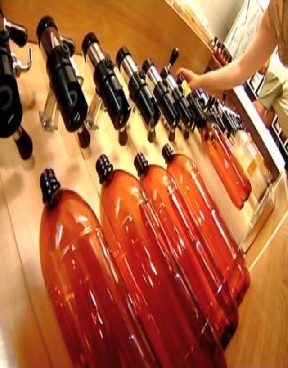
Инвестор - группа компаний «Марийский НПЗ». Мощность завода составляет 220 тыс. т в год. Планируется выпуск исключительно бутылочных марок ПЭТФ. Завод входит в число самых передовых в мире предприятий по производству ПЭТФ, которые используют так называемую «одностадийную» технологию, разработанную компанией Uhde. Технологический процесс синтеза ПЭТФ пищевого назначения 2R MTR компании Uhde Inventa-Fischer GmbH состоит из следующих этапов: 1) Приготовление катализатора и стабилизатора – порошкообразный или жидкий катализатор, а также стабилизатор и добавки растворяются в гликоле при повышенной температуре. Раствор направляется в резервуары и далее для смешивания с основным сырьем. 2) Смешивание пасты - ТФК, изофталевая кислота (ИФК), раствор гликолей с катализаторами и стабилизаторами перемешиваются в емкости в определенном соотношении. Емкость оборудована специальной конструкцией, которая обеспечивает образование однородной пастообразной массы. 3) Этерификация и поликонденсация (двухреакторная технология) - основными аппаратами реакционной системы этерификации и поликонденсации являются запатентованные Компанией реакторы ESPREE® и DISCAGE®. Паста поступает в нижнюю часть реактора ESPREE® колонного типа, где происходит реакция этерификации при температуре до 270 градусов Цельсия. Окончательная вязкость полимера достигается в реакторе DISCAGE®, в котором продукт находится под вакуумом. Данный реактор оснащен мешалкой коробчато-клеточного типа без центрального вала с редукторным двигателем и инверторным приводом, оснащенной многочисленным перфорированными дисками и съемниками, действующий как винтовой конвейер. Это позволяет транспортировать полимер со стороны низкой вязкости в сторону высокой вязкости, а затем через разгрузочный желоб в аппарат резки (гранулирования). 4) гранулирование и кристаллизация - в аппарате резки поток расплава продавливается через перфорированную плиту в резательную камеру, через которую течет горячая вода (подводное гранулирование). Установленная за перфорированной плитой ротационная резальная головка режет жгуты полимера в гранулы, которые при контакте с ножом остывают и приобретают типичную сферическую форму. Далее гранулят направляется в центробежную сферическую сушилку, где происходит отвод технологической воды. Затем высушенный горячий гранулят выгружается из сушилки и кристаллизуется на виброконвейере. Гранулят собирается в термостатированном бункере, откуда подается в силос кондиционирования с помощью пневмотранспортной системы. 5) Кондиционирование гранулята - в силосе кондиционирования гранулят в противотоке обдувается воздухом с постоянной температурой для снижения содержания ацетальдегида без повышения вязкости полимера. Из силоса кондиционирования гранулят поступает в охладитель и затем в силосы хранения. Гранулят готов к растарке в транспортную упаковку. Управление одностадийным технологическим процессом полностью автоматизировано от момента загрузки сырья до упаковки товарного продукта в транспортную тару.
Технология 2R MTR позволяет снизить расходы на производство ПЭТФ по приведенным ниже причинам: * Отсутствие потерь готовой продукции на стадии твердофазной дополиконденсации (SSP) - до 7 кг на тонну произведенного продукта. * Отсутствие затрат энергии на с тадии твердофазной дополиконденсации (SSP), что позволяет экономить при производстве 1 метрической тонны ПЭТФ до:
- 50кВт электроэнергии, - 9 кг топочного мазута, - 0,6 кубического метра воды, - 30 кг пара.
* Экономия сырья в процессе синтеза 1 метрической тонны ПЭТФ до:
- 8 кг моноэтилен гликоля, - 4 кг терефталевой кислоты
Ознакомиться с российским рынком полиэтилентерефталата Вы можете в исследовании: «Анализ рынка ПЭТФ в России в 2008-2009 гг.» Светлана Коротаева, www.polymery.ru |