлении сигаретных фильтров, увеличили в 2006 г. свой объем на 2,6% и впервые превысили рубеж в 700 тыс.тонн [15]. На рыночную долю Северной и Южной Америки приходится 38%, Азии – 34%, Западной и Восточной Европы (включая Россию и Турцию) – 28%. Однако выпуск ацетатных волокон в американском регионе упал на 5,9% в 2006 г., напротив, в Азии, особенно в Китае, он возрос на 15,9%, а в Европе – лишь незначительно (1,2%). По-прежнему растущим спросом пользуются волокна и нити специального назначения, в первую очередь на основе ароматических полиамидов (арамидные) и углеродные, что, естественно, отражается и на объемах их производства. Мировые мощности по выпуску арамидных волокон и нитей обеих типов (пара-арамидные и мета-арамидные) с 2004 по 2006г.г. возросли на 16%, достигнув уровня 85 тыс.т/год (рис.3), в т.ч. по пара-арамидным 62 тыс.т/год, из них комплексных нитей и штапельного волокна (вместе с фибридами-пульпой) 45 и 17 тыс.т/год соответственно [3].
Рис.3. Рост мировых мощностей по арамидным волокнам. Пара-арамидные волокна типа Кевлар (фирма «Du Рont», США) или Тварон (“Tejin”, Япония), характеризуемые высокими модулем упругости, прочностью, тепло-хемо-и огнестойкостью, низкой температурной усадкой и электропроводностью, стабильностью размеров и др., успешно применяются в баллистике, резино-технике для изготовления высокопрочных ниток, канатов, шин, композитов и т.п. Мета-арамидные волокна типа Номекс («Du Рont”) или Конекс (“Tejin”), обладающие устойчивостью к теплу, пламени, химическому, ультрафиолетовому и абразивным воздействиям, низкими усадкой и электропроводностью и др., незаменимы для защитных тканей, фильтров, электроизоляционной бумаги (очень важно для авиационных двигателей). Активность на рынке арамидных волокон и нитей, например за первые 9 месяцев 2006 г., в большей степени отвечала спросу военных и полиции. Компания “Tejin” недавно довела их производство до 23 тыс.т/год и в дальнейшем планирует совместно с “Akzo” расширение его в Нидерландах. Благодаря вводу новых мощностей в период 2004-2008 г.г. в Китае и Ю. Корее мировое производство пара- и мета-арамидных волокон будет постепенно расти, достигнув к концу указанного периода уровня 70 и 30 тыс.т/год соответственно, т.е. – общего прироста по сравнению с 2006 г. ок. 18% (рис.3). Тем самым ожидается примерный баланс между ежегодным приростом мощностей и темпами роста спроса на эту продукцию. Мировое производство углеродных волокон увеличилось по сравнению с предыдущим 2005 г. на 13% до 27,5 тыс. тонн. В ближайшие годы спрос на него возрастет на 15% [9]. Во всех регионах отмечен рост их потребления, где лидирующие позиции занимает Северная Америка с долей примерно 35%, за ней идет Европа (30%), на Японию и остальные страны проходятся оставшиеся 35%. Среди сфер применения на долю аэрокосмического сектора падает ок. 15%, спортивного и туристического – 25%, технического (в т.ч. композитные и армирующие материалы для авиационной, автомобильной, военной и др. промышленности) – 60%. Японская компания “Toray” планируют увеличить выпуск углеродного волокна под торговой маркой «торейсе» на 3х предприятиях – в Японии, Франции и США. Расширение производства, запланированное к началу 2009г., связано с увеличением спроса на эту продукцию, особенно в авиастроении. Совокупная стоимость проекта равна 354 млн.евро. Проект “Toray” предусматривает установку линий по выпуску углеродного волокна производительностью 1800 т/год каждая на дочерних предприятиях “CFA” в США и “Soficar” во Франции. В планы компании входит также строительство в Японии завода по выпуску препрегов (углеродное волокно, пропитанное эпоксидной смолой) в г. Ишикава и расширение аналогичного производства на действующих заводах в г. Ехиме на 400 т, а также ввод там же в эксплуатацию установки получения препрегов мощностью 5,8 млн.м2 в год. В Зап. Европе остается повышенный интерес к углеродному волокну – компании “Lenzing Plastics” (Австрия) и германские “SGL Carbon” и “Kelheim Fibres” создали совместное предприятие по его производству под названием “European Precursor GmbH”. Кратко остановимся на ассортименте сырья для мирового текстильного рынка в 2006 г. В целом по всем видам сырья, включая целлюлозные и синтетические нити для бытового и промышленного назначения, изготовления ковров и т.п., объем производство комплексной нити увеличился на 4,9% до 22,4 млн. тонн. Почти 80% этого объема поступало из Азии. На долю Северной и Южной Америки, а также Западной и Восточной Европы, включая Россию и Турцию, приходится почти по 10%. Преобладающая часть комплексной нити (примерно 79%) используется в текстильной промышленности. В 2006 г. выпуск текстильной нити вырос на 6% до 17,6 млн.тонн, технической – на 5,1% до 2,6 млн.тонн, а ковровой снизился на 3,1% до 2,3 млн.тонн. В сегменте текстильных комплексных нитей преобладает ПЭФ, доля которого составляет 86%, а производство за прошедший год поднялось на 6,5% до 15,2 млн.т, ПА нитей на 4,7% до 1,6 млн.т, в то время как объемы ПП остались практически неизменными, а целлюлозных продолжали падение вниз более чем на 3%. Ведущие поставщики ПЭФ текстильной нити – Китай и Индия – произвели дополнительно 1,4 млн.т (прирост на 15% для каждой из этих стран) и теперь на их долю приходится ¾ мирового рынка. Доля Азии в выпуске ПА текстильной нити также выросла и составила 73%, причем указанный прирост практически принадлежит одному Китаю (табл.2). Мировой объем выпуска высокопрочных технических нитей, где помимо ПЭФ и ПА, присутствуют ПП, вискозная и углеродная нити, в 2006 г. увеличился на 5,1% до 2,6 млн.т. В автомобильной промышленности их потребление выросло на 4%. Эта отрасль базируется преимущественно на ПА и ПЭФ нитях, которые занимают почти 85% данного рынка. Рост ПЭФ по сравнению с 2005 г. составил 7,3% до 1,1 млн.т, а ПА – 4,5%, немного превысив 1,1 млн.т [15]. В Северной и Южной Америке отмечено сильное снижение производства ПА технических нитей, составившее 5%. В США, согласно табл.3, выпуск ПЭФ технической нити сократился на 8,8%, а импорт возрос на 5% до 80 тыс.тонн. Внутреннее потребление в этой стране шинного корда из ПЭФ уменьшилось в 2006 г. на 19% до 67,5 тыс.т, а ПА – на 18% до 26 тыс.т [14]. Сегодня доля азиатских стран на рынке технических (кордных) нитей явно преобладает: по ПА – 60%, по ПЭФ -55%, в то время как европейский (включая Россию и Турцию) и американский регионы постепенно теряют здесь свои позиции. Характерным является активное расширение продаж ПЭФ технических (кордных) нитей в страны, не имеющие собственного их производства, но обладающие развернутой сетью перерабатывающих предприятий. Например, в 2006 г. поставки упомянутой продукции в Аргентину выросли на 32% до 5,2 тыс.т, в Австралию на 41% до 3,3тыс. в Италию на 2% до 10,1 тыс.т и в Португалию на 11,8% до 10,7 тыс.т [15]. Как будет показано ниже, Россия также зависима от импорта ПЭФ технических нитей, как для промышленности РТИ (табл.4), так и шин (табл.5). На рынке ковровой нити (т.н. ковровый жгутик – BCF) в 2006 г. отмечено снижение уровня потребления как ПП, так и ПА нитей – суммарно на 3,1% до 2,3 млн.тонн. Хотя спрос на ПЭФ ковровую нить увеличился, объем его остается небольшим, но все-таки вселяет оптимизм ввиду более низкой цены полимерного сырья (ПЭТ) и возможности изготовления модных ковров с длинным ворсом. Производство нетканых материалов (НМ) продолжает динамично развиваться [18]. Особенно впечатляет ситуация в Китае: количество установок получения НМ по сравнению с 2004 увеличилось на 118 или 33%, и в настоящее время составляет 476 при объеме выпуска НМ в стране ок. 1,4 млн.т. При этом опережающими темпами растет производство НМ по методам спанбонд и спанлейс: с 2005 по 2006 г.г. соответственно на 20 и 15% (!).
Рис.4. Мировое производство нетканых материалов по регионам (2006 г. – суммарно 6,6 млн.т). Мировое производство НМ всех видов за прошлый год поднялось на 8% до 6,6.млн.тонн с региональной структурой, иллюстрированной рис.4, где более 2/3 занимают Азия и Европа. До настоящего времени ведущее положение в мире занимают НМ, получаемые по т.н. «кардинговой» схеме, где в качестве исходного сырья используют различные виды натуральных и химических волокон (преимущественно ПП и ПЭФ), перерабатываемые в дальнейшем по классической схеме кардо-чесания и скрепления волокнистой массы. Среди последних наиболее известны иглопробивной, спанлейс (гидроструйный), термо-или химическое соединение. Если в 2000г. их доля составляла соответственно 42;13 и 45%, то в 2006г. она заметно изменилась в пользу спанлейс – соответственно 45;25 и 30%. Тем не менее, постепенно повышается доля НМ, изготавливаемых по технологии спанлайд прямым формованием из расплавов полимеров, главным образом ПП и ПЭФ (спанбонд, мелтблаун, SMS и т.п.). По технологии спанлайд в 2006 г. было произведено почти 2,2 млн.тонн НМ (в основном спанбонда из ПП), что соответствовало приросту на 9% к уровню 2005г. Заметим, что в данный момент рыночная доля ПП в производстве спанбонда ок. 80% [15]. ХИМИЧЕСКИЕ ВОЛОКНА-2006: СНГ ХИМИЧЕСКИЕ ВОЛОКНА-2006: Россия |